terry_g
Ultra Member
Over twenty five years ago I bought A Southbend 10K lathe. One of the sets of jaws was missing for the 3 jaw chuck so I bought a new chuck for it.
I paid almost as much for the chuck as I paid for the lathe. I had a few options but I bought a quality chuck made in Poland.
I remember cringing at the price when I bought it.
About twelve years ago I sold the Southbend and bought a Chinese 12 x 36 lathe. I swapped chucks and gave the new
owner of the Southbend the chuck that came with the Chinese lathe which was also a decent quality chuck.
A while back I was making some heavy duty washers for a gear puller. I sawed four 3/8" pieces off a chunk of 1 1/4"
round stock and chucked all four of them in the lathe to drill them. When the centre drill hit the first washer it spun in the chuck.
I took some pieces of scrap aluminium from an old cleaning rod and made spacers so I could tighten the chuck jaws with them still open.
I attached a Dremel die grinder to the tool post using a 3/8 key and rubber bands made from an old motorcycle tire tube.
I fed the grinding wheel back and fourth on the chuck jaws grinding very lightly for the better part of half an hour.
I put some Play Dough at the back of the jaws to keep the grinder grit out of the scroll plate.
Once I was done I took the jaws out and cleaned the chuck and jaws well.
I paid almost as much for the chuck as I paid for the lathe. I had a few options but I bought a quality chuck made in Poland.
I remember cringing at the price when I bought it.
About twelve years ago I sold the Southbend and bought a Chinese 12 x 36 lathe. I swapped chucks and gave the new
owner of the Southbend the chuck that came with the Chinese lathe which was also a decent quality chuck.
A while back I was making some heavy duty washers for a gear puller. I sawed four 3/8" pieces off a chunk of 1 1/4"
round stock and chucked all four of them in the lathe to drill them. When the centre drill hit the first washer it spun in the chuck.
I took some pieces of scrap aluminium from an old cleaning rod and made spacers so I could tighten the chuck jaws with them still open.
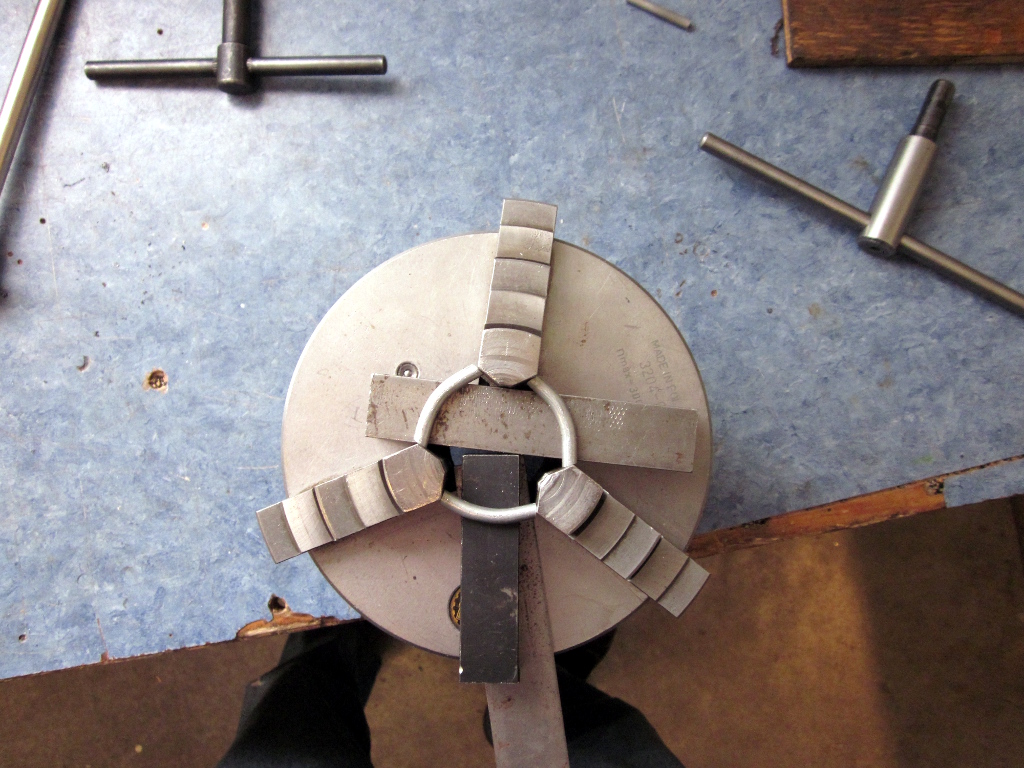
I attached a Dremel die grinder to the tool post using a 3/8 key and rubber bands made from an old motorcycle tire tube.
