This is a lengthy post, sorry for all the detail but my understanding of electrical is very limited and I am trying to diagnose a problem with the machine. Advice and explanations are very much appreciated!!
I recently purchased a very nice Atlas Horizontal milling machine model MFB.
The mill is equipped with a 1/4 hp, single phase motor, 120volt. there is a switch with centre off, forward and reverse. A new chord has been fitted from the machine to the wall plug. When I flip the switch to forward or reverse there are sparks visible from inside the machine, sometimes the motor will start spinning in F or R and sometimes the electric panel breaker trips.
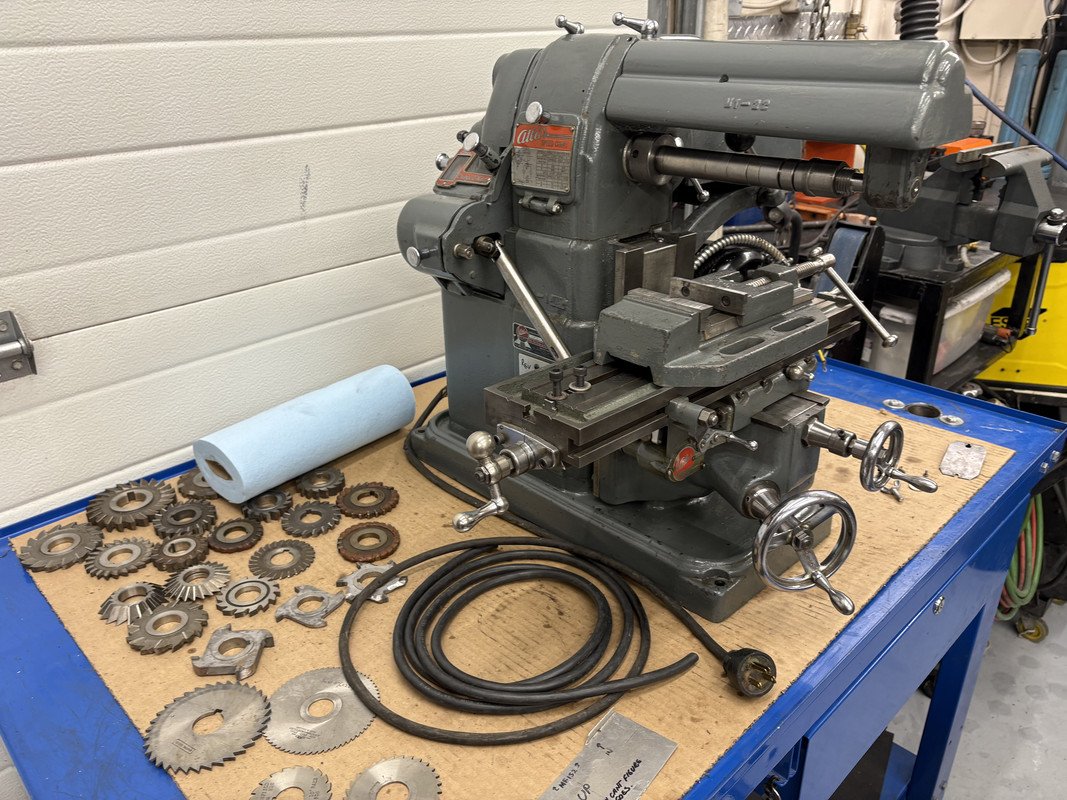
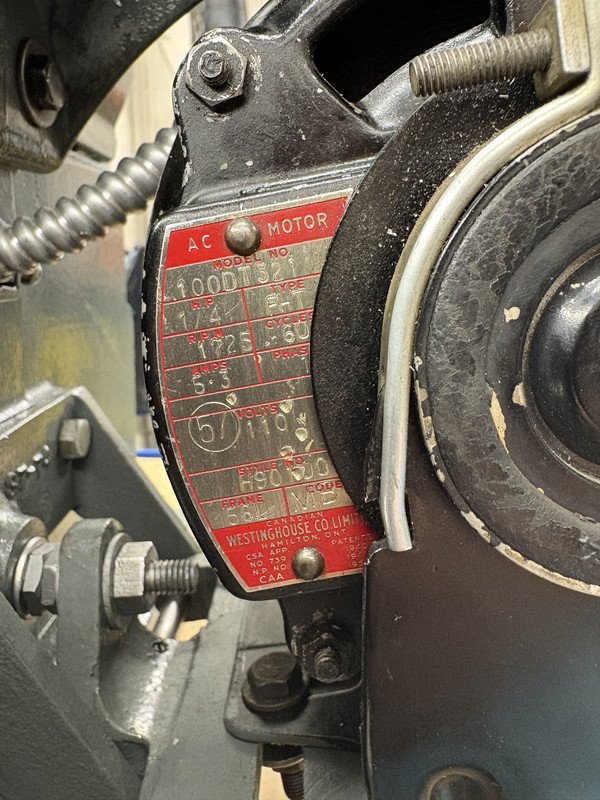
I removed the rear access panel to expose the pair of electromagnetic contactors, there are two of these modules and each has four brass fingers that act like automotive points. I washed everything down with electrical contactors cleaner, used Q tips to wipe everything.
When I plug in the machine and flip the switch back and forth between F and R there are sparks shooting out from the corresponding points contact and a smell of electrical burning.
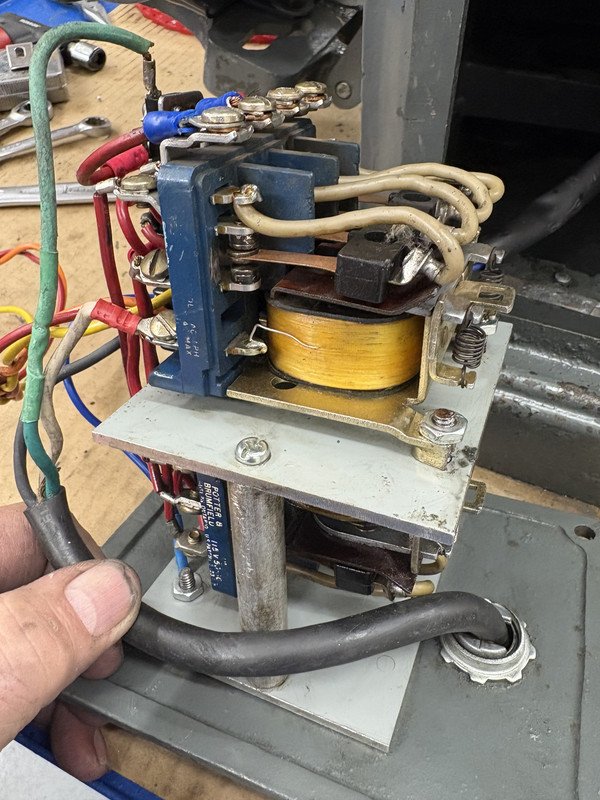
