painly
Member
What I have come up with for suitable materials are 4340 or 4140, or in stainless, 416. But to get the properties desirable, these materials need heat treatment. This is the conundrum I am faced with, without a furnace. My question is whether or not there is a machinable, on kiddy machines, metal for my purpose that I can get away without hardening post-machining?
The Spindle and where it broke for me. This spindle is from the tongsheng tsdz2 ebike motor and is notorious for breaking under heavy use, however, these kits rarely see heavy use, so no one has produced an aftermarket alternative. I assume this is originally made of c40? or something similar. They are also produced with a poor design prone to stress risers as you can see; where mine broke. This axle has 2 degree tapers on either end and other than that, which I am half sure I can pull off, is a rather simple exercise in machining without the need for special tools...other than a furnace.
Thanks for any advice!
Barrett
The Spindle and where it broke for me. This spindle is from the tongsheng tsdz2 ebike motor and is notorious for breaking under heavy use, however, these kits rarely see heavy use, so no one has produced an aftermarket alternative. I assume this is originally made of c40? or something similar. They are also produced with a poor design prone to stress risers as you can see; where mine broke. This axle has 2 degree tapers on either end and other than that, which I am half sure I can pull off, is a rather simple exercise in machining without the need for special tools...other than a furnace.
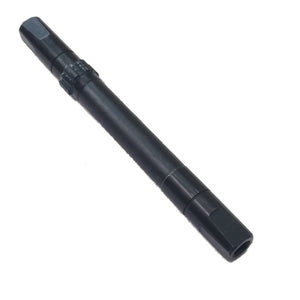
Thanks for any advice!
Barrett