ChazzC
Ultra Member
I submitted my questions to Wera last night:
Subject
Comment
Also asked Bosch if there was a chart of the torque vs. Clutch Setting on the PS21 (and if not, was there an estimated torque for the lowest setting).
Amazon (US) has the Wera 900 kit for US$88:
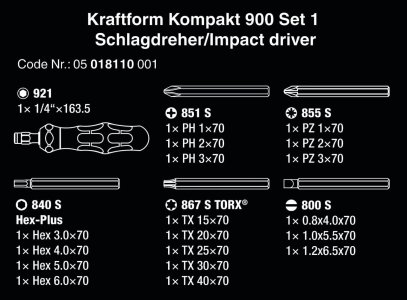
Just US$18 more than just the screwdriver, so US$1 per bit (and a free case).
I forgot to ask Wera about the warranty & broken bits (will do so in my reply to their response when I get it): does anyone know if they replace broken bits?
Subject
921 KRAFTFORM PLUS IMPACT SCREWDRIVER - DETAILS |
Comment
Hi, I have several questions about the 921 Screwdriver: • The description states “The pound-thru blade ensures complete power transmission (zero loss).” How much of the hammer blow is transferred into rotary motion? I am concerned that when the screwdriver is “On” that there will be significant force applied down into the screw. • The impact is noted as producing “a loosening moment of up to 25 Nm.” What is the minimum torque that can be produced? I understand that lighter blows on the handle of the screwdriver will produce lower torque, but I assume that there is a lower limit due to friction within the mechanism. • What is the smallest screw that you would recommend that the 921 be used on? Thank you for your assistance, Charlie |
Also asked Bosch if there was a chart of the torque vs. Clutch Setting on the PS21 (and if not, was there an estimated torque for the lowest setting).
Amazon (US) has the Wera 900 kit for US$88:
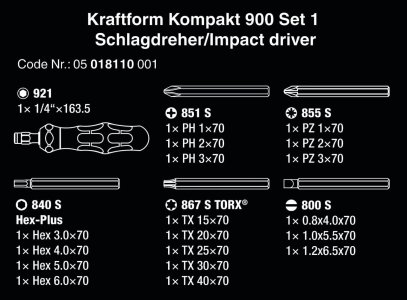
Just US$18 more than just the screwdriver, so US$1 per bit (and a free case).
I forgot to ask Wera about the warranty & broken bits (will do so in my reply to their response when I get it): does anyone know if they replace broken bits?