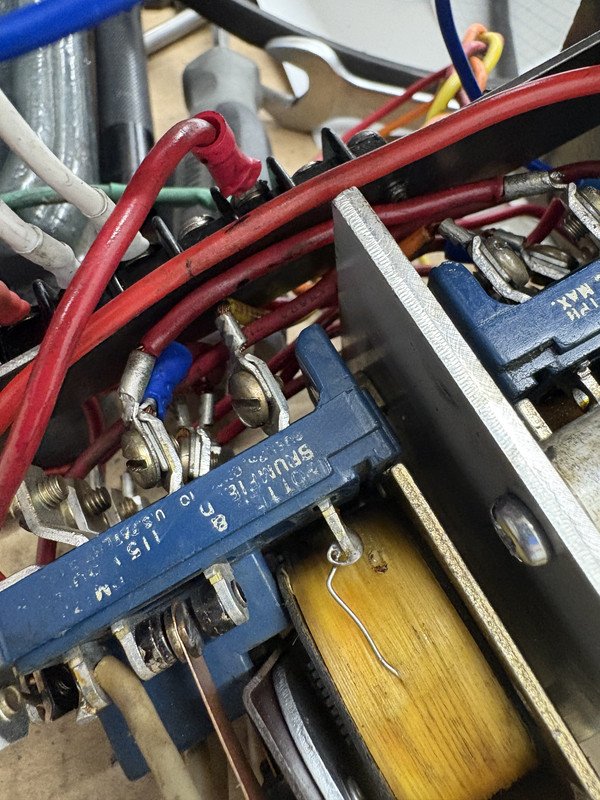
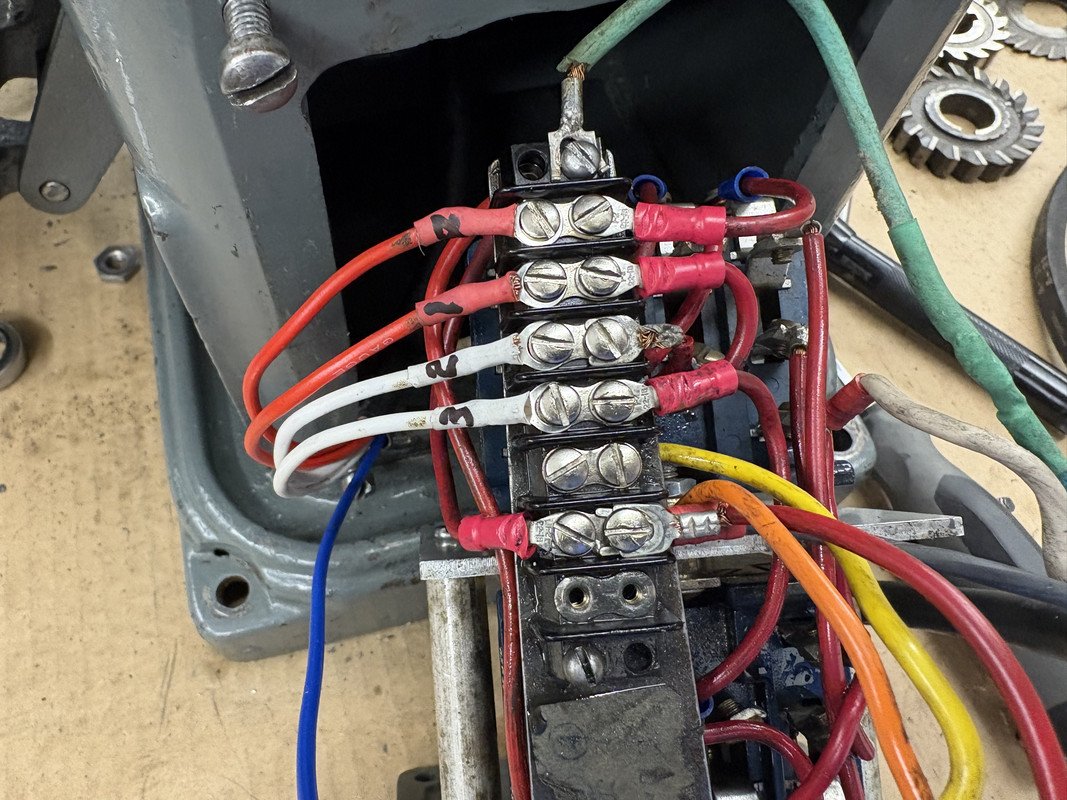
I removed the four wires to the motor and then flipped the switch back and forth, no sparks from the contactor points. Hook the motor back up and the sparks fly again.
I visited a friend who has a pump and electric motor company. He gave me a new motor to try out, this new motor has a pair of capacitor on the top. He showed me how to wire it up, two white wires from the contactor bus strip to the two white ‘line’ lugs on the motor. The two red wires from the contactor bus strip are joined to the red and black wires inside the motor access opening.
