This is a 9x36 Bridgeport clone, made in Taiwan with the Mehanite castings, I have owned it since new and it's seen light work for about 25 years. It is well made and sufficiently accurate for my home shop work. Until recently however, when the spindle bearings now make a rattling noise when in high speed mode. Also I can move the tip of a tool +/- 1mm laterally and the slop in the spindle is quite obvious. I have a video of the problem, but uploading that to this site is not happening.
As far as I can tell, the quill sleeve is sound, and there is no additional play with the quill fully lowered.
What would be involved in replacing the old bearings? I have a 20 Ton press to squeeze them in, but extracting the bearings is going to be a nasty job. Has anyone done this? Are any special tools needed? Can anyone recommend a Canadian source for parts for these machines?
Advice appreciated!
As far as I can tell, the quill sleeve is sound, and there is no additional play with the quill fully lowered.
What would be involved in replacing the old bearings? I have a 20 Ton press to squeeze them in, but extracting the bearings is going to be a nasty job. Has anyone done this? Are any special tools needed? Can anyone recommend a Canadian source for parts for these machines?
Advice appreciated!
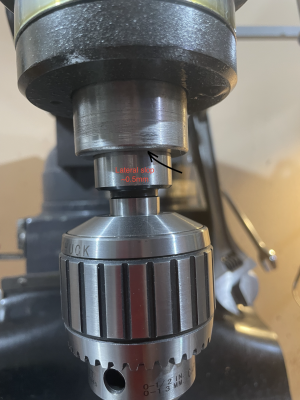