Tmate
Well-Known Member
Here are some mods I made to my 20 ton Harbor Freight press:
Air/hydraulic jack, table winch, guide rollers, casters, pinned table plates, release knob, grade 8 frame bolts, finger brake, support pin shaft collars.
Also, I have found it obnoxious to give up my ability to use my press when it is occupied by my Swag finger brake. As useful as the brake is, it is tiresome to have to uninstall it every time the press is needed as a press.
I'm currently fixing this problem. If you have a winch installed to raise and lower the deck, as I do, my fix is to lower the existing deck (table) way down, and fabricate a second deck from a length of channel. It can be quickly inserted above the brake in the frame and used for pressing. The second deck can be made as sturdy as necessary for the pressing you intend to do. Use a wooden block to raise the pressing surface as needed. I'm using 4" x 7.25 channel, which is in the process of being delivered. See second image.
Air/hydraulic jack, table winch, guide rollers, casters, pinned table plates, release knob, grade 8 frame bolts, finger brake, support pin shaft collars.
Also, I have found it obnoxious to give up my ability to use my press when it is occupied by my Swag finger brake. As useful as the brake is, it is tiresome to have to uninstall it every time the press is needed as a press.
I'm currently fixing this problem. If you have a winch installed to raise and lower the deck, as I do, my fix is to lower the existing deck (table) way down, and fabricate a second deck from a length of channel. It can be quickly inserted above the brake in the frame and used for pressing. The second deck can be made as sturdy as necessary for the pressing you intend to do. Use a wooden block to raise the pressing surface as needed. I'm using 4" x 7.25 channel, which is in the process of being delivered. See second image.
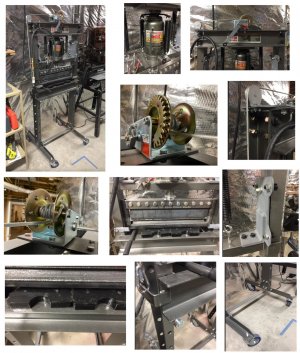
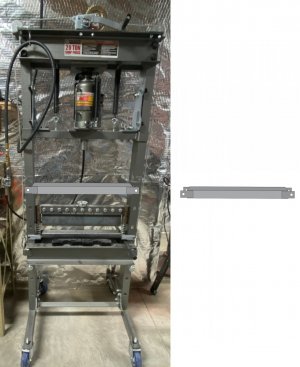