Tobho Mott
Well-Known Member
Several months ago for reasons I still can't quite comprehend, a fellow from our near Kingston was willing to take these off my hands (the Salamander in the middle is top shelf for a clay graphite crucible and has lots of life left in it but the other two A6's are DOA and near retirement)
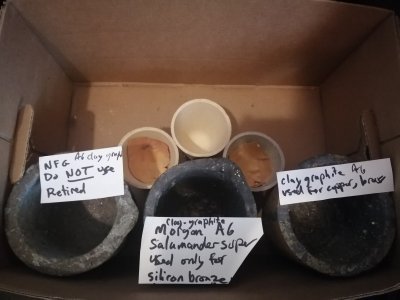
in trade for these:
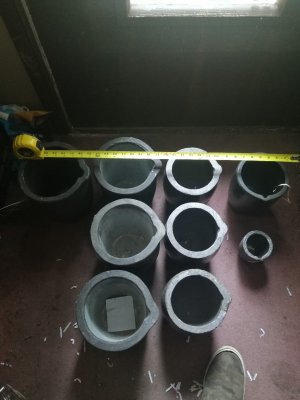
All stored dry and never used. Near as I can tell from L to R that's an A20, three A16's, 3 B12's (so far all silicon carbide, from Vesuvius), and 2 Morgan Salamander Super clay graphites, an A2 and an A12.
I only have liftout tongs and pouring shanks for my A6's and my existing B12 silicon carbide crucible, which is a decent size and shape match for the new Vesuvius B12's (although I do not like the shank I made for the B12 back in 2015). And some.very large ones, but not for any 16's or 20's.
Those silicon carbide crucibles are expensive, but they can last a really long time, my 10yo one is still in great shape if you ignore the chips.resulting from my clumsiness. I normally buy clay graphite crucibles because they're cheaper, and the good ones also last a long time.
Anyhow, so I need tongs and pouring shanks for the A12 and eventually for the A16's and the A20. Since the A12 is iron rated and getting into cast iron is my big spring project this year, I decided to start with that.
I cut off the tapered sides of a piece of C-channel I had lying around and with some help from a friend got them rolled into almost sort of circles and welded into 2 rings I could bring back home to work on some more. One for the A12 and hopefully also the B12's, and one for the A20 and hopefully also the A16's which aren't as narrow at the bottom as the 20. Crucibles are weird.
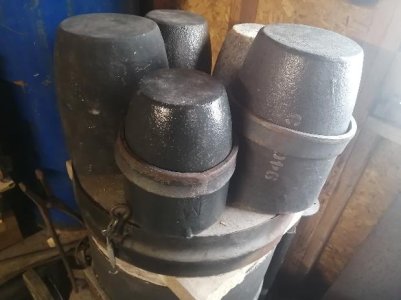
To get them to fit this well I got out my anvil shaped objects and propped up the lid of my waste oil furnace on some firebricks to use it as an improvised propane forge, making a space where the rings could sit on the edge of the furnace sort of half inside it to heat up so I could refine the roundness and put some added taper on the sides.
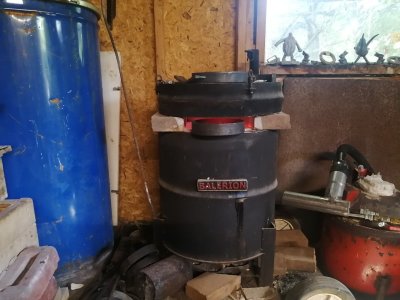
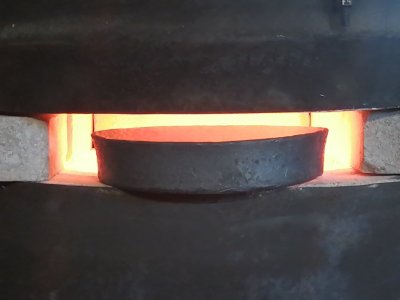
I'm no blacksmith, but it worked out eventually.
I'm just as bad of a welder, but getting the handle attached worked out ok too. I swung it overhead to smash the ring into some heavy beams a couple times and it didn't break off, so I guess I'm good to go.
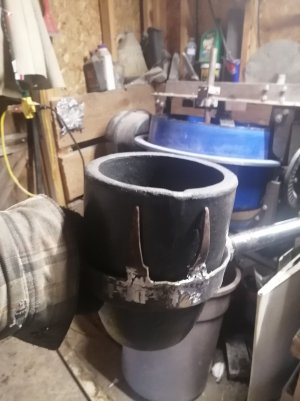
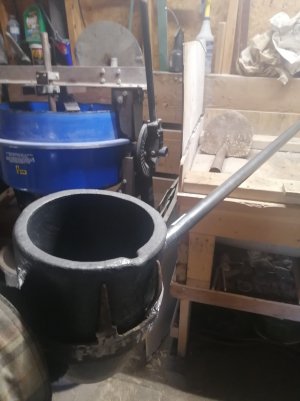
It sits a little low on the B12's, but after welding a couple of rake tines to the top of the ring they'll stay put in it (the new ones and my old one), huzzah!
