I managed to source what I thought were the right size drive hubs for a project. The bore was supposed to be 17mm to accommodate the motor shafts which are just under 17mm. Sadly, when they arrived from the USA the internal bores are slightly too small at 16.59 and 16.47mm respectively. The shafts are both 16.97mm. In other words, even if they were intended to be an interference fit (which they are not), they would be too tight. In fact I can't even get the shaft on.
I'm fighting with the USA supplier but thought I'd ask for a backup plan in case they don't come through. Because it is a keyed shaft I'd need a spiral fluted chucking reamer to work the keyway. The hub depth is 2.3". I don't have any spirals, or any straight fluted 17mm reamers (which wouldn't work). I could take it to a shop, which I may do. I'm still looking for a affordable spiral online.
If the company does send me new hubs, the duty will be another 48 bucks. So I'm looking for cheaper solutions. Are there any lathe tricks for re-boring a keyed hole? Can it be done? The material is A36 I'm pretty sure.
What about a 17mm drill bit? Would the 118 degree point be sufficient to rebore these? That seems like the cheapest solution if it would work.
Any ideas??
I'm fighting with the USA supplier but thought I'd ask for a backup plan in case they don't come through. Because it is a keyed shaft I'd need a spiral fluted chucking reamer to work the keyway. The hub depth is 2.3". I don't have any spirals, or any straight fluted 17mm reamers (which wouldn't work). I could take it to a shop, which I may do. I'm still looking for a affordable spiral online.
If the company does send me new hubs, the duty will be another 48 bucks. So I'm looking for cheaper solutions. Are there any lathe tricks for re-boring a keyed hole? Can it be done? The material is A36 I'm pretty sure.
What about a 17mm drill bit? Would the 118 degree point be sufficient to rebore these? That seems like the cheapest solution if it would work.
Any ideas??
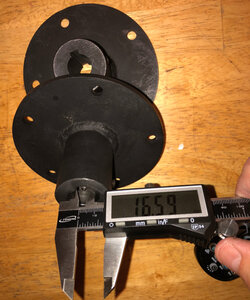