Chicken lights
Forum Pony Express Driver
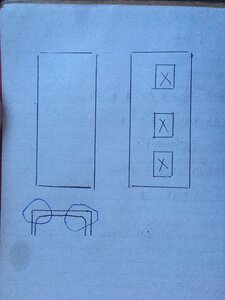
If you took a piece of C channel and cut a bunch of holes in it....how much would you weaken it?
C channel is strongest in the corners, where the most steel is, right?
So as pictured the “x” would be missing. I screwed up the drawing a bit but I was thinking if it was 5-6” tall C channel you could cut a 3”x4” hole every six inches and not really weaken the main piece of C channel