VicHobbyGuy
Ultra Member
Baby steps here....
Today's project: Flywheel for a simple small model engine (Wobbler/Oscillating cylinder type - absolute beginner project)
Material 2" 1018 steel
Central boss is about 12mm diameter, recess is about 12mm wide.
I went through my collection of lathe tools trying to do this 'little job' ("Where did the day go???").
I got the recess starrted with a bunch of different turning tools, mostly using the 'point' of a 90 deg carbide insert tool. That worked OK for the central part of the recess, but working out to the edges was the challenge. The recess is pretty narrow and it's difficult to fit a tool in there without part of it rubbing.
I ended up using a boring bar-type tool, cutting the outer part of the recess 'normally' , then running the lathe in reverse and cutting 'from the back' to work to the central boss.
What's the right way ('standard method') to do this?
Today's project: Flywheel for a simple small model engine (Wobbler/Oscillating cylinder type - absolute beginner project)
Material 2" 1018 steel

Central boss is about 12mm diameter, recess is about 12mm wide.
I went through my collection of lathe tools trying to do this 'little job' ("Where did the day go???").
I got the recess starrted with a bunch of different turning tools, mostly using the 'point' of a 90 deg carbide insert tool. That worked OK for the central part of the recess, but working out to the edges was the challenge. The recess is pretty narrow and it's difficult to fit a tool in there without part of it rubbing.
I ended up using a boring bar-type tool, cutting the outer part of the recess 'normally' , then running the lathe in reverse and cutting 'from the back' to work to the central boss.
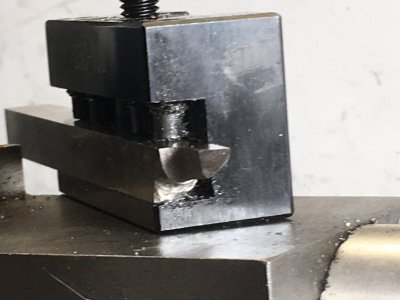
What's the right way ('standard method') to do this?