Phaneron
Scott
I have a brand new, never used 4 jaw chuck with accessories. It came with an older lathe I now have since sold. I plan to buy a direct mount D1-3 4 jaw for my current lathe instead of using this plain back with an adapter. Asking $120, will ship at buyers expense. Located in SE Calgary, Alberta.
Link to product which was bought from KBC Tools; https://www.kbctools.ca/itemdetail/6-318-004
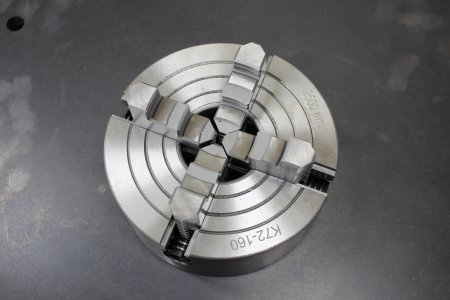
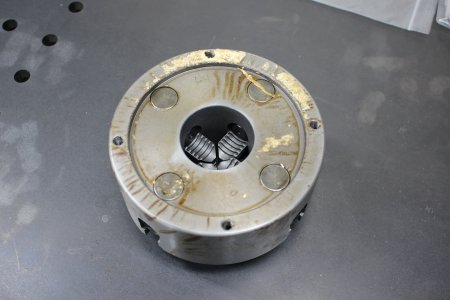
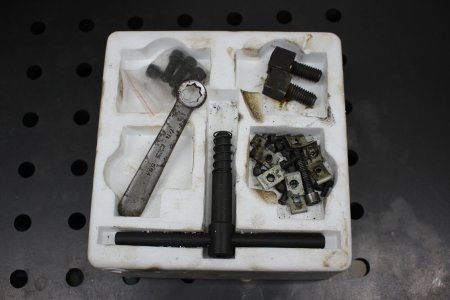
Link to product which was bought from KBC Tools; https://www.kbctools.ca/itemdetail/6-318-004
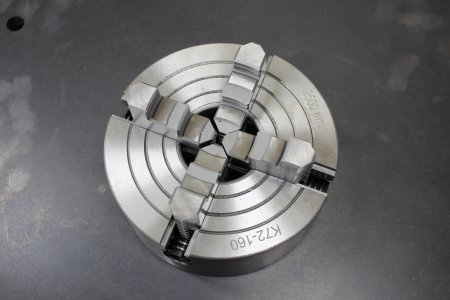
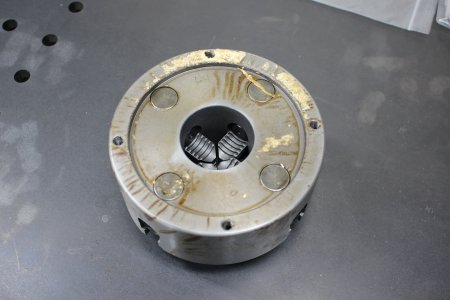
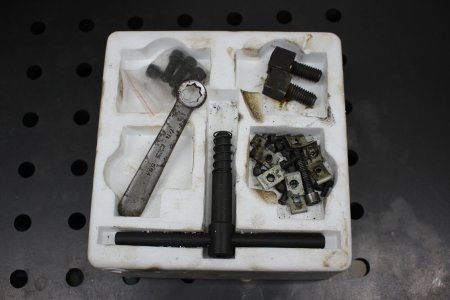