Ive been using these cardboard boxes for years in my truck to organize anchors, they are convenient, the anchors come in them, and they are all the same size. But, they are cardboard, so they fall apart, ive thought about buying little plastic bins to replace them with...but i know they will fall apart....probably faster. Making these little metal boxes has been on the back of my mind for a while, and with no work today i figured what the heck, might as well...i have material, and it will give me cnc practice, sheet metal practice...and why not add in solid rivet practice (the only solid rivets on the zenair are in the wing spars, and i didnt do those)
By the last one i had it down to 25 minutes from putting the piece on the cnc to driving the last rivet, i probably wouldn't make it as a sheet metal guy, and my rivets still need some work
its all 18g 5052 with 1/8 solid an rivets
The trial box...
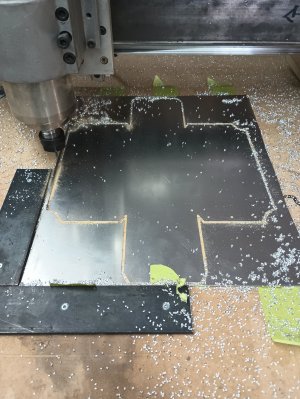
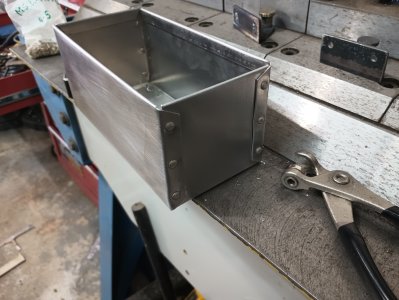
ok that worked out...lets start the mass production
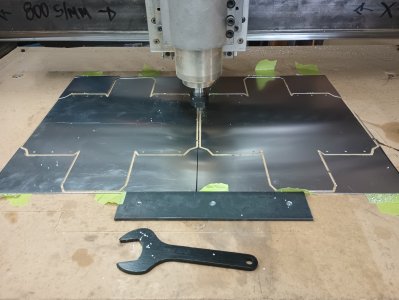
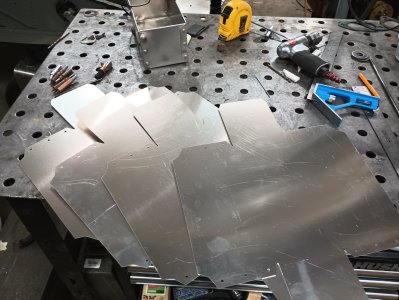
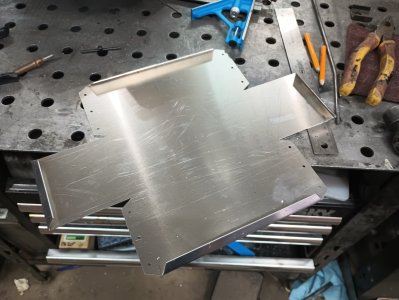
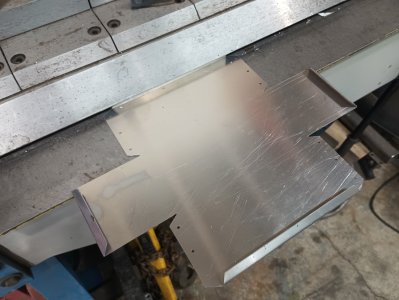
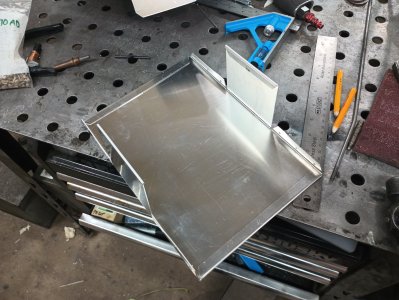
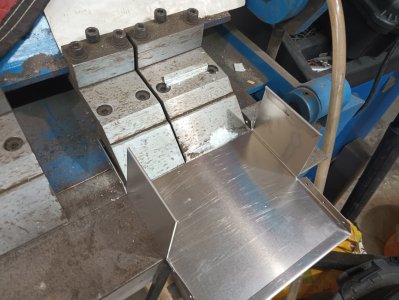
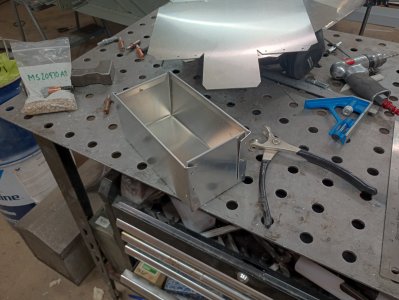
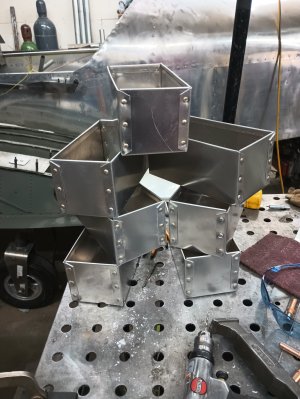
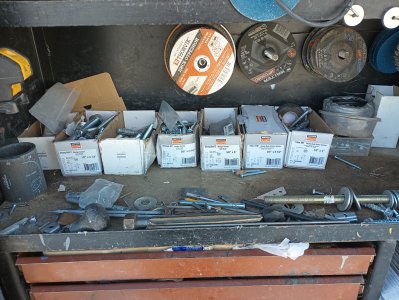
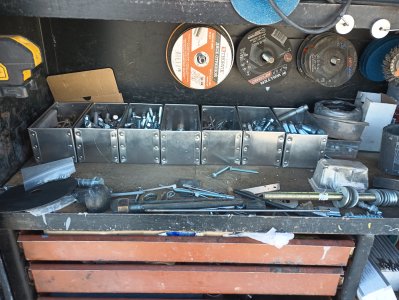
By the last one i had it down to 25 minutes from putting the piece on the cnc to driving the last rivet, i probably wouldn't make it as a sheet metal guy, and my rivets still need some work
its all 18g 5052 with 1/8 solid an rivets
The trial box...
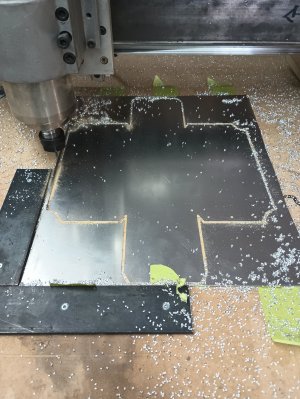
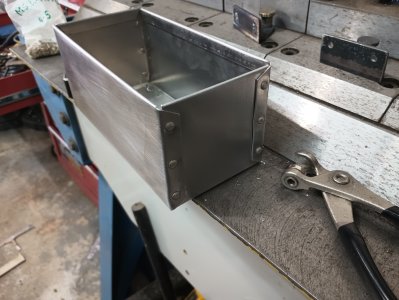
ok that worked out...lets start the mass production
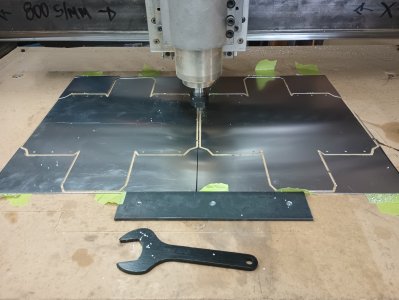
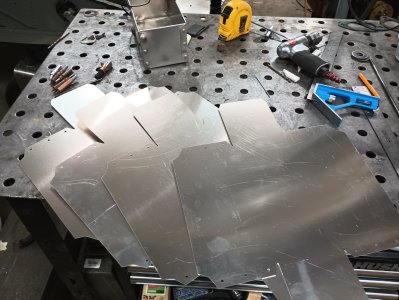
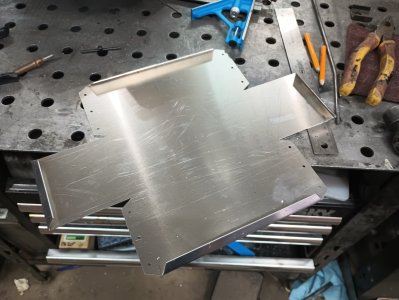
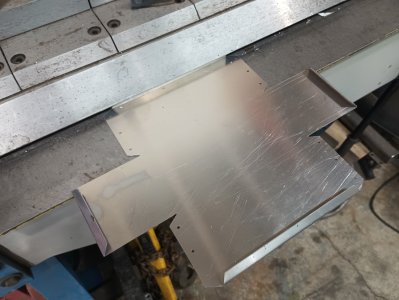
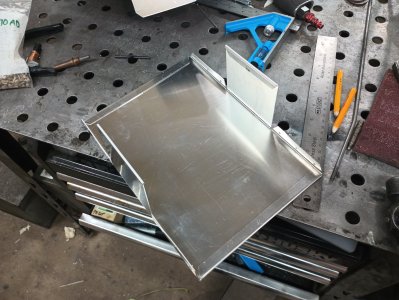
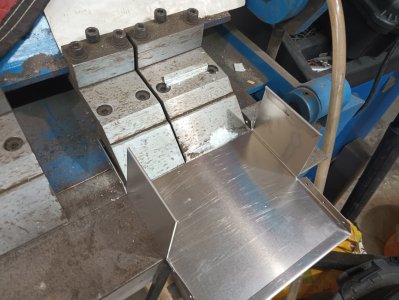
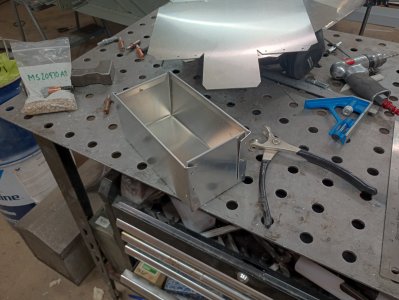
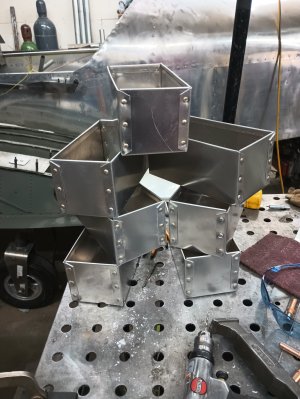
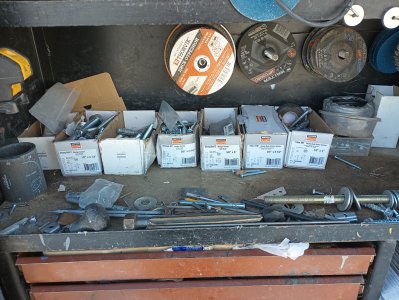
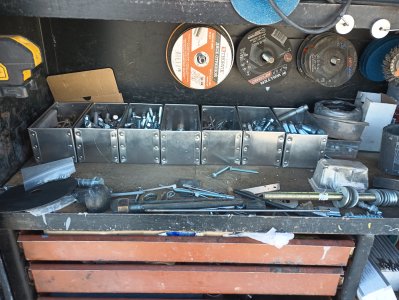