Earl Wong
Active Member
I've been in search for an atlas Shaper for awhile to complete my collection of Atlas machines I've already rebuilt (can be found on my other posts) and finally came across this one from Ontario. It's an early version of the 7B Shaper that most people have, almost a prototype as I keep running across several differences between this version (according to Clausing built in 1937 according to serial number) and the latest versions.
I have completely disassembled it already, stripped and cleaned to assess what parts need to be made and repaired. There is surface scraping planned, parts built, and rebuilt. Stay tuned for the build progress and I welcome any comments that may help me in the build, especially if you have experience with these shapers.
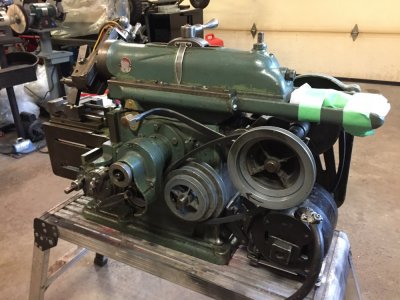
I have completely disassembled it already, stripped and cleaned to assess what parts need to be made and repaired. There is surface scraping planned, parts built, and rebuilt. Stay tuned for the build progress and I welcome any comments that may help me in the build, especially if you have experience with these shapers.
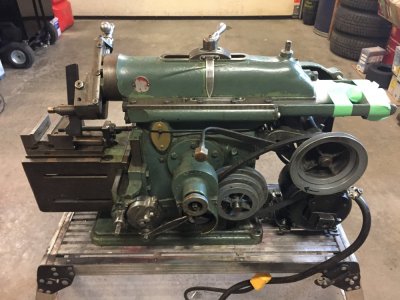
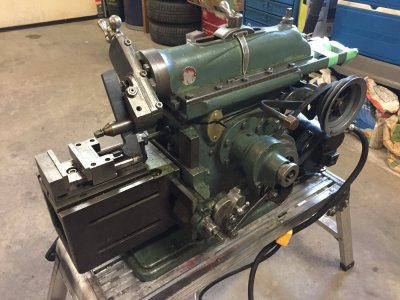
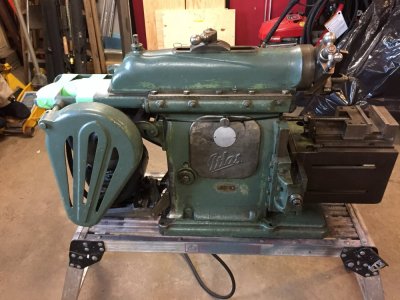
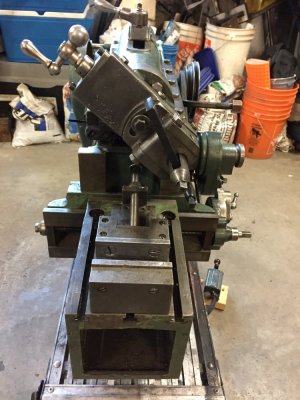
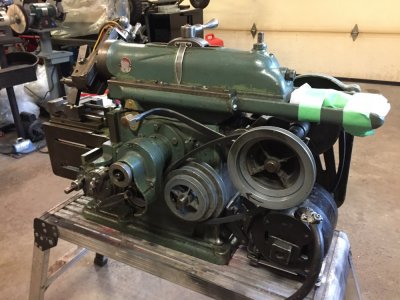