I said I'd do a quick survey of the happy vise, here are the results. Whats acceptable to someone is variable thing but for me and imo its a poor show putting out tooling like this. What should be universal though is disdain for false claims. I've had roles in two business that exposed me to manufacturing in the China and 10 years ago vendors filling in a certificates was simply a marketing exercise....the certificates function is to tell the customer what they want to hear and if they don't notice, win! I was hoping things had changed as they start to discover branding. Anyway, I really dislike that style of commerce.
Test were done a pristine Starrett grade A inspection plate using a interapid 10ths indicator. The parallels are proven and everything was repeated several times to check for dead on repeatability
Indicating the four corners of vise ways shows that they are close to within tolerance
However on flipping the vise over and checking for parallelism, there is lots of variance across the surface. As much 002" over a few inches. That seems like a huge amount for a ground surface and as soon as you bolt it to something, the base will distort and would put the ways out of tolerance (the already are but just a wee bit)
you can see across this short area there is a 2 thou variation. At first I thought the fixed jaw must be warped and is pulling the base out of shape, but then the first test would have mirrored this, but those top surfaces were close to ok.
Where there is no doubt as to false claims is squareness. They claim its certified to .05mm per 100mm. I measure 8.5 thou over 6" which equates to .096mm over 100m! That square is mitutoyo certified grade 00, bought new by yours truly and only used very rarely and only for inspections. certified to 5 microns or 150mm. That is very loose standard by tooling standards, and this one is almost twice that
Everyone has to decide for themselves what they want and whats acceptable, but go in eyes wide open. If there was ever any doubt about