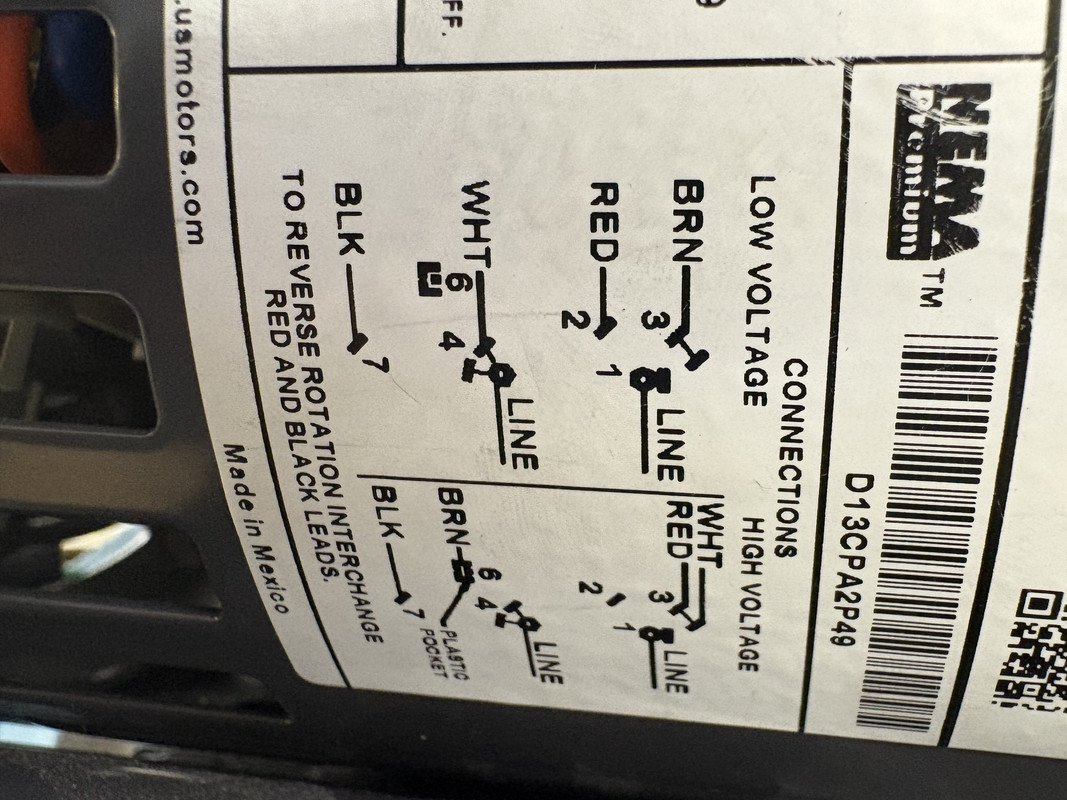
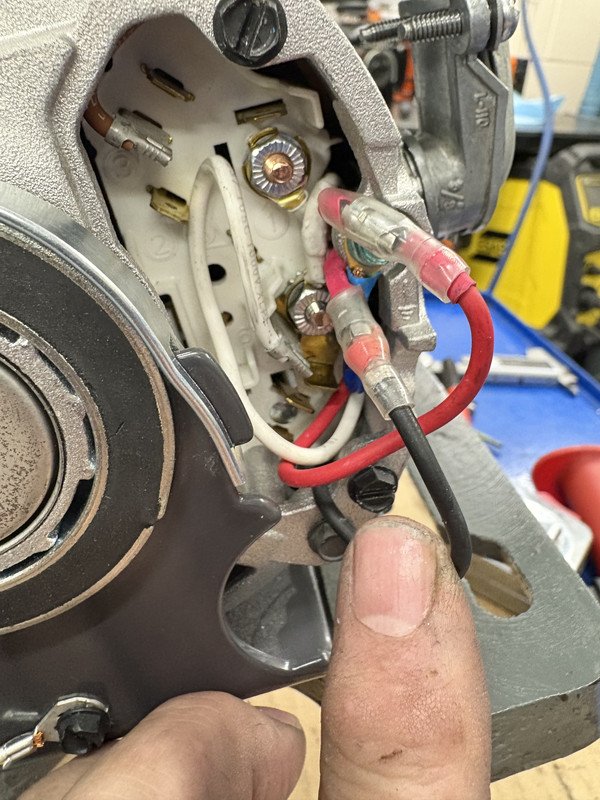
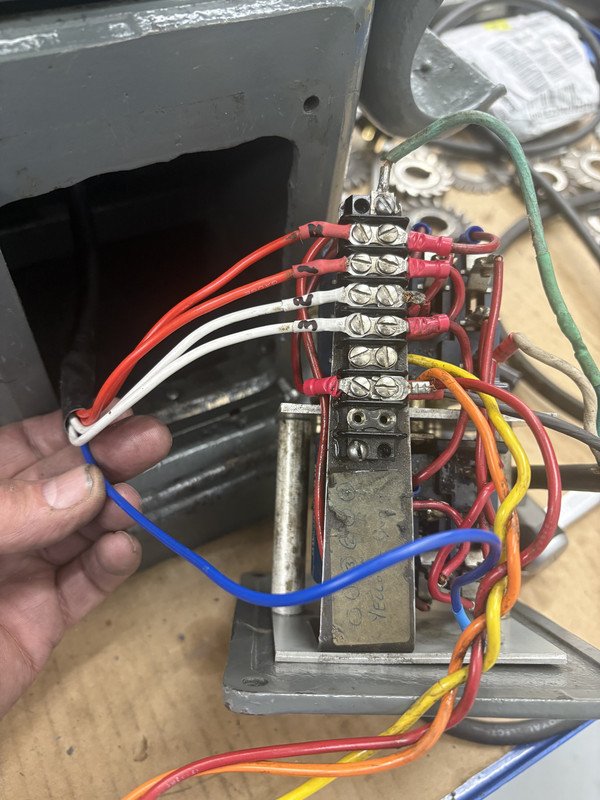
I hooked up all the wires to the contactor bus strip and I get sparks again when I flip the switch to F or R. I had the motor running for about 5 minutes in F and R. The motor case was very hot to the touch and I didn’t even have the drive belt hooked up to the spindle!
Something is very wrong.
While the motor was running it would sometimes seem to switch speeds up and down.
