Hey everyone,
This is my first post i found this forum trying to track down somone for a small job, I need a template made for cutting slots in Kydex.
The material is not super imortant but it needs to be at least 1/8" thick preferably stainless. Ill try to include a picture to give an idea of what i need please feel free to ask anything you need to know to properly quote this.
If the picture i post is too hard to figure out or just too busy i can send anyone the cad file.
Thanks in advance for any help with this.
This is my first post i found this forum trying to track down somone for a small job, I need a template made for cutting slots in Kydex.
The material is not super imortant but it needs to be at least 1/8" thick preferably stainless. Ill try to include a picture to give an idea of what i need please feel free to ask anything you need to know to properly quote this.
If the picture i post is too hard to figure out or just too busy i can send anyone the cad file.
Thanks in advance for any help with this.
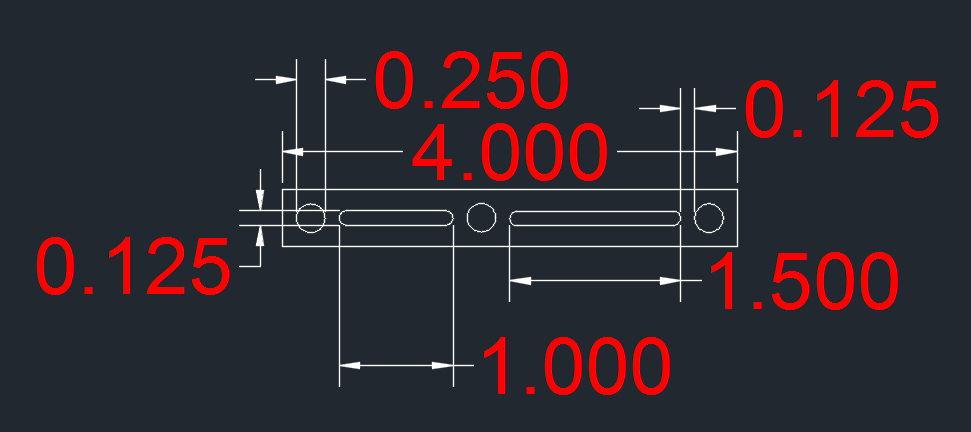