@Susquatch explains his quick and dirty yet effective screw shortening technique.
canadianhobbymetalworkers.com
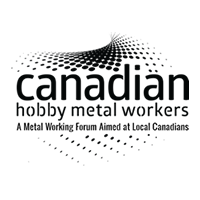
Tool - Threaded screw cutter
I have an older set of wire strippers that I picked up of the Snap-On truck back in the 70's. There not great for wire stripping however the threaded screw cutter is really handy. However fairly limited selection for screws, no M3 which is what I need right now. Suggestions for a similar...
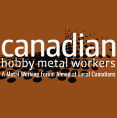