TorontoBuilder
Sapientia et Doctrina Stabilitas
So I finally found a cheap viable option to add tooling to my meyrat and luisoni tousdiamants mill/faceting machine
I'm not paying 1200 euros for a set of w12 collets. I'm going to buy this blank W12 arbour and machine it into an ER16 collet chuck. No need to machine the buttress threads at all. 23mm x 40mm machinable round section... ER16 requires M19 x 1.0 for the nut. 8 degree taper angle and a 22mm bore, Easy stuff.
Cheap enough to buy 2 or 3 of these blank arbours and then make a slitting saw arbour too
I'm not paying 1200 euros for a set of w12 collets. I'm going to buy this blank W12 arbour and machine it into an ER16 collet chuck. No need to machine the buttress threads at all. 23mm x 40mm machinable round section... ER16 requires M19 x 1.0 for the nut. 8 degree taper angle and a 22mm bore, Easy stuff.
Cheap enough to buy 2 or 3 of these blank arbours and then make a slitting saw arbour too
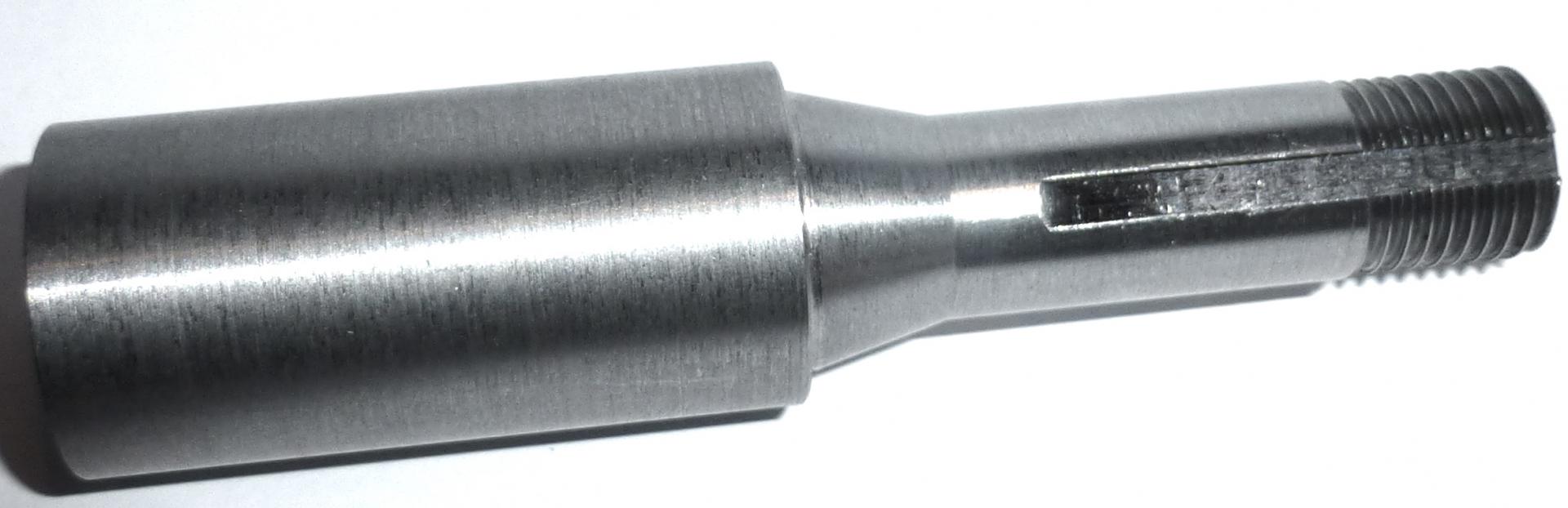