Completely off any topic, but I'm in an unusually bad insomnia cycle for the past month....so Google is my friend.
After I got my new solid rivet gun a while back it's been bugging me how ship builders solved the issue of making riveted plates watertight. I have seen old wooden boats caulked with oakum and tar etc., but always wondered how steel hulls were done. I also knew wooden boats made with certain types of wood were sunk first to allow the wood to expand and help seal the joints, but what about steel? I created a post a while back about my gun and even showed a vid of old fashioned hot rivets being set (very cool), so maybe that's how I got down this path of wondering.
Anyways, I finally did some research and was fascinated to discover that the plates were indeed "caulked," but not in the way we use the term today. The plates are actually deformed (caulked) with impact hammers to plasticize the metal, creating a downward facing ridge that presses on the bottom plate to create the watertight seal. It is a two stage process to make the joint watertight, but in fact uses no substrate to achieve the result. Between the contraction of the hot rivet and the proper seam done by a skilled tradesman, the plates are watertight. A great illustration is here:
The full explanation (with photo of the cross section) can be found here: http://johnoxley.org.au/restoration/how-is-it-done/caulking-plate-edges/ The distance from the edge of the plate to the rivet (not shown here) is actually critical. When just right the ridge ever so slightly lifts the plate against the rivet, resulting in a spring-like seal against the bottom plate. Genius!
While welding has been around since the 19th century, it was weaker that rivets back then (plus we knew less about materials science). Rivets also had an added benefit of stopping stress cracks from travelling the length of the plate—something problematic in cold Atlantic waters with big waves. Some Liberty ships literally snapped in two even before leaving the dock. There's a pic of one here: https://metallurgyandmaterials.wordpress.com/2015/12/25/liberty-ship-failures/
Now that I have this "caulking" solution tucked in my brain, perhaps I can rest tonight.
I hope I don't start thinking about special seals used around the driveshaft of a submarine's propeller to keep the water out under deep sea pressures.
Darn.
Back to Google again 🙁
After I got my new solid rivet gun a while back it's been bugging me how ship builders solved the issue of making riveted plates watertight. I have seen old wooden boats caulked with oakum and tar etc., but always wondered how steel hulls were done. I also knew wooden boats made with certain types of wood were sunk first to allow the wood to expand and help seal the joints, but what about steel? I created a post a while back about my gun and even showed a vid of old fashioned hot rivets being set (very cool), so maybe that's how I got down this path of wondering.
Anyways, I finally did some research and was fascinated to discover that the plates were indeed "caulked," but not in the way we use the term today. The plates are actually deformed (caulked) with impact hammers to plasticize the metal, creating a downward facing ridge that presses on the bottom plate to create the watertight seal. It is a two stage process to make the joint watertight, but in fact uses no substrate to achieve the result. Between the contraction of the hot rivet and the proper seam done by a skilled tradesman, the plates are watertight. A great illustration is here:
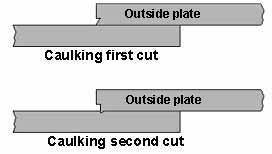
The full explanation (with photo of the cross section) can be found here: http://johnoxley.org.au/restoration/how-is-it-done/caulking-plate-edges/ The distance from the edge of the plate to the rivet (not shown here) is actually critical. When just right the ridge ever so slightly lifts the plate against the rivet, resulting in a spring-like seal against the bottom plate. Genius!
While welding has been around since the 19th century, it was weaker that rivets back then (plus we knew less about materials science). Rivets also had an added benefit of stopping stress cracks from travelling the length of the plate—something problematic in cold Atlantic waters with big waves. Some Liberty ships literally snapped in two even before leaving the dock. There's a pic of one here: https://metallurgyandmaterials.wordpress.com/2015/12/25/liberty-ship-failures/
Now that I have this "caulking" solution tucked in my brain, perhaps I can rest tonight.
I hope I don't start thinking about special seals used around the driveshaft of a submarine's propeller to keep the water out under deep sea pressures.
Darn.
Back to Google again 🙁
Last edited: