JuryriggedSean
New Member
I'm hoping someone on the island might be able to help getting a hole bored in my headstock .
I've got the 2 slabs ganged with bolts and the position marked. The size is 8" x 12" with the hole center to be 9" from one end. It is in mild/A36 steel, each piece 5/8" thick.
I'll need it bored to 1.98" for my bearing cups, then I'll build up the rest of the headstock.
I can do any prep work or change as requested before getting it done.
I did talk to one person who could do it towards the end of Sept, but maybe someone could give me an assist before then. I'm open to compensation if desired.
Muchas gracias.
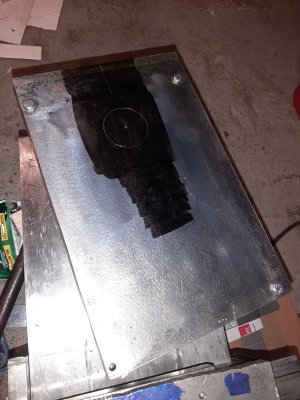
I've got the 2 slabs ganged with bolts and the position marked. The size is 8" x 12" with the hole center to be 9" from one end. It is in mild/A36 steel, each piece 5/8" thick.
I'll need it bored to 1.98" for my bearing cups, then I'll build up the rest of the headstock.
I can do any prep work or change as requested before getting it done.
I did talk to one person who could do it towards the end of Sept, but maybe someone could give me an assist before then. I'm open to compensation if desired.
Muchas gracias.
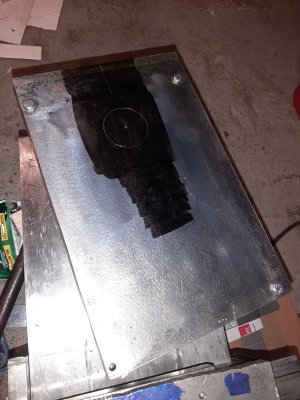