KeeponDragon
no problems... just challenges
Oh look...apprentice marks...
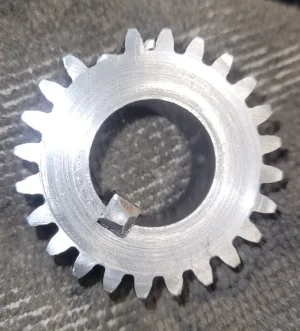
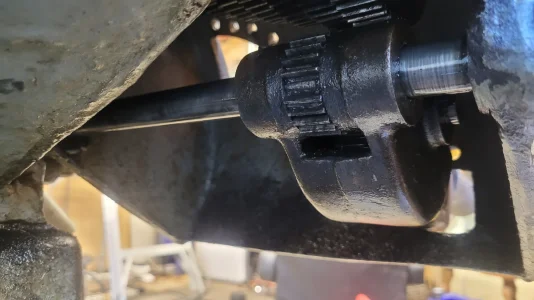
That gear came out of the speed change gizmo...the pin in the back for the gear pack engagement...not even locked in to place...
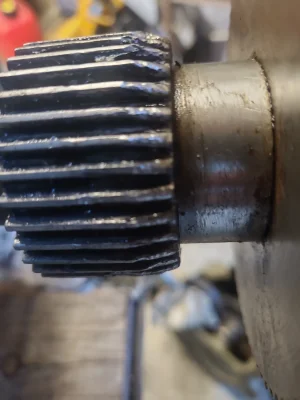
This tumbler looks like it was half engaged for a while
There's 2 of them on this unit...both in similar condition
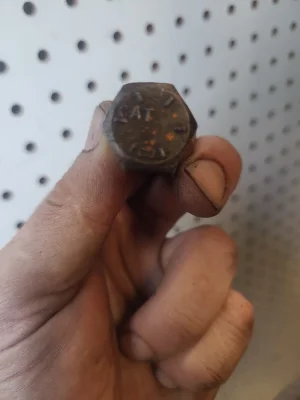
Equipment mechanic tell-tale sign...
I was successful with getting it wired up and running...VFD works good
The new cone drive belt from the local distributor works like a charm
But upon light up, the gear train was making some pretty hellacious noise...
So I started looking deeper...
Lots of loose fasteners...some chipped teeth...
Not surprised...it IS 100 afterall...
If anyone has gears in a box collecting dust...lemme know lol
The gear pack for the lead screw has 3 damaged gears in it as well...
So I guess it makes sense why the previous owner made the comment about scrapping it....he just didn't want to put in the effort to repair it...
It can still turn parts though
And I'm ok with that...
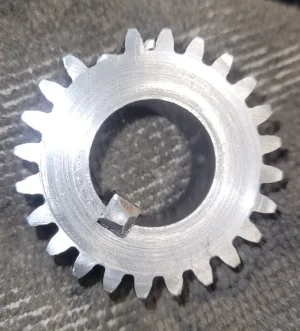
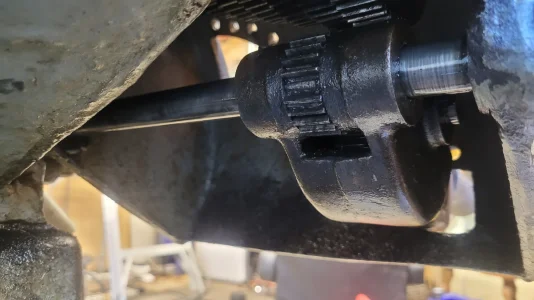
That gear came out of the speed change gizmo...the pin in the back for the gear pack engagement...not even locked in to place...
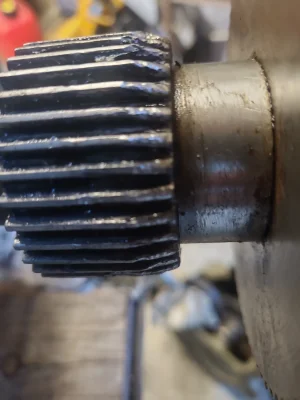
This tumbler looks like it was half engaged for a while
There's 2 of them on this unit...both in similar condition
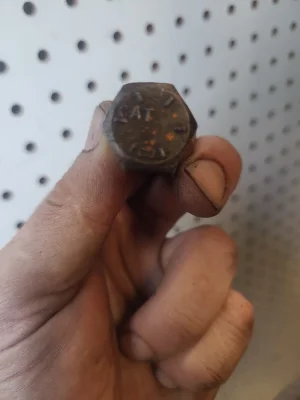
Equipment mechanic tell-tale sign...
I was successful with getting it wired up and running...VFD works good
The new cone drive belt from the local distributor works like a charm
But upon light up, the gear train was making some pretty hellacious noise...
So I started looking deeper...
Lots of loose fasteners...some chipped teeth...
Not surprised...it IS 100 afterall...
If anyone has gears in a box collecting dust...lemme know lol
The gear pack for the lead screw has 3 damaged gears in it as well...
So I guess it makes sense why the previous owner made the comment about scrapping it....he just didn't want to put in the effort to repair it...
It can still turn parts though
And I'm ok with that...