the credibility of certificates and claims of these manufacturers, hopefully this shows what we're up against
Here's a short video of the tests.
Test were done a pristine Starrett grade A inspection plate using a interapid 10ths indicator. The parallels are proven and everything was repeated several times to check for dead on repeatability
Indicating the four corners of vise ways shows that they are close to within tolerance
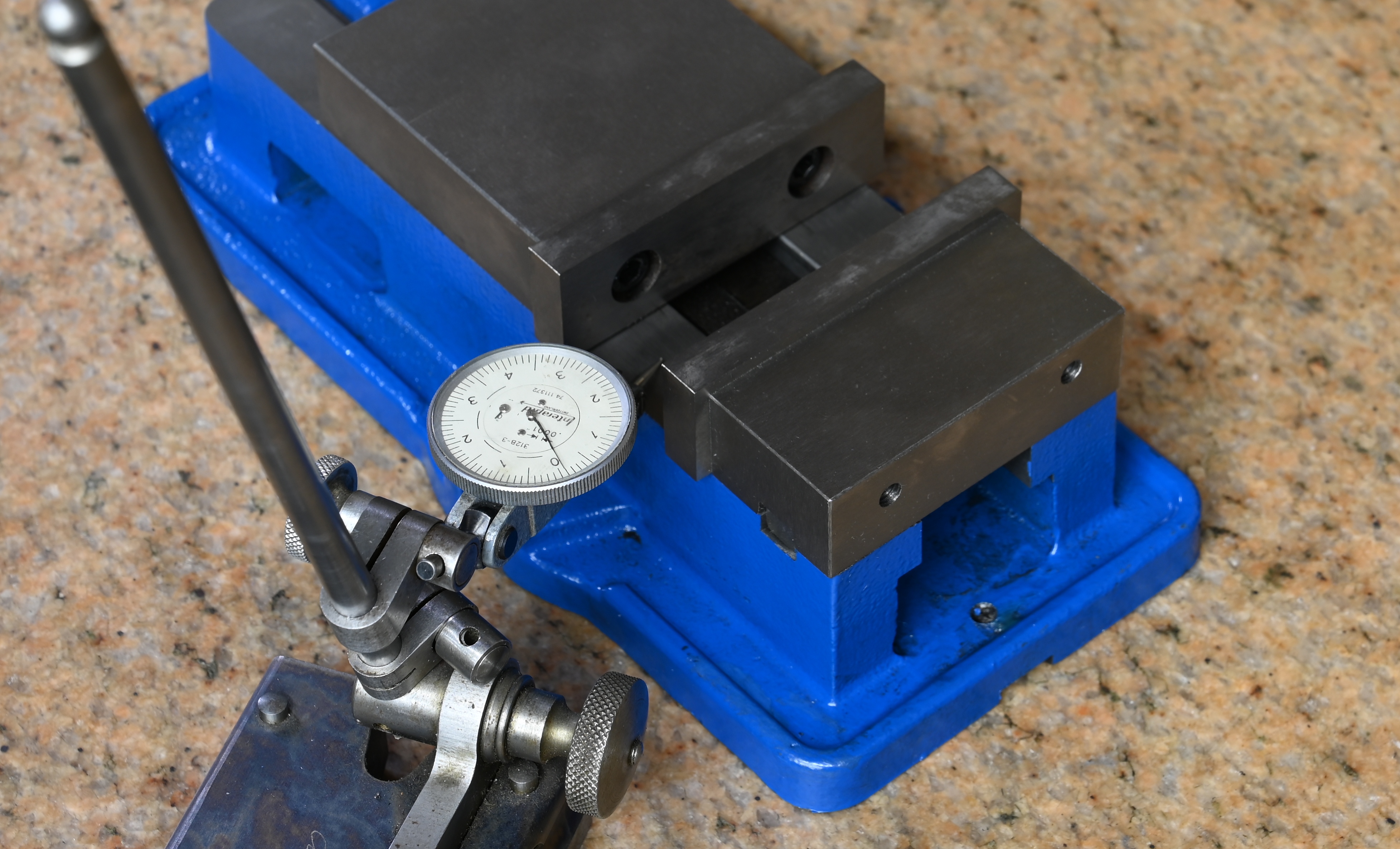
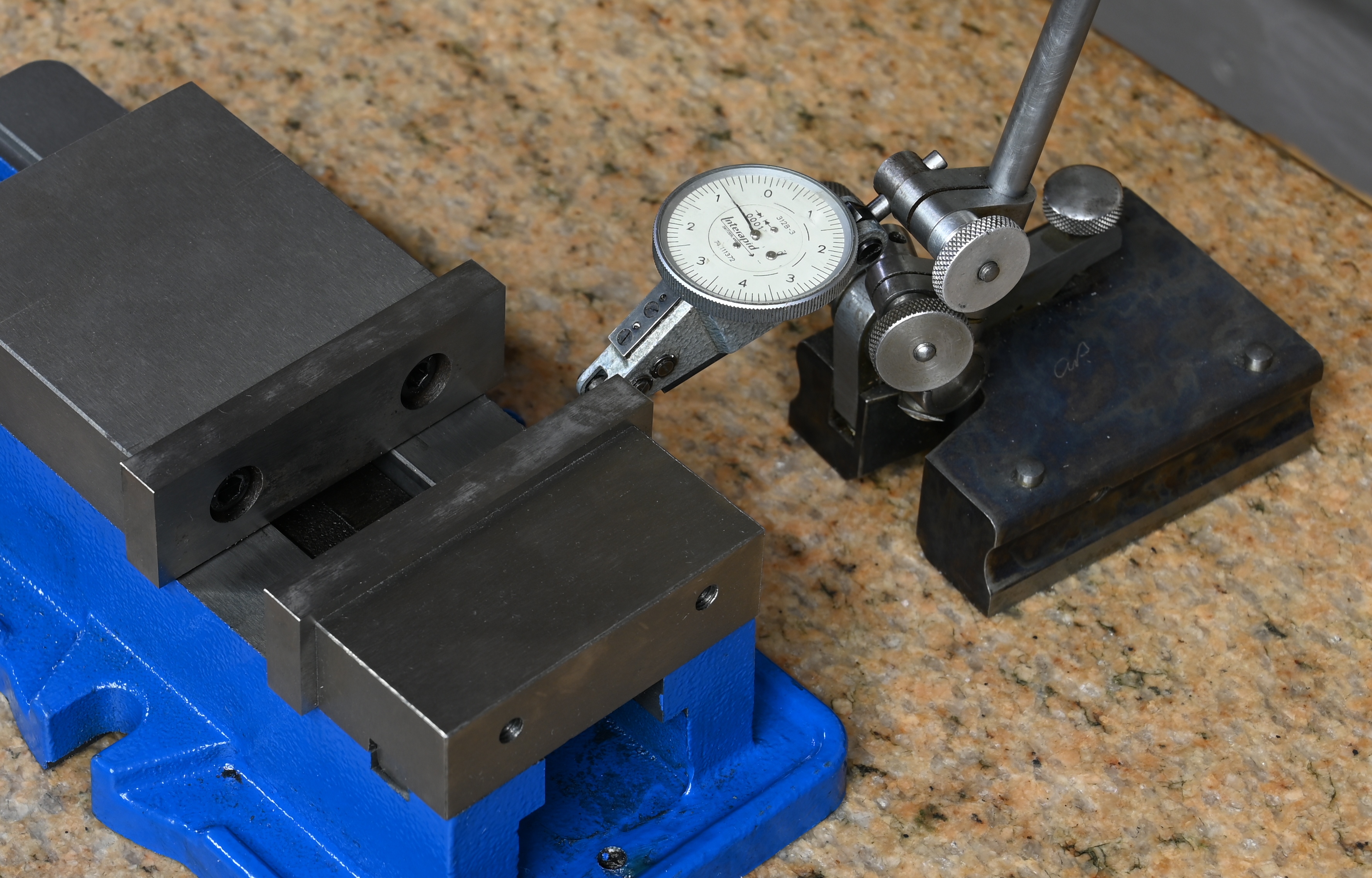
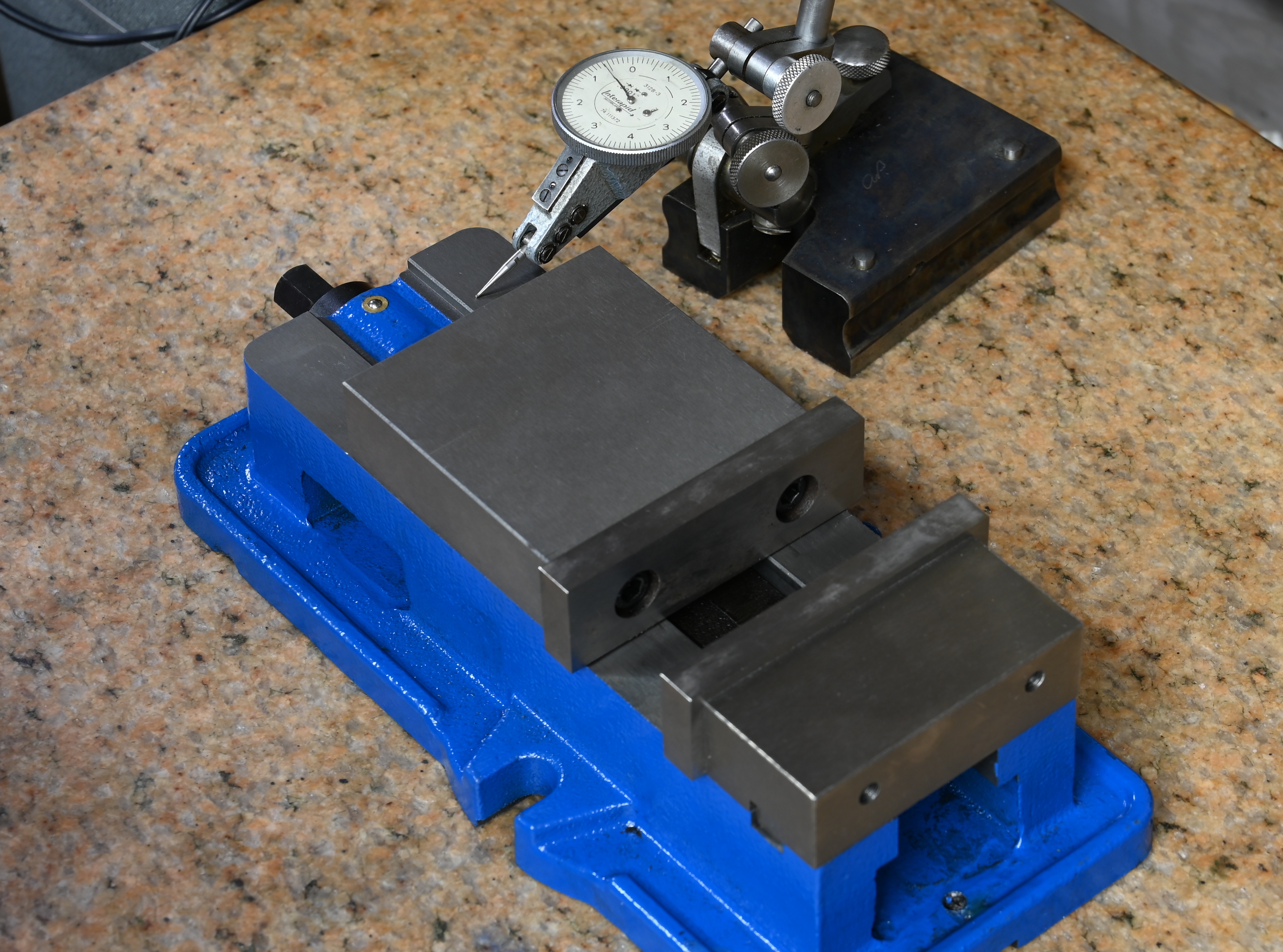
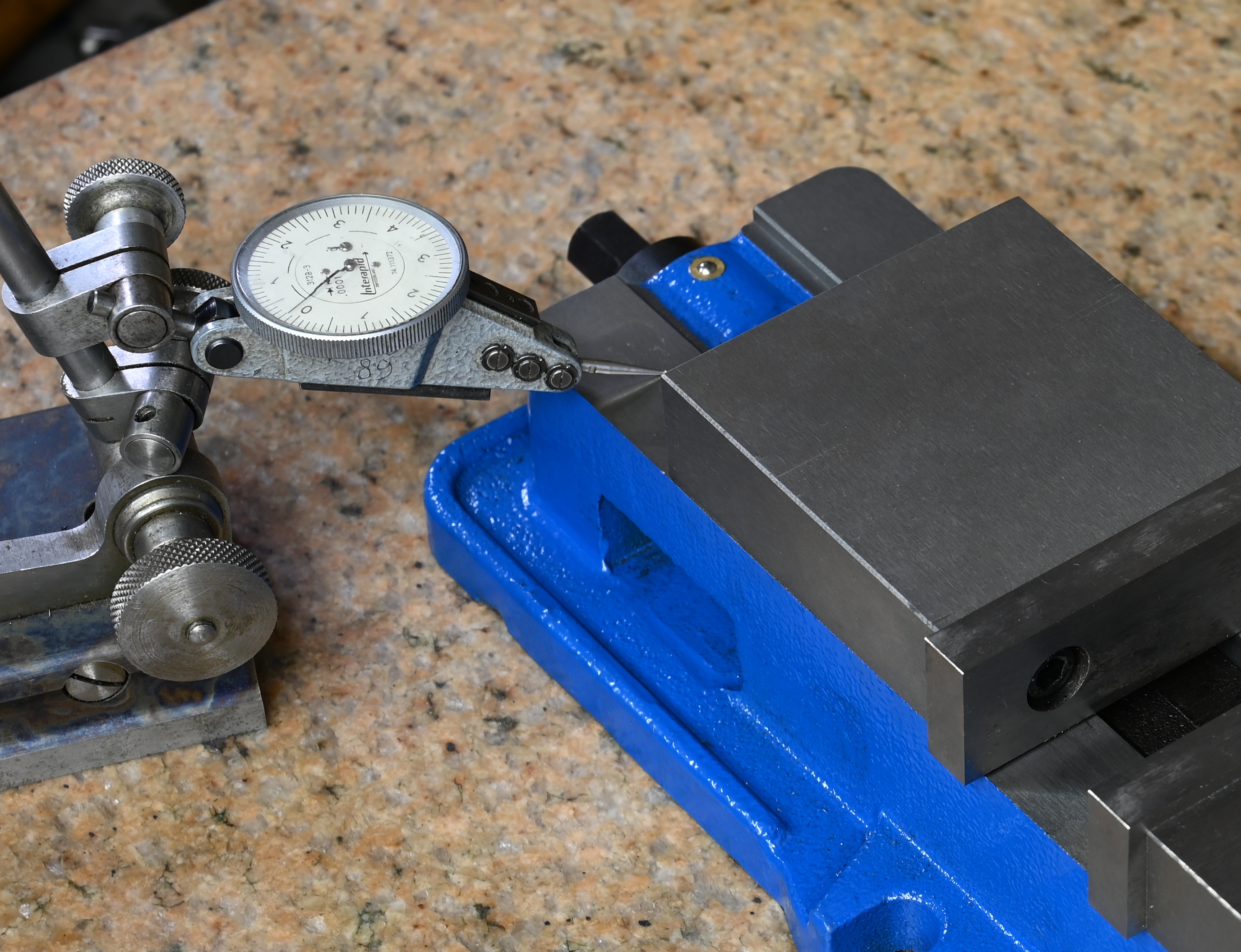
However on flipping the vise over and checking for parallelism, there is lots of variance across the surface. As much 002" over a few inches. That seems like a huge amount for a ground surface and as soon as you bolt it to something, the base will distort and would put the ways out of tolerance (the already are but just a wee bit)
you can see across this short area there is a 2 thou variation. At first I thought the fixed jaw must be warped and is pulling the base out of shape, but then the first test would have mirrored this, but those top surfaces were close to ok.
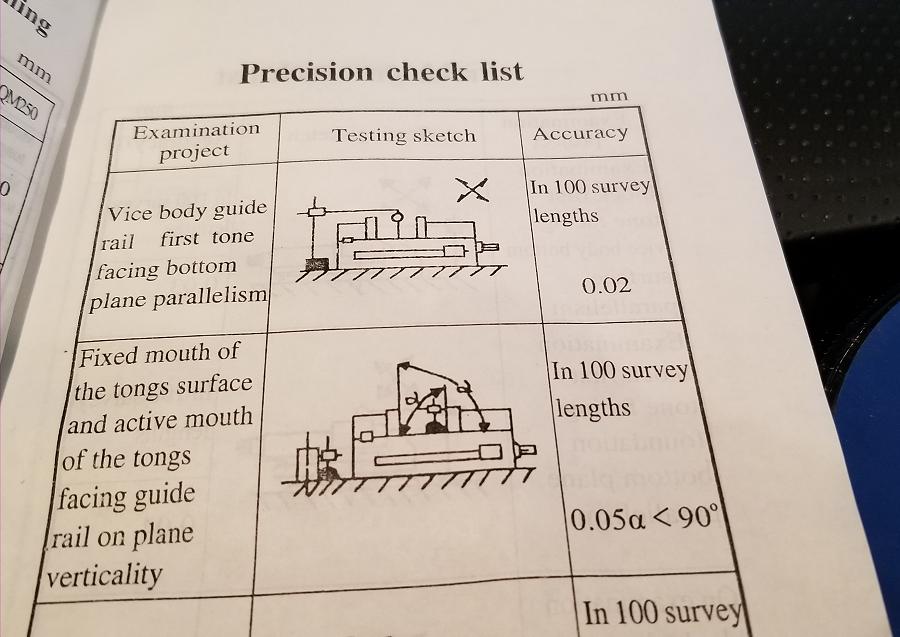
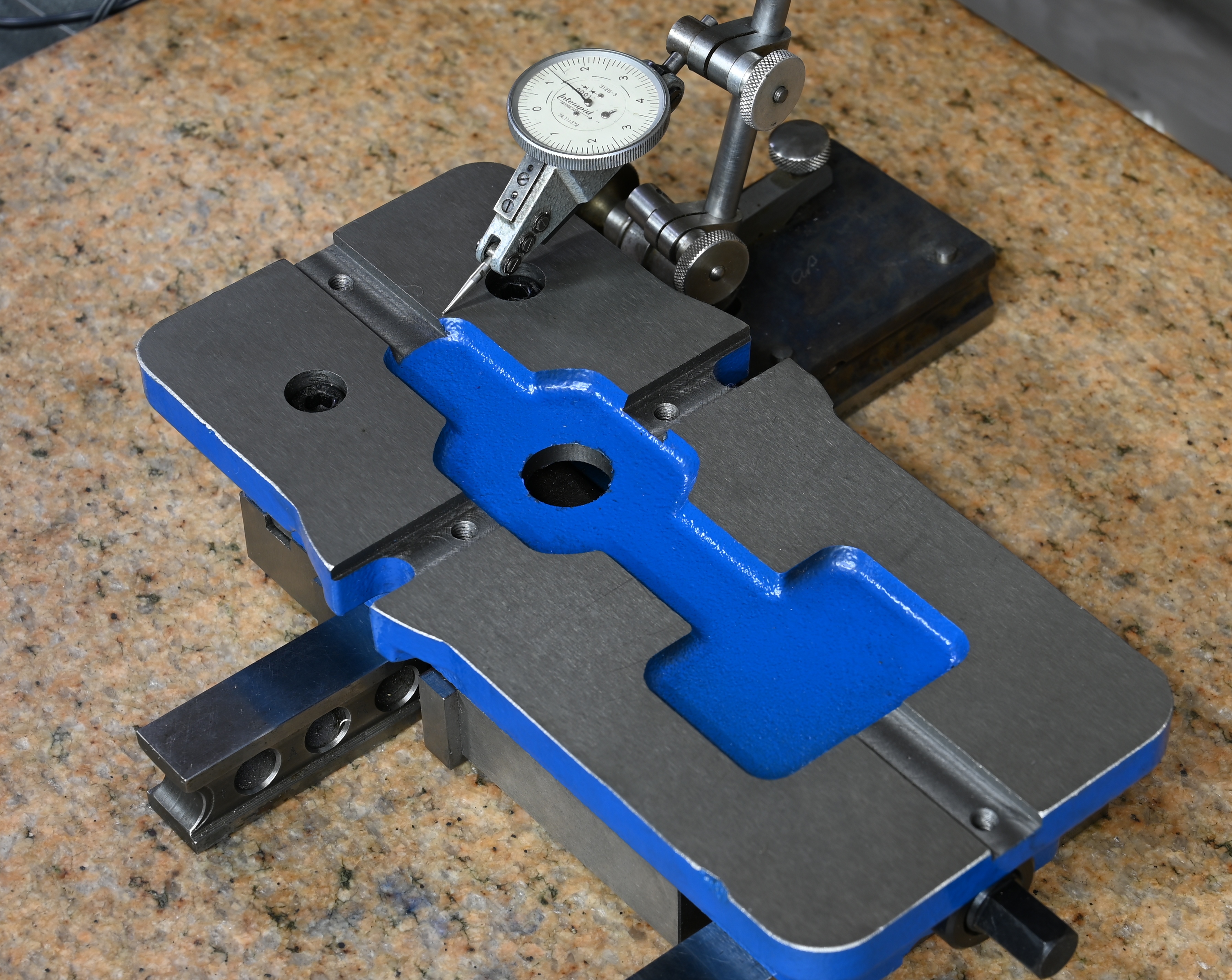
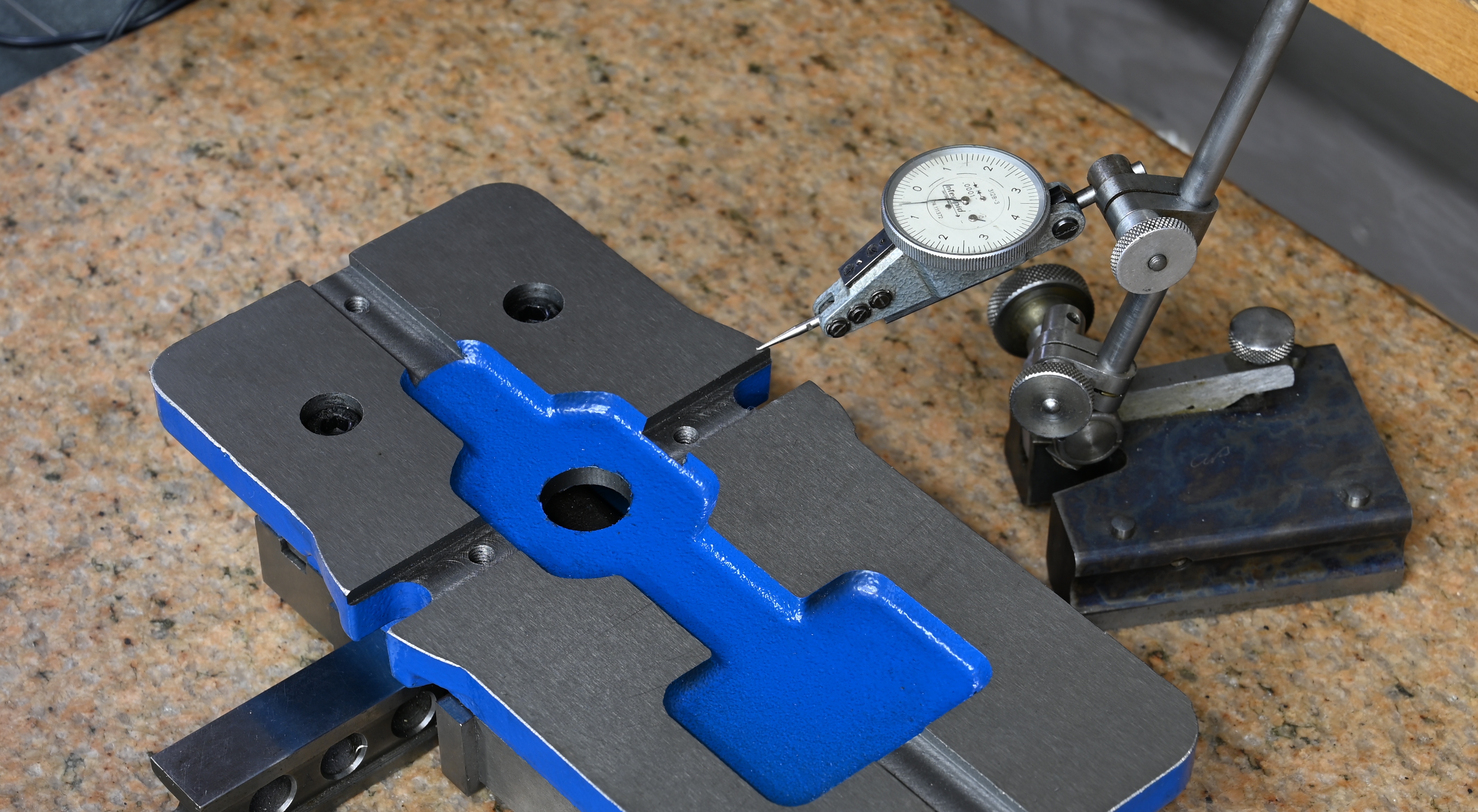
Where there is no doubt as to false claims is squareness. They claim its certified to .05mm per 100mm. I measure 8.5 thou over 6" which equates to .096mm over 100m! That square is mitutoyo certified grade 00, bought new by yours