I'm milling out a the outside contour for a big bracket clamp. It is about 4" across. 0.05" plunge depth per trip around the outside of the part. The plunge is defaulted to be a ramp but with only a 0.04 radius. It goes THUNK into the cut. See the green preview in the simulation screen shot - the tool enters on the left sliding in and down from the very left. I'm thinking that I could change the radius to 0.25" and maybe it would be a lot smoother. I wonder if I'm damaging the EM doing this? Why does fusion default to 1/10 of the cutter diameter for the lead ins? wouldn't more generally be preferred? Oh and it's 15" per min and 5000 rpm. 12mm EM. Aluminium.
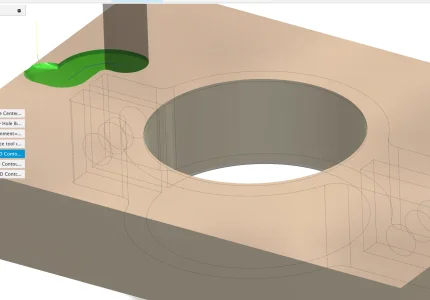
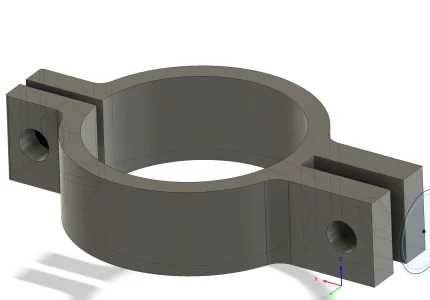
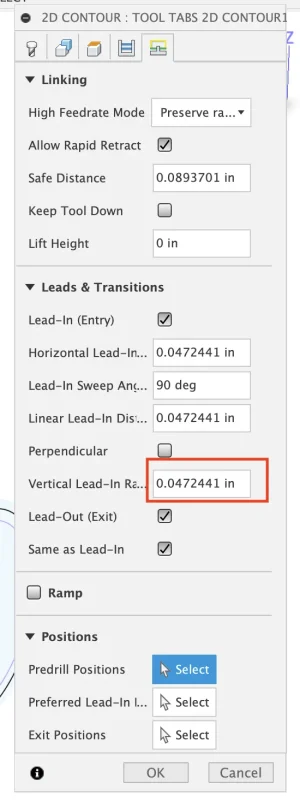
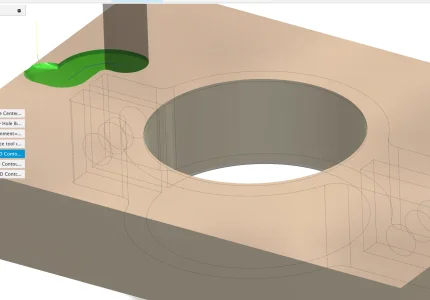
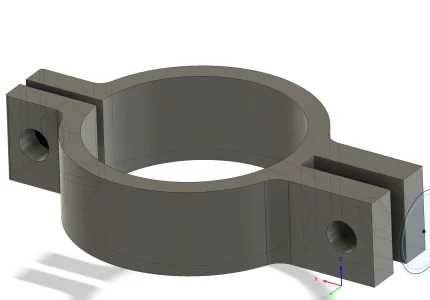
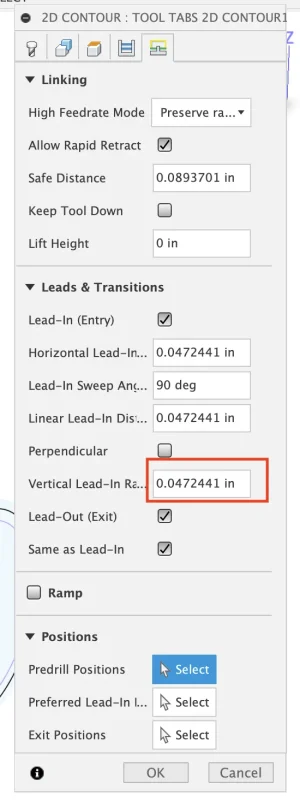