Brent H
Ultra Member
So I purchased a Vevor BS-0 or 1 to help making gears and such as my 12” dividing head is very heavy with an 8” chuck. Mailed from BC it arrived today - impressive 5 days across Canada BC to NB
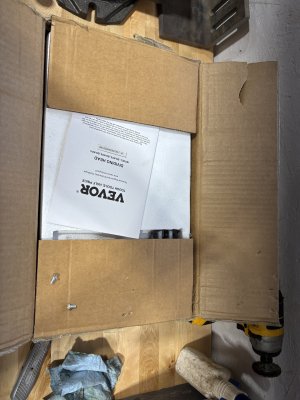
Box opening and there are 2 loose screws - they seem to fit nothing other than possibly the dividing plates? Here is the box markers:
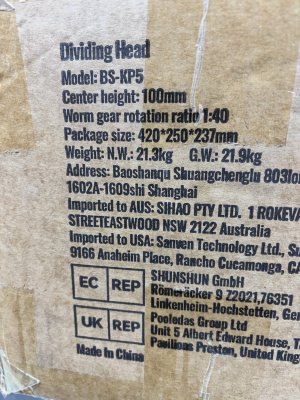
So the dividing plates were all right and range from 31 to 49 holes (have to confirm) and you get 3 with 6 lines of holes. I had to clear swarf out of 2 of them but they look fine
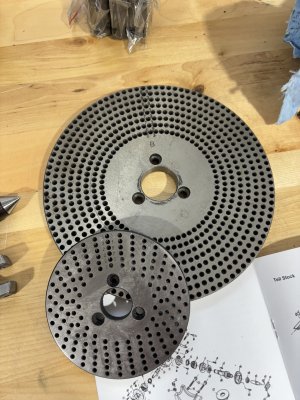
The index plunger was stiff and needed some tuning up - might need a better spring (like a bit more load pressure). The pressure clip that holds the clock arms in place was too big for the application and I had to grind off about 3/32 to 1/8 off the outer edge to get a solid fit and no interference with the clock arms. I changed out the allen screw holding the plunger with a set screw and changed the stupid Phillips head lock screw with a allen head cap screw.
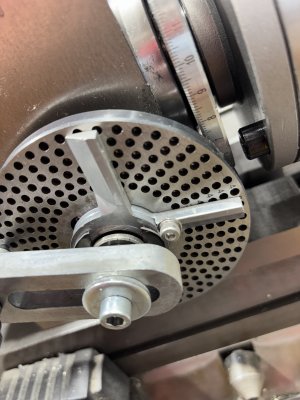
Size difference is huge which will help my back as well as allow full use of the mill height.
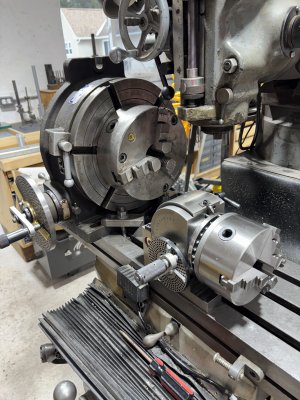
It dialled out at 0.001” run out and I will be checking things out further. It has some backlash (0.020 ish) so it is important to keep your turning direction consistent. I will have more to say as Input this unit into fabrication
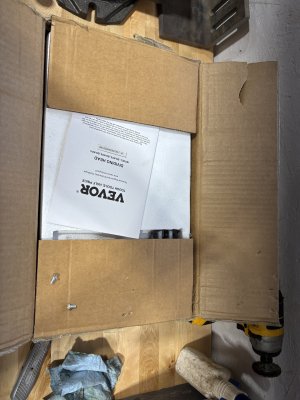
Box opening and there are 2 loose screws - they seem to fit nothing other than possibly the dividing plates? Here is the box markers:
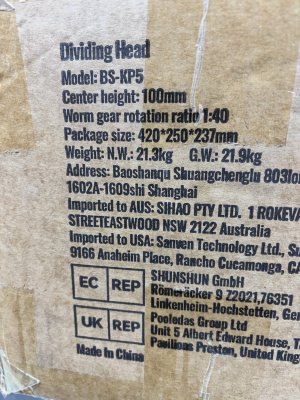
So the dividing plates were all right and range from 31 to 49 holes (have to confirm) and you get 3 with 6 lines of holes. I had to clear swarf out of 2 of them but they look fine
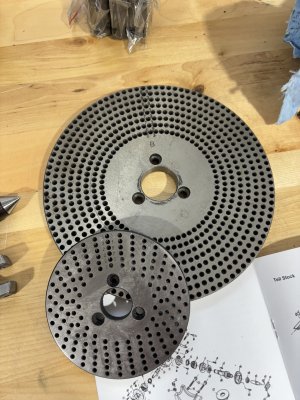
The index plunger was stiff and needed some tuning up - might need a better spring (like a bit more load pressure). The pressure clip that holds the clock arms in place was too big for the application and I had to grind off about 3/32 to 1/8 off the outer edge to get a solid fit and no interference with the clock arms. I changed out the allen screw holding the plunger with a set screw and changed the stupid Phillips head lock screw with a allen head cap screw.
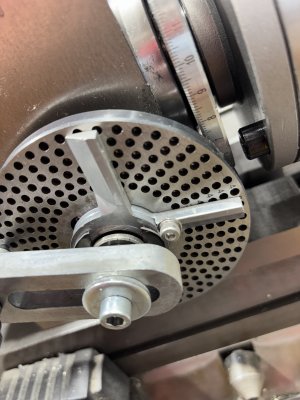
Size difference is huge which will help my back as well as allow full use of the mill height.
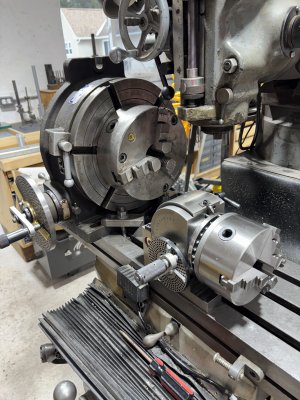
It dialled out at 0.001” run out and I will be checking things out further. It has some backlash (0.020 ish) so it is important to keep your turning direction consistent. I will have more to say as Input this unit into fabrication