truly and only used very rarely and only for inspections. certified to 5 microns or 150mm. That is very loose standard by tooling standards, and this one is almost twice that
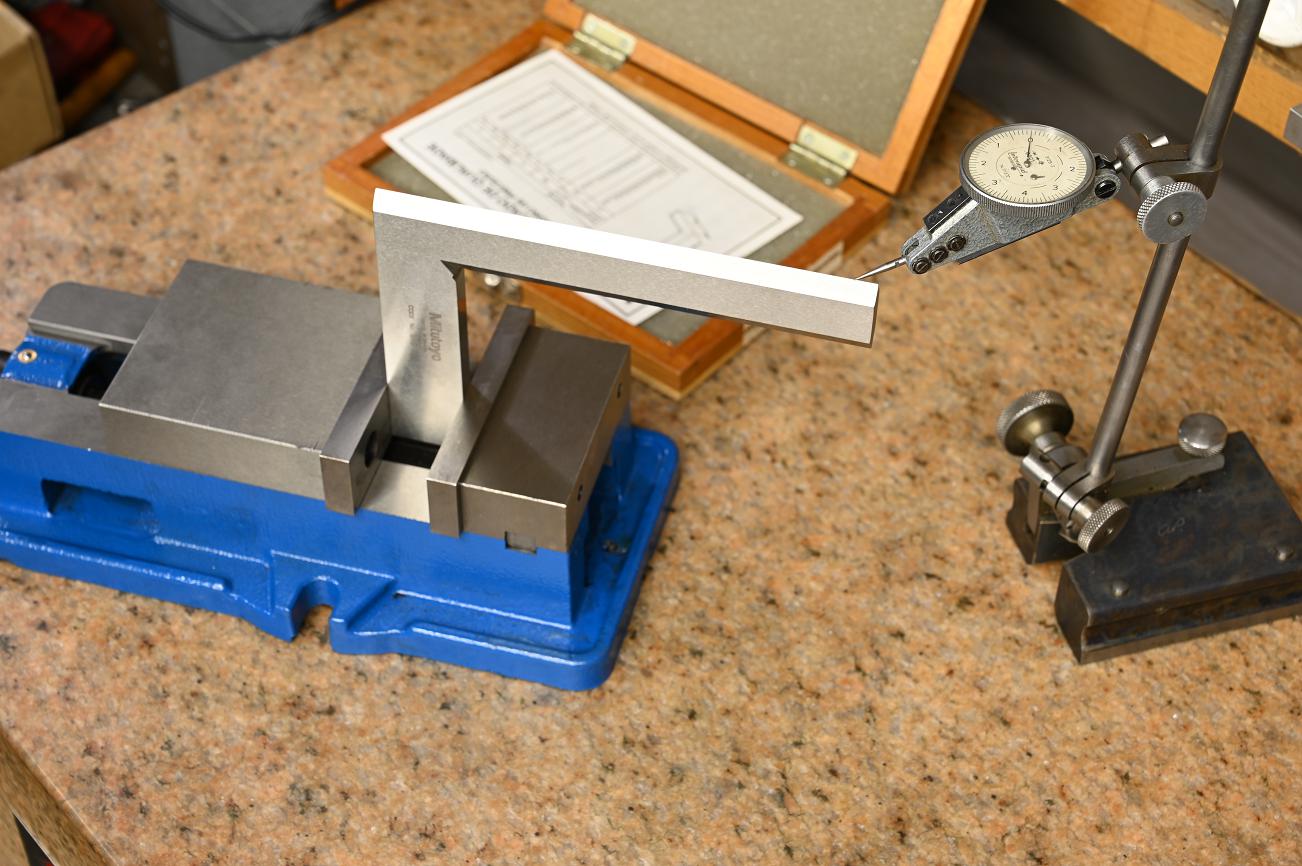
Everyone has to decide for themselves what they want and whats acceptable, but go in eyes wide open. If there was ever any doubt about the credibility of certificates and claims of these manufacturers, hopefully this shows what we're up against
Here's a short video of the tests.
Last edited: