ThirtyOneDriver
Johnathan (John)
Posts to the "Intros" forum and my 7 page thread keep bumping other new member's posts and I'd like to stop doing that. My intent is to continue that thread here and keep my projects and the related questions in one spot.
Of course, I'm still a "Cambridge - machinist newb" so feel free to jump in and help me learn - I'll try to be as transparent as I can with my ideas and how I'm thinking about doing something that I'm not 100% confident about and hopefully experience and knowledge from the forum members will reduce mistakes/improve my efficiency.
Thank you to everyone for their assistance and support; it has a distinct impact on how quickly I'm learning, the costs of my tooling, and my ability to complete tasks.
Older thread:
canadianhobbymetalworkers.com
My to do list:
Of course, I'm still a "Cambridge - machinist newb" so feel free to jump in and help me learn - I'll try to be as transparent as I can with my ideas and how I'm thinking about doing something that I'm not 100% confident about and hopefully experience and knowledge from the forum members will reduce mistakes/improve my efficiency.
Thank you to everyone for their assistance and support; it has a distinct impact on how quickly I'm learning, the costs of my tooling, and my ability to complete tasks.
Older thread:
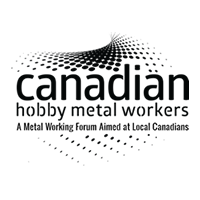
Cambridge - machinist newb
Another thing I missed dropping off the thread like I did....... There is no T-slot. Gunna have to re-read the whole thread I think.
My to do list:
This being buried on the fourth/fifth page of an intro is convenient for me - there could be other places to post it, but I'd rather not start any new threads.
Again, so very thankful to have found this group of people - I've needed someone(s) to bounce ideas off of, to share my success and share my fails with. If you haven't caught on yet - staying focused is a challenge for me, I'm either struggling or super super engaged to the point where I'm forgetting to eat and the back injury makes it really hard to get in the state of 'hyper focus'.
I've been planning on building a shop to build racecars in for at least 24 years and am finally getting to do it - that also means I have 24 years of ideas/plans/goals to work through. I've written all of these out for myself previously and it's been cool to see how accurate some of the accomplishments have been a few years later having completely forgotten that I had previously planned/researched (the lathe an milling machine I bought were the same ones I hypothetically decided on in 2017).
So here's a list of SOME of the stuff I'm currently pursuing; I'll post pictures of the shop, equipment, toys, etc. and continue to ask silly questions.
Shop build:
Bathroom install
- trench water and new electrical into shop (100 amp shop panel has already been upgraded) (new electrical includes separate conduit for low voltage wiring)
Complete protective framing and paneling (plastic/vinyl diaper style insulation on a steel beam building; paneling to protect from sparks/heat but has other advantages)
Build barrier wall to help contain machining mess/create a "clean" assembly area for automotive parts (differential assy, calipers, master cylinders, other components)
Install racking on wall for tube lengths
Propane tank reinstallation
- add leveling material, level, compact
- propane tank installation
- gas line extension and hook-up
Future: organize and customize 40' sea container that was recently installed (created the propane tank project)
Shop equipment:
48" high scale/load cell pads (future capability of compressing the suspension against itself by placing beams under the load cell pads and drawing the beams up to the frame creating force but not weight - may or may not use load cells in the process... higher capacity racing scale systems, or at least high enough to pull against, are about $5k and there's other things that I'd like to prioritize)
- assists in alignment... we're trying to align the car to create the most amount of grip in the corners; if we align it (kind of like measuring using a base plate) how it's going to run down the straightaways we're not being very accurate
- identifies binds/flexes (we have a better chance of identifying chassis flex and the inherent inaccuracy created by it)
- these have been built and used, but not finished or prepared for the "pull-down" aspect
48" box and pan brake (needs mobile base fabricated)
CX 611 milling machine (needs mobile base fabricated)
- DRO
- power feed
- coolant system?
- CNC retrofit?
- learn to maintain and operate it
- quill mechanism broken/never operated properly - determine if it's needed and repair if necessary (something to do w/ the fine feed, wouldn't disengage)
CX 709x lathe (needs mobile base fabricated)
- install QCTP tool post
- DRO
- learn to maintain and operate
- replace motor to enable more spindle speeds/RPMs?
CX 116
- coolant system?