I am wondering if the old magnetic contactors are at fault?
I have a pair of new contactors I had purchased for my single phase 220 volt lathe, can I swap out the old contactors for these new 230v ones?
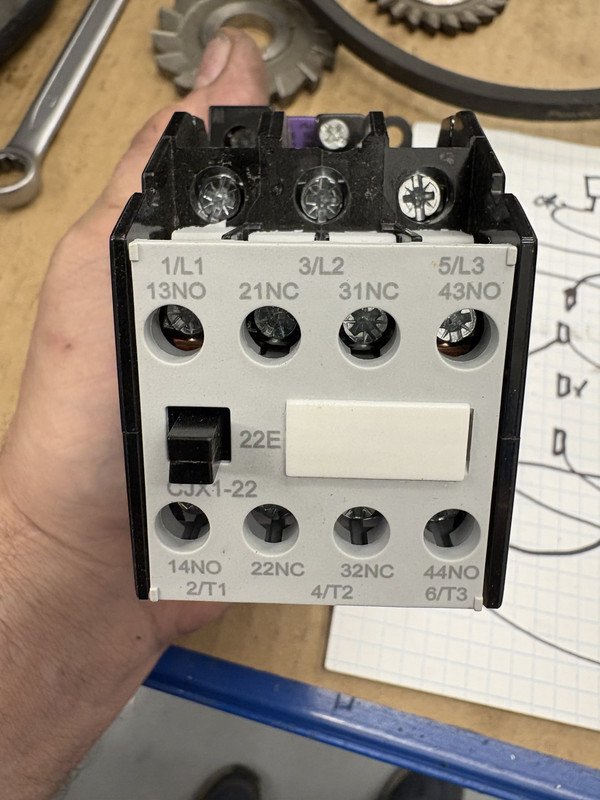
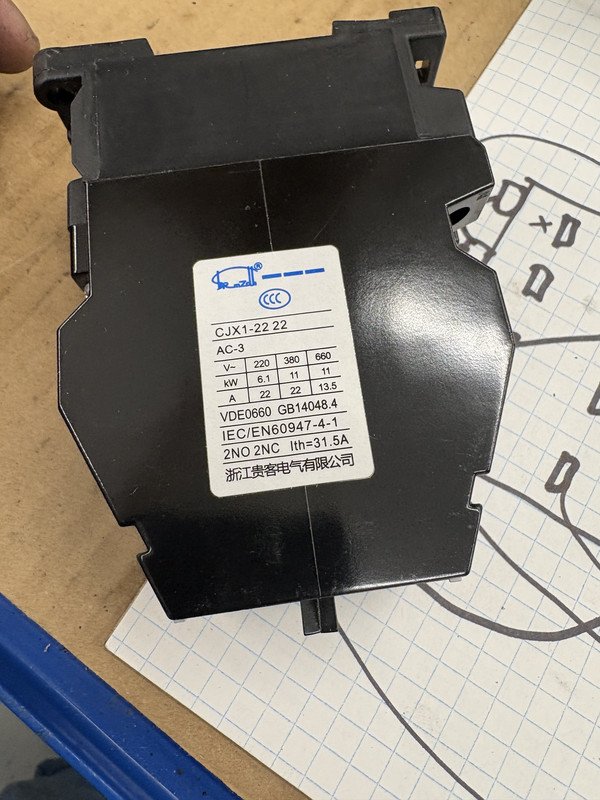
And if so any ideas on how to wire up these new contactors from the 120 volt wall outlet to the motor?
My crude wire diagram of the existing contactors and switch.
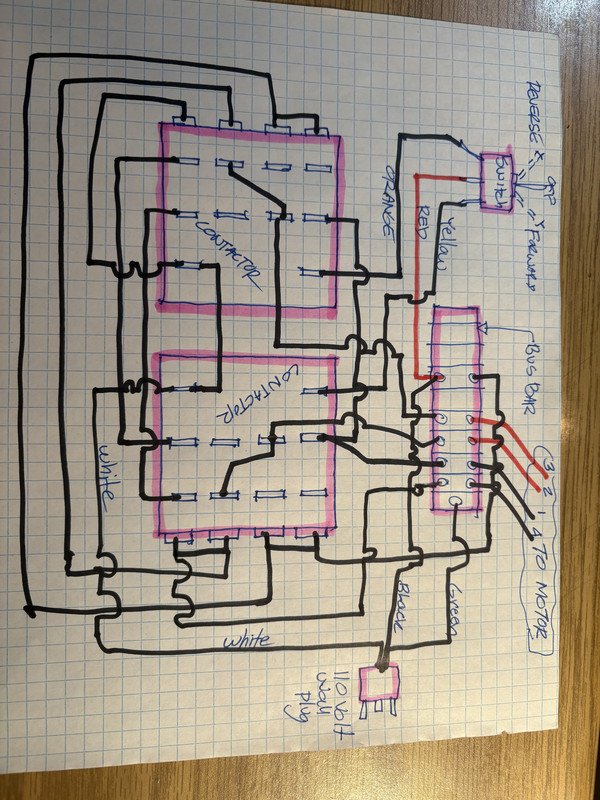
I recently purchased a very nice Atlas Horizontal milling machine model MFB.
The mill is equipped with a 1/4 hp, single phase motor, 120volt. there is a switch with centre off, forward and reverse. A new chord has been fitted from the machine to the wall plug. When I flip the switch to forward or reverse there are sparks visible from inside the machine, sometimes the motor will start spinning in F or R and sometimes the electric panel breaker trips.