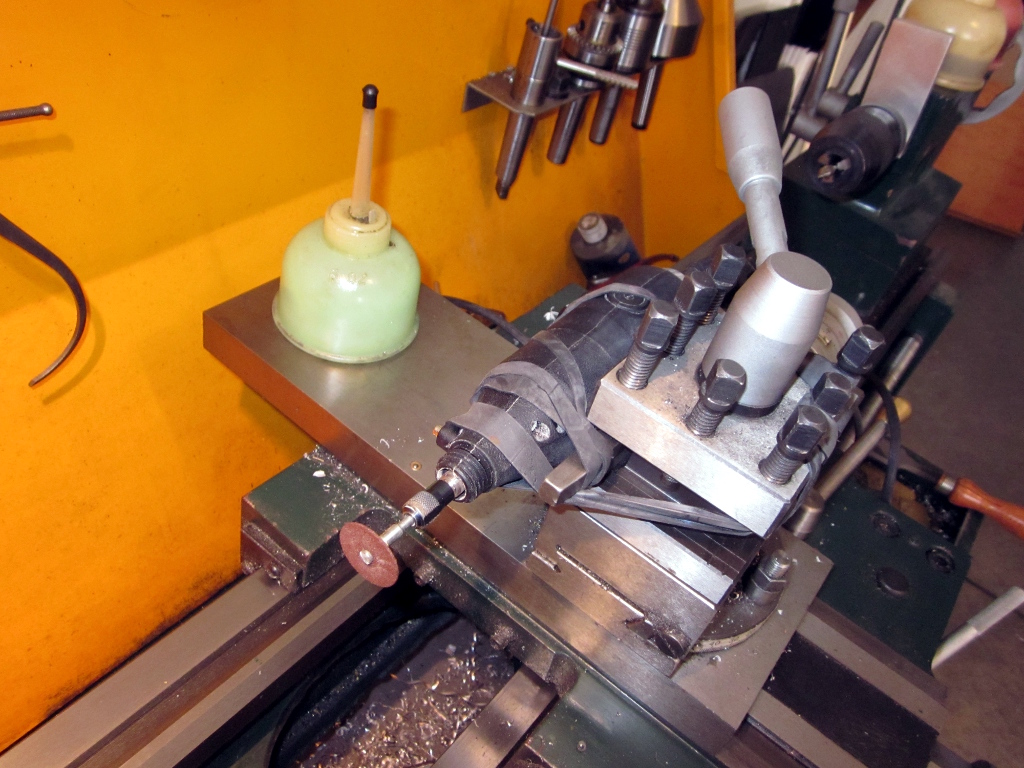
I fed the grinding wheel back and fourth on the chuck jaws grinding very lightly for the better part of half an hour.
I put some Play Dough at the back of the jaws to keep the grinder grit out of the scroll plate.
Once I was done I took the jaws out and cleaned the chuck and jaws well.

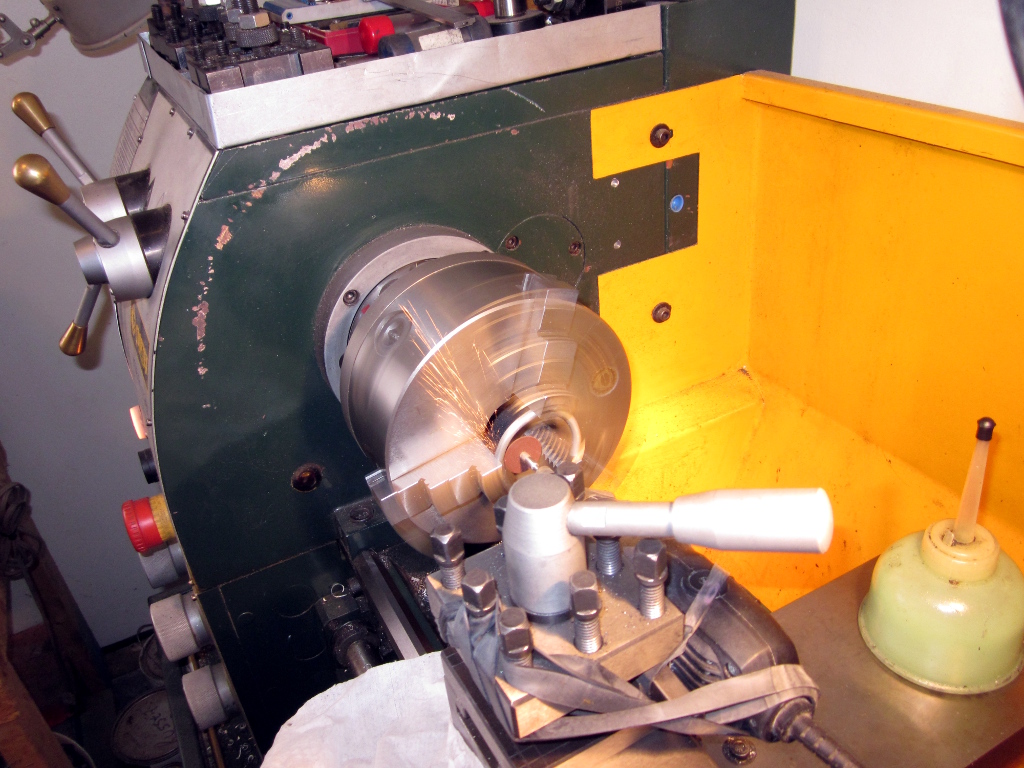