I was asked to make an adapter out of PVC for a sensor. This adapter fits into a special opening in a tank and it supports the sensor.
There are to be 4” MPT on a section of the outside and G1 BSP for the sensor in the cavity of the adapter.
I started by making a G1 BSP gage out of aluminum so that I’d have a way to “measure“ the internal thread later. Had to grind a 55* tool on the T&CG. I made it out of HSS and used it for both the external thread here and later in a threading bar for the internal thread. The thread was made as close as I could to the standard as published in technical manuals. I used the three wire method to measure it accurately.
Next I got the PVC stock set up in the lathe and roughed out the adapter at the end of the slug. The necked down (cylindrical) part is to dimension (it includes about 3/4” extra length at the base for work holding later during the internal machining) and the lager section needs to be taper turned to accept the MPT.
PVC produces strings, no matter what you do. The problem arises when the stuff can’t clear the cutting tool and starts to “weld” itself back into the part because it heats up very fast to its plastic temperature. This was especially tricky when I bored the recess in the next op.
Using the taper attachment to thread 4” MPT.
This completed the external work other than finish to length.
Now I cut the part off the slug on the bandsaw and mounted it back in the 4J by holding onto the ~ 3/4” machining allowance. This reduced the stick out to an acceptable level. Bored the recess and then worked on the internal G1 BSP thread at the base of the adapter.
The gage made previously was used to check the dimension of this thread. The threading tool seen in the boring bar is the same as was used to make the gage.
Once the internal work was complete, the part was flipped 180* and held internally in the 4J. The machining allowance was now parted off and the bottom faced to bring the part to final length.
There are 4 holes in the face of the part for a pin spanner to tighten it into the tank’s opening. These were drilled on the mill.
Couple more pictures of the finished part.
So what did I learn?
PVC turns very well. Strings need to be controlled otherwise they weld themselves back where you don’t want them and create chatter. Carbide tooling suitable for aluminum or stainless steel works well on PVC. So does sharp HSS. The biggest DoC I tried was 5mm; it worked, but the strings get very soft and can start to cause problems. So I reduced the max to 3mm. The maximum rpm was 770. The strings get too soft above that. No coolant or cutting fluid was used.
There are to be 4” MPT on a section of the outside and G1 BSP for the sensor in the cavity of the adapter.
I started by making a G1 BSP gage out of aluminum so that I’d have a way to “measure“ the internal thread later. Had to grind a 55* tool on the T&CG. I made it out of HSS and used it for both the external thread here and later in a threading bar for the internal thread. The thread was made as close as I could to the standard as published in technical manuals. I used the three wire method to measure it accurately.
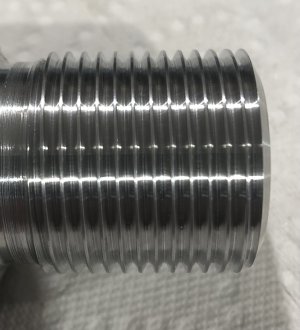
Next I got the PVC stock set up in the lathe and roughed out the adapter at the end of the slug. The necked down (cylindrical) part is to dimension (it includes about 3/4” extra length at the base for work holding later during the internal machining) and the lager section needs to be taper turned to accept the MPT.
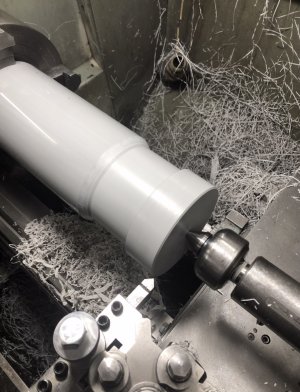
PVC produces strings, no matter what you do. The problem arises when the stuff can’t clear the cutting tool and starts to “weld” itself back into the part because it heats up very fast to its plastic temperature. This was especially tricky when I bored the recess in the next op.
Using the taper attachment to thread 4” MPT.
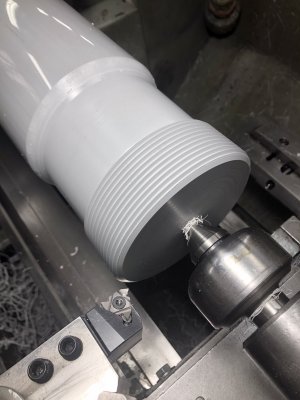
This completed the external work other than finish to length.
Now I cut the part off the slug on the bandsaw and mounted it back in the 4J by holding onto the ~ 3/4” machining allowance. This reduced the stick out to an acceptable level. Bored the recess and then worked on the internal G1 BSP thread at the base of the adapter.
The gage made previously was used to check the dimension of this thread. The threading tool seen in the boring bar is the same as was used to make the gage.
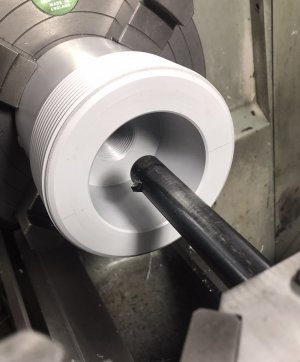
Once the internal work was complete, the part was flipped 180* and held internally in the 4J. The machining allowance was now parted off and the bottom faced to bring the part to final length.
There are 4 holes in the face of the part for a pin spanner to tighten it into the tank’s opening. These were drilled on the mill.
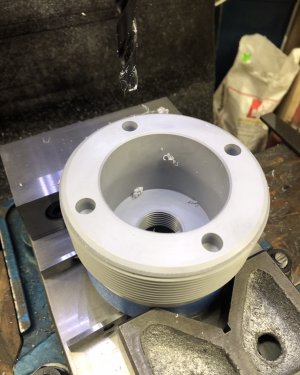
Couple more pictures of the finished part.
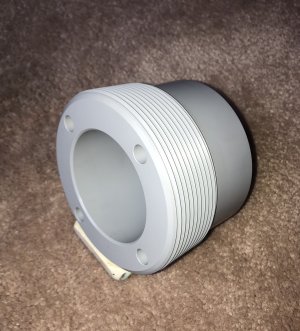
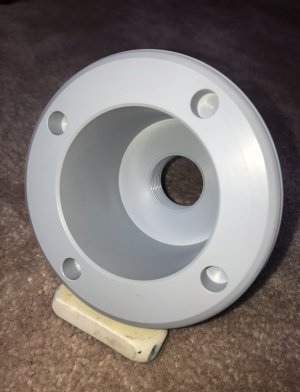
So what did I learn?
PVC turns very well. Strings need to be controlled otherwise they weld themselves back where you don’t want them and create chatter. Carbide tooling suitable for aluminum or stainless steel works well on PVC. So does sharp HSS. The biggest DoC I tried was 5mm; it worked, but the strings get very soft and can start to cause problems. So I reduced the max to 3mm. The maximum rpm was 770. The strings get too soft above that. No coolant or cutting fluid was used.