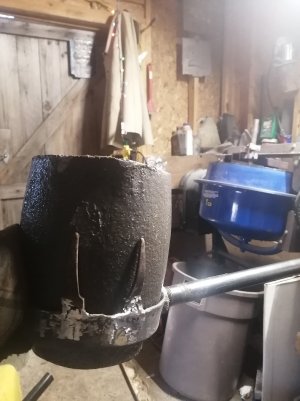
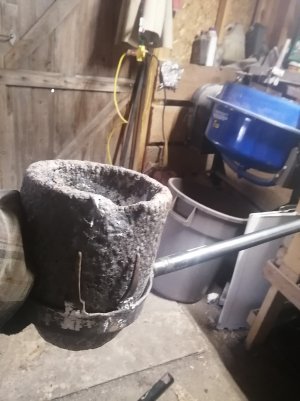
I really didn't like the old B12 pouring shank so that's a bonus. Its ring was so thick it got in the way of getting the crucible spout down as close (in)to the pouring basin of my sprues as I prefer to.
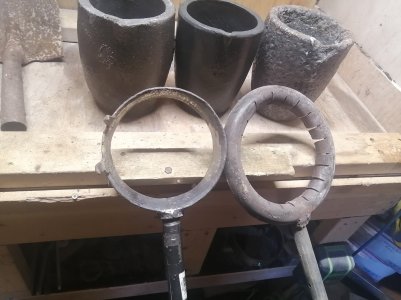
The spade blade on the left above will become a heat shield for my right hand. Still need a tilting handle for my left at the cold end as well.
The A12 would just fall right through the B12 pouring shank, though these A and Bilge shaped #12 crucibles all have the same nominal capacity (12 pounds of aluminum brim full, which is really too full if you like your feet). Happy that the new and old B12's are similar enough to use the same tools as each other, but being able to share with the A12 is a really nice bonus..
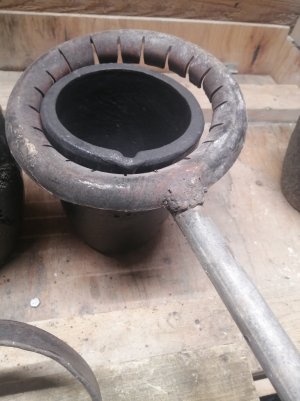
Next up, the liftout tongs...
I've used an app to reduce the size of these pics, but if this was still too much someone please let me know.
Jeff
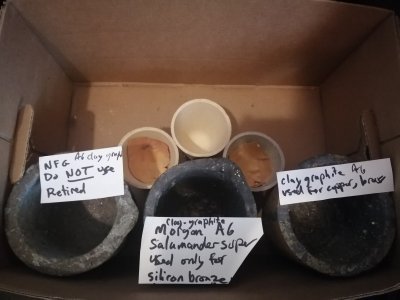
in trade for these:
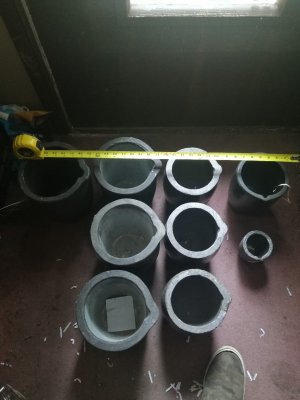
All stored dry and never used. Near as I can tell from L to R that's an A20, three A16's, 3 B12's (so far all silicon carbide, from Vesuvius), and 2 Morgan Salamander Super clay graphites, an A2 and an A12.
I only have liftout tongs and pouring shanks for my A6's and my existing B12 silicon carbide crucible, which is a decent size and shape match for the new Vesuvius B12's (although I do not like the shank I made for the B12 back in 2015). And some.very large ones, but not for any 16's or 20's.
Those silicon carbide crucibles are expensive, but they can last a really long time, my 10yo one is still in great shape if you ignore the chips.resulting from my clumsiness. I normally buy clay graphite crucibles because they're cheaper, and the good ones also last a long time.
Anyhow, so I need tongs and pouring shanks for the A12 and eventually for the A16's and the A20. Since the A12 is iron rated and getting into cast iron is my big spring project this year, I decided to start with that.
I cut off the tapered sides of a piece of C-channel I had lying around and with some help from a friend got them rolled into almost sort of circles and welded into 2 rings I could bring back home to work on some more. One for the A12 and hopefully also the B12's, and one for the A20 and hopefully also the A16's which aren't as narrow at the bottom as the 20. Crucibles are weird.
