calgaryguy
Chris
Im aligning my tailstock by machining a piece 'between centers'. MT3 dead center in the headstock and a MT2 live center in the tailstock. Drive plate and drive dog installed per the pic below.
I've eliminated any taper on the shaft by adjusting the tailstock adjustment allen screws located on each side of the base of the tailstock.
When I was done aligning, I removed the shaft/drive dog and , out of curiousity pushed the tailstock up close to the MT3 center in the headstock and tightened down the tailstock. I then extended the tailstock quill with the livecenter in it out until it was almost touching the headstock dead center. Looking down on the two centers from right above their contact area I was surprised to see the tips of the two centers out of alignment - the tailstock tip was closer to the back of the machine by about .010-.015 ('calibrated eye measurement).
I guess I just assumed that once the tailstock was aligned using the 'turning between centers' method that I'd see the tips of the centers in very close alignment when brought together.
Am I off base here?
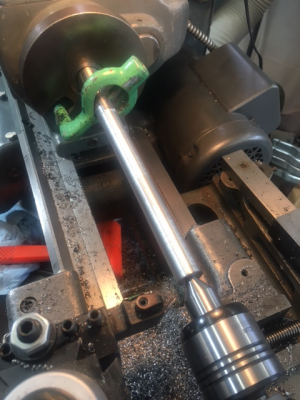
I've eliminated any taper on the shaft by adjusting the tailstock adjustment allen screws located on each side of the base of the tailstock.
When I was done aligning, I removed the shaft/drive dog and , out of curiousity pushed the tailstock up close to the MT3 center in the headstock and tightened down the tailstock. I then extended the tailstock quill with the livecenter in it out until it was almost touching the headstock dead center. Looking down on the two centers from right above their contact area I was surprised to see the tips of the two centers out of alignment - the tailstock tip was closer to the back of the machine by about .010-.015 ('calibrated eye measurement).
I guess I just assumed that once the tailstock was aligned using the 'turning between centers' method that I'd see the tips of the centers in very close alignment when brought together.
Am I off base here?