My first experience with a truly sharp, well-ground HSS tool was a total eye-opener. I was able to cut deeper and more easily than I ever thought possible on my South Bend 10K. It is definitely the mainstay in my shop.
just for kicks, here's taking a 1.3125" DOC, .005 feed with a HSS bit. lots of rake via a big chip breaker. (admittedly, not a brilliant move pushing a machine to see what I can do, but the DSG didn't sound like it cared). Third pic....last weekend...cutting 57.6 x 3mm internal thread, lathe spindle back plate, which is a coarse thread by my standards. chipped two expensive crappy Criterion carbide internal thread tools before smartening up and grinding a proper hss bit.
on some forums the carbide/hss thing seems to be like guys rooting for their favourite team. I always thought that was wrong; they are just tools, understand the pros and cons of both and select the most appropriate for the job. As home shop guys, factoring in cost is also sensible - we're not hustling to cover overheads like a commercial shop
So what do you do when you get close and want to make a very light or few light cuts as you sneak up on a specific size? Do you switch to HSS?
SOP for most would be to not switch (100% for commercial shops). You're say 40 thou over, infeed 10 and measure. Then compensate on the last cut for how far off 20 thou targeted dim change you were. That's SOP. However, often I do switch when a lot of precision needed (say, fit for very expensive p4 AC bearings). I use a hss tool honed to fine edge and 10ths indicator on the infeed. btw, "creeping up on it" is I think frowned up by the commercial guys. It takes more time, but does work...the fineness of you DOC is function of the fineness of the tool edge; creeping works beautifully if you put the right edge on the tool. That works for carbide too...and 1/10 of thou DOC is not only doable, but a regular occurrence - just ask anyone who scrapes (but of course its a function of the edge which has to be there).
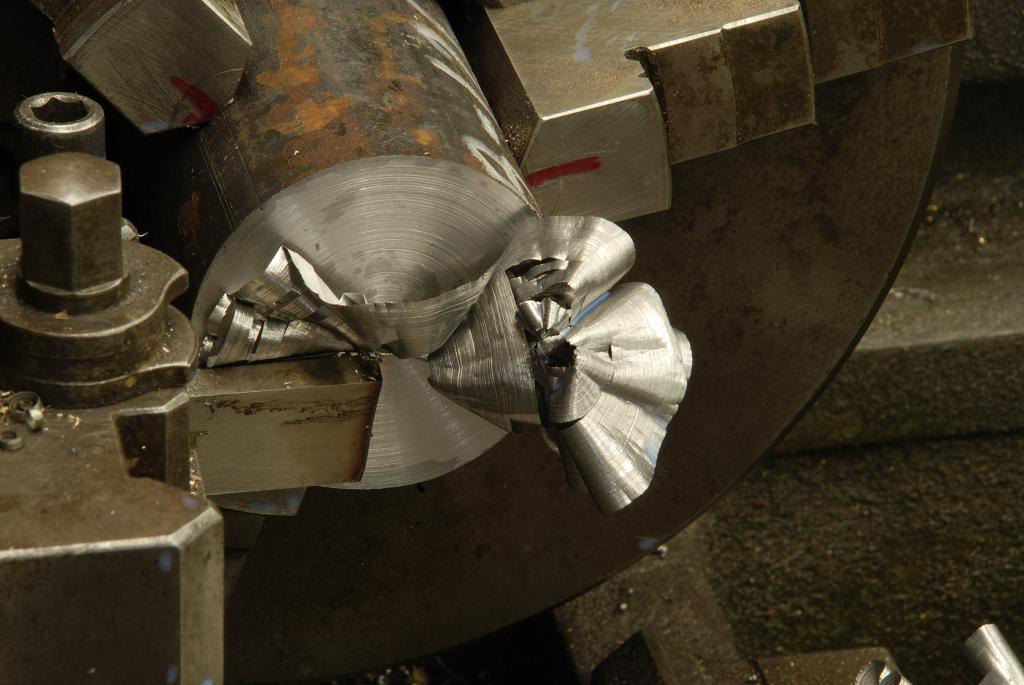

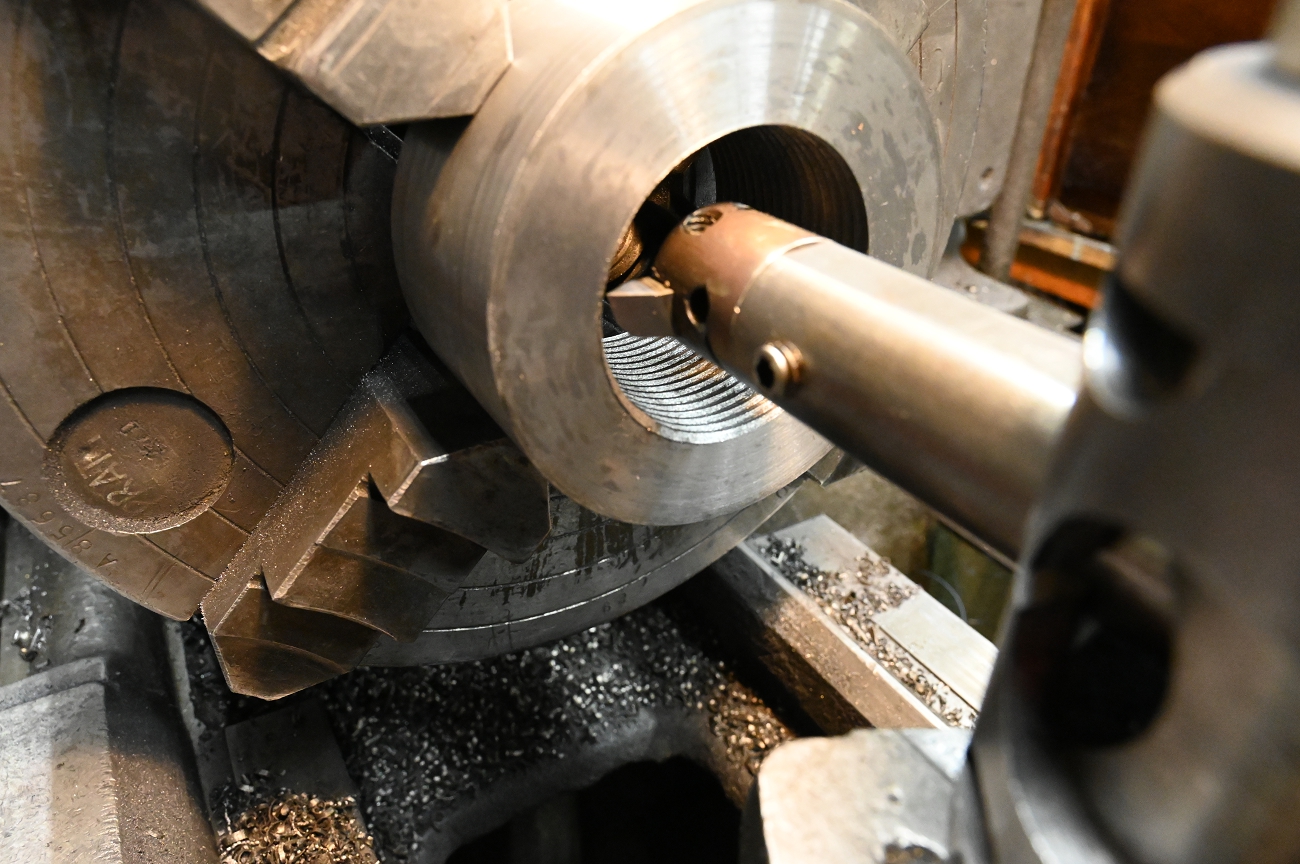
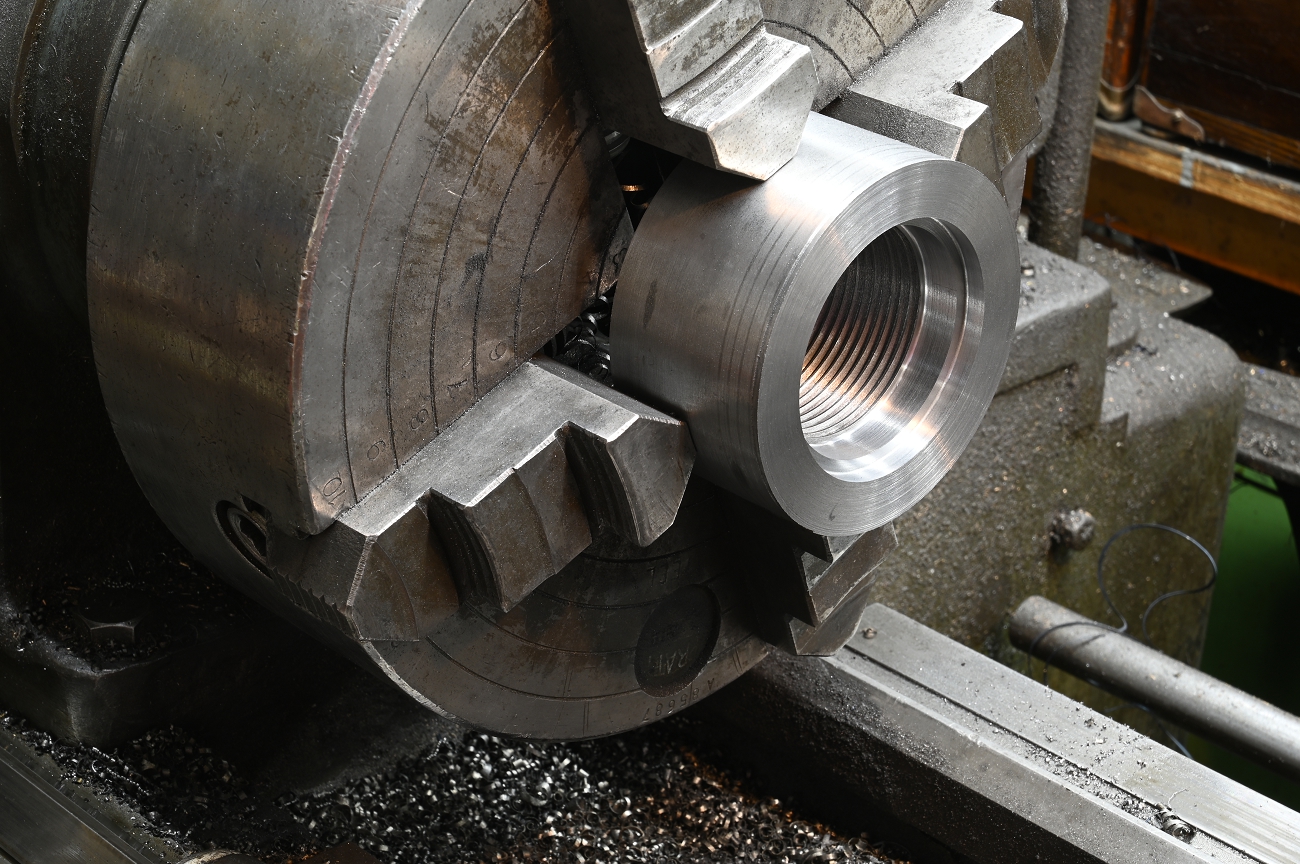
Last edited: