Dieselbenz1
Member
Hi again I need some ideas on how to repair this head I just picked up. As you can see in the picture someone tried to drill out a stainless steel pin used to hold the chain rail guide. The result is part of the shoulder used as structure has been removed and a new hole has been made in the case. I have more pics but its not letting me post any more. Anyways I need ideas and likely talent to repair this somehow.
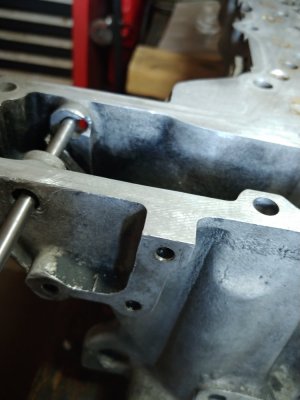
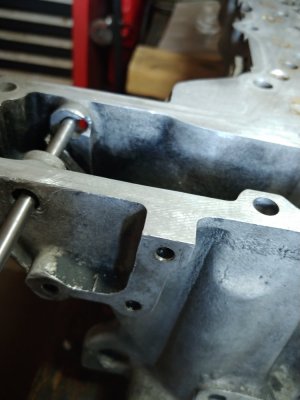