Thanks to those who provided comments on my first version of my stand design:
Stand Design for benchtop Mill- looking for feedback
and gently pointed out that my design sucked-LOL.
Version 2 is ready for feedback!
It has:
- 2"x2"x1/4" thick square tubing for the sides and hopefully the legs as well (I already purchased this based on the rejected Revision 1 design...)
- The cross members bolt on so the stand can be pulled apart.
- Plywood slides so that full extension slides for the drawers (not shown in below) can be attached.
- Wooden top (already purchased, that I like the look of).
- @LenVW suggested that ballast might be helpful, so it has provisions for including that.
Based on my experience with my woodworking bench, I think there's enough overhang so I don't hit my feet on the front? See images below.
Below is a detailed view, showing how I'm proposing to put everything together. The model is not finished, it doesn't have things like the bolted joints or parts cut so they don't interfere.
In above, I added some 1/2" plate for attaching the feet. I'm not too keen on the overhang, but I haven't thought of a better way to allow for adjustment of the feet and not have the feet hit the wall. Hopefully after thinking about it more I'll come up with a better way.
Stand Design for benchtop Mill- looking for feedback
and gently pointed out that my design sucked-LOL.
Version 2 is ready for feedback!
It has:
- 2"x2"x1/4" thick square tubing for the sides and hopefully the legs as well (I already purchased this based on the rejected Revision 1 design...)
- The cross members bolt on so the stand can be pulled apart.
- Plywood slides so that full extension slides for the drawers (not shown in below) can be attached.
- Wooden top (already purchased, that I like the look of).
- @LenVW suggested that ballast might be helpful, so it has provisions for including that.
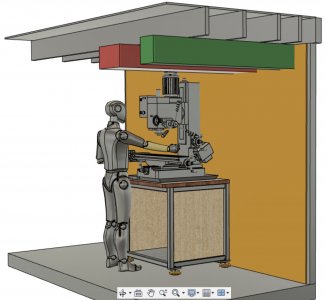
Based on my experience with my woodworking bench, I think there's enough overhang so I don't hit my feet on the front? See images below.
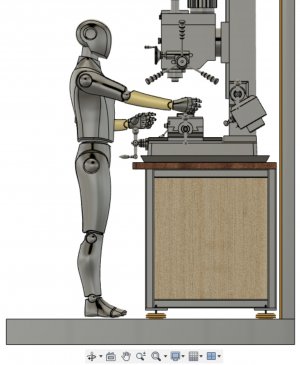
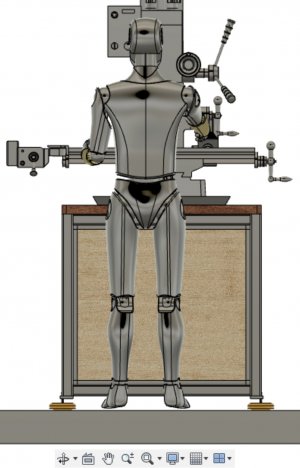
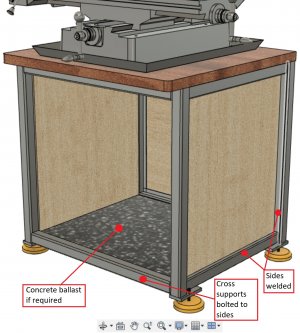
Below is a detailed view, showing how I'm proposing to put everything together. The model is not finished, it doesn't have things like the bolted joints or parts cut so they don't interfere.
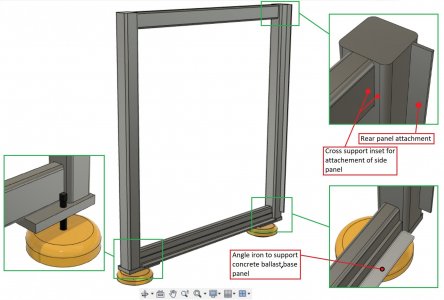
In above, I added some 1/2" plate for attaching the feet. I'm not too keen on the overhang, but I haven't thought of a better way to allow for adjustment of the feet and not have the feet hit the wall. Hopefully after thinking about it more I'll come up with a better way.