Dan Dubeau
Ultra Member
New coworker was getting rid of his old kennedy. As much as I hate them, it's a much better fit for the hutch above my workbench, so I bought it and swapped it out for my 2 drawer mechanics kennedy.
I also picked up a right angle head for my Excello. Saw it advertised last week for $225, and drove up to get it. The guy had bought it for his taiwan b-port clone, and it didn't fit (Excello's have bigger diam quills). Owner before him had turned the r8 adapter down to a straight shank for some reason (and was just using the drawbar thread to drive it apparently....), and it also felt really tight, so I offered $100 with these issues in mind but he didn't take it. We chatted for a while about machining, jobs etc, and he mentioned he needed some cad work done so I offered to do the modeling in exchange for the head for $100. He said he'd think about it, then contacted me this week and said sure, so I whipped up the parts he wanted modeled, and drove up after work to pick it up. I'll know more when I get inside of it, but I'm not the first one inside of it obviously.... It's very tight spinning, but I'm hoping it's just a preload problem, and that nothing is damaged inside. I'll also have to make an r8 shank for it, but that shouldn't be a problem. For $100, I'll take the issues in stride.
It's not a pretty show piece, but neither is my mill. I think they look good together
. Didn't plan on buying anything this week, but that's the way she goes.....
Now I need to get back to some other projects this weekend after a few weeks doing other things. So much to catch up on...
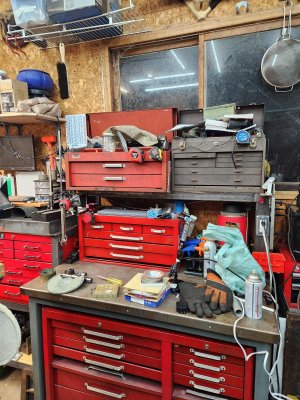
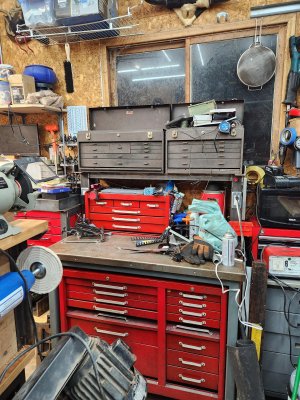
I also picked up a right angle head for my Excello. Saw it advertised last week for $225, and drove up to get it. The guy had bought it for his taiwan b-port clone, and it didn't fit (Excello's have bigger diam quills). Owner before him had turned the r8 adapter down to a straight shank for some reason (and was just using the drawbar thread to drive it apparently....), and it also felt really tight, so I offered $100 with these issues in mind but he didn't take it. We chatted for a while about machining, jobs etc, and he mentioned he needed some cad work done so I offered to do the modeling in exchange for the head for $100. He said he'd think about it, then contacted me this week and said sure, so I whipped up the parts he wanted modeled, and drove up after work to pick it up. I'll know more when I get inside of it, but I'm not the first one inside of it obviously.... It's very tight spinning, but I'm hoping it's just a preload problem, and that nothing is damaged inside. I'll also have to make an r8 shank for it, but that shouldn't be a problem. For $100, I'll take the issues in stride.
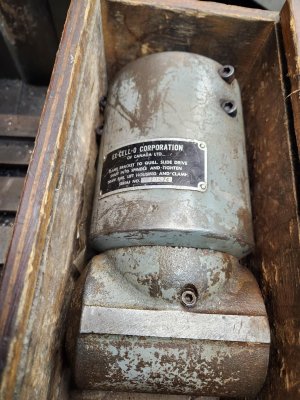
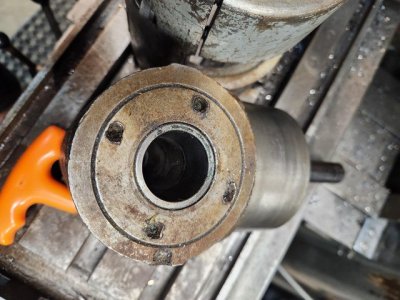
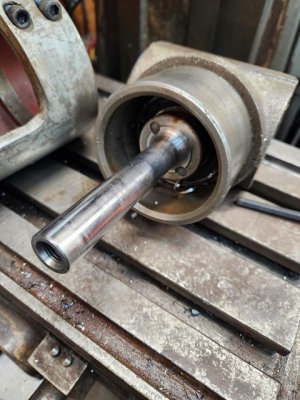
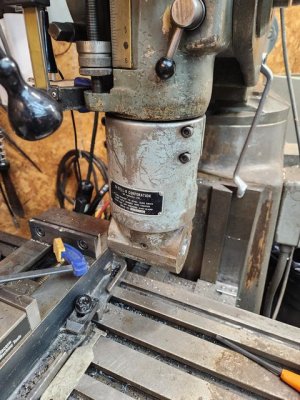
It's not a pretty show piece, but neither is my mill. I think they look good together
Now I need to get back to some other projects this weekend after a few weeks doing other things. So much to catch up on...