- maintain
*by mobile bases I mean something like a 2"x2" tube frame w/ levelling feet that I can attach the equipment to and move if it's necessary; they don't need to have casters on them because they likely won't be moved very often... (exception the box and pan brake) ability to move them is an "in case"... raising them to more appropriate working heights, providing the equipment w/ stable bases and the ability to level are the necessary tasks
Lincoln 225 TIG/Stick
- repair gas solenoid (ordered)
- fab mobile cart
- distant future upgrade (Aspect/inverter ~300amp AC/DC TIG)
Lincoln 180 MIG
- replace it's version of a mother board
- send it to Dad so he has a welder
- distant future upgrade to (ideally) an LE 260 a 256 may be another option
Lincoln 275 Plasma
- cart/add to 225 cart
Lincoln 180 MIG (#2)
- fabricate cart
oxy acy bottles/torch
- fabricate cart
*I like things on wheels... many, many carts apparently
JD2 Model 3 bender
- mod stand
- have 1.75" x 6.5 clr dies
- 1" dies have been ordered and shipped
- design organization for air/hydraulic pump and hydraulic ram (if needed)
12 ton hydraulic shop press
- machine adapter for press brake finger and mate
- fabricate mobile base?
Hoist
- machine internal threaded adapter to replace bent one
Chassis table/frame jig/surface plate (7'x16', 6"channel topped w/ 5/16" plate)
- fab/install leveling feet/legs (machine jacks? - needs enough height for hoist legs to go under - risk of breaking/bending leveling legs if they protrude below bottom plane when moving w/ tractor)
- fab/install attachments to facilitate moving w/ tractor (weighs 2700#)
- score/grind/cut/some method permanent center line
- score/grind/cut/some method permanent front and rear axle lines (needs to be square, I'd like to avoid protrusion from surface)
Rearend fabricating fixture (fab mobile base)
Spindle fabricating/measuring fixture
- design and fabricate
Control arm fabrication fixture
- design and fabricate
Other misc. shop stuff as needed (brackets, hangers, etc.)
Car builds:
'96 Harley - repair/rebuild carb
'71 C10 - retromod build for wife; complete body, move firewall, 6.0L LS swap, build frame, tubular upper and lower control arms, Ford 9"... $15k for parts set aside, most parts in shop/sea can
'69 C20 - power steering box rebuild, rear brakes rebuild - sold
Street Stock - '88 Monte Carlo based stock car build for friend's 11 yr old son - may/may not happen - responsible for frame, cage and body fabrication
Late Model - brand new (built in 2018, still bare) NASCAR Pinty's Series chassis from reputable builder (great deal... bought at cost of material essentially) - build for self
- I have majority of components to assemble but this is just a cage/frame and needs a lot of fabrication
- engine I have/willing to spend $ for is underpowered but has 150# weight advantage (minimum weight of the car is only 2850# instead of 3000#) ... considerable effort must be made to take advantage of the weight savings and make the smaller engine package competitive (meaning lightening parts where possible by machining)
- can make molds for vacuum forming composite parts using big 3D printer (recently purchased) (friend makes composite windmill blades & components for luxury yachts)
- creating data logging Arduino to replace gauges w/ LEDs (engineer friend assisting when he's in country) (race car drivers don't read gauges... different coloured idiot lights work better; green=good, red=bad, orange=concern, blue=cold) lighter and 1/10th the cost of gauges - data logging capability may be limited to practice use only, would provide data to establish chassis heights, etc. for pull down system described above
- build rearend in previously fabricated fixture
- build own lower and upper control arms, possibly own center link, idler arm and pinion arm
- modify/build other parts that I can't be specific about (welding, plasma CNC cutting, machining, 3D printing, vacuum forming - necessary equipment may need fabricated for these)
Crew Cab dually - replace/repair (San Diego trip for wedding in future best opportunity for replace)
Open car trailer - purchase/modify for racing (had commissioned one 2 years ago, fabricator kept deposit and flaked)
Enclosed car trailer - empty into sea can - have reskinned, re-axled (connection teaches trailer repairs, needs work for demo/practical)
Dirt bike(s) - mine's at friend's shop for engine enhancements, wife's (same model) needs seasonal maintenance
Track car project - back burner'd while life happens - project w/ friend... crazy ideas using cheap, readily available, reliable components - a "f" you to another friend type of project "can't be done" he says
Plus, plus, plus