Is anyone on the forum running one of these (typically Chinese) ER collet spindle / vfd combos like pic?
I've been checking out websites & YouTube vids, just curious about a few things as the feedback seems to vary. BTW, I don't have a cnc router/mill & not really contemplating a build. I'm kind of curious about the motor for other purposes.
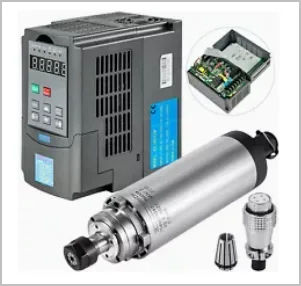
I've been checking out websites & YouTube vids, just curious about a few things as the feedback seems to vary. BTW, I don't have a cnc router/mill & not really contemplating a build. I'm kind of curious about the motor for other purposes.
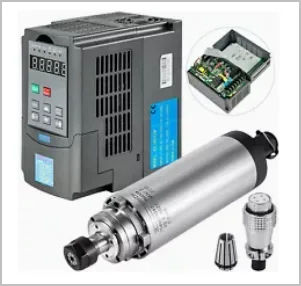