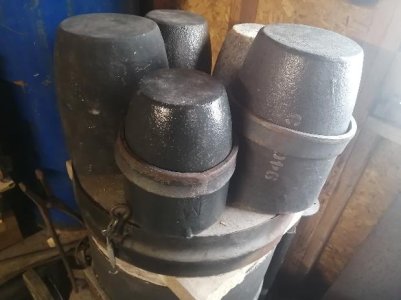
To get them to fit this well I got out my anvil shaped objects and propped up the lid of my waste oil furnace on some firebricks to use it as an improvised propane forge, making a space where the rings could sit on the edge of the furnace sort of half inside it to heat up so I could refine the roundness and put some added taper on the sides.
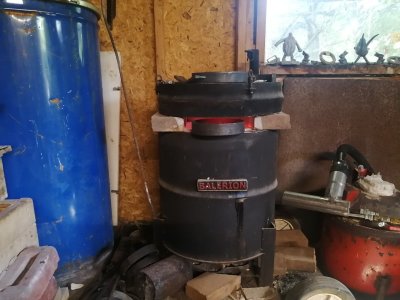
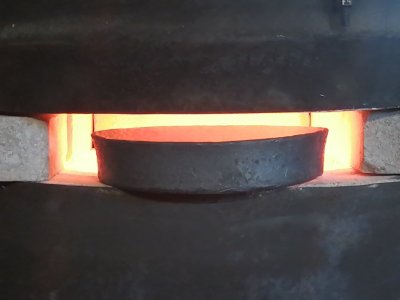
I'm no blacksmith, but it worked out eventually.
I'm just as bad of a welder, but getting the handle attached worked out ok too. I swung it overhead to smash the ring into some heavy beams a couple times and it didn't break off, so I guess I'm good to go.
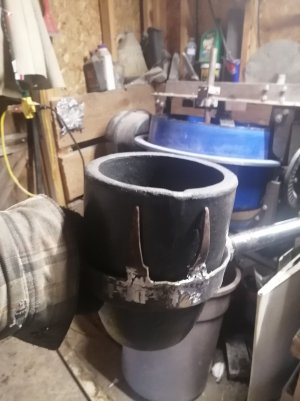
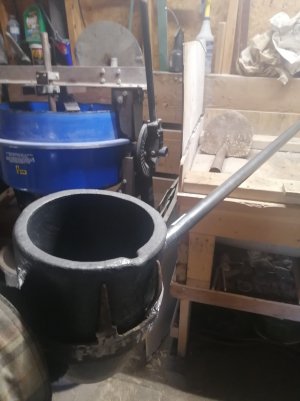
It sits a little low on the B12's, but after welding a couple of rake tines to the top of the ring they'll stay put in it (the new ones and my old one), huzzah!
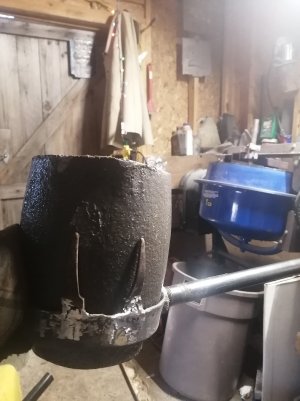
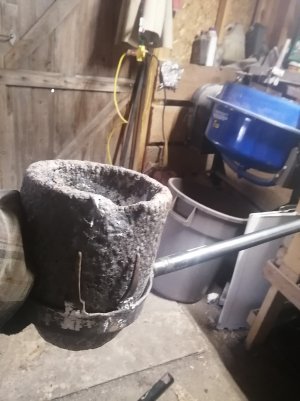
I really didn't like the old B12 pouring shank so that's a bonus. Its ring was so thick it got in the way of getting the crucible spout down as close (in)to the pouring basin of my sprues as I prefer to.
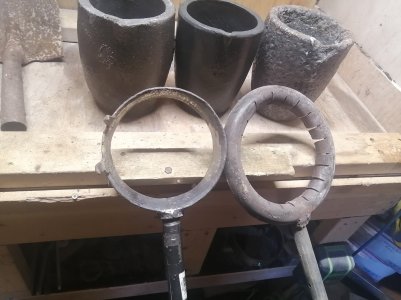
The spade blade on the left above will become a heat shield for my right hand. Still need a tilting handle for my left at the cold end as well.
The A12 would just fall right through the B12 pouring shank, though these A and Bilge shaped #12 crucibles all have the same nominal capacity (12 pounds of aluminum brim full, which is really too full if you like your feet). Happy that the new and old B12's are similar enough to use the same tools as each other, but being able to share with the A12 is a really nice bonus..
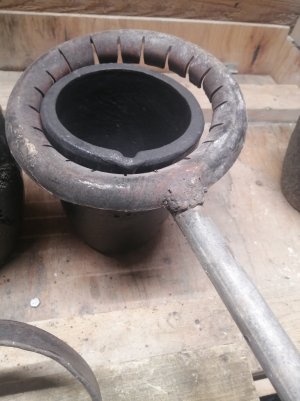
Next up, the liftout tongs...
I've used an app to reduce the size of these pics, but if this was still too much someone please let me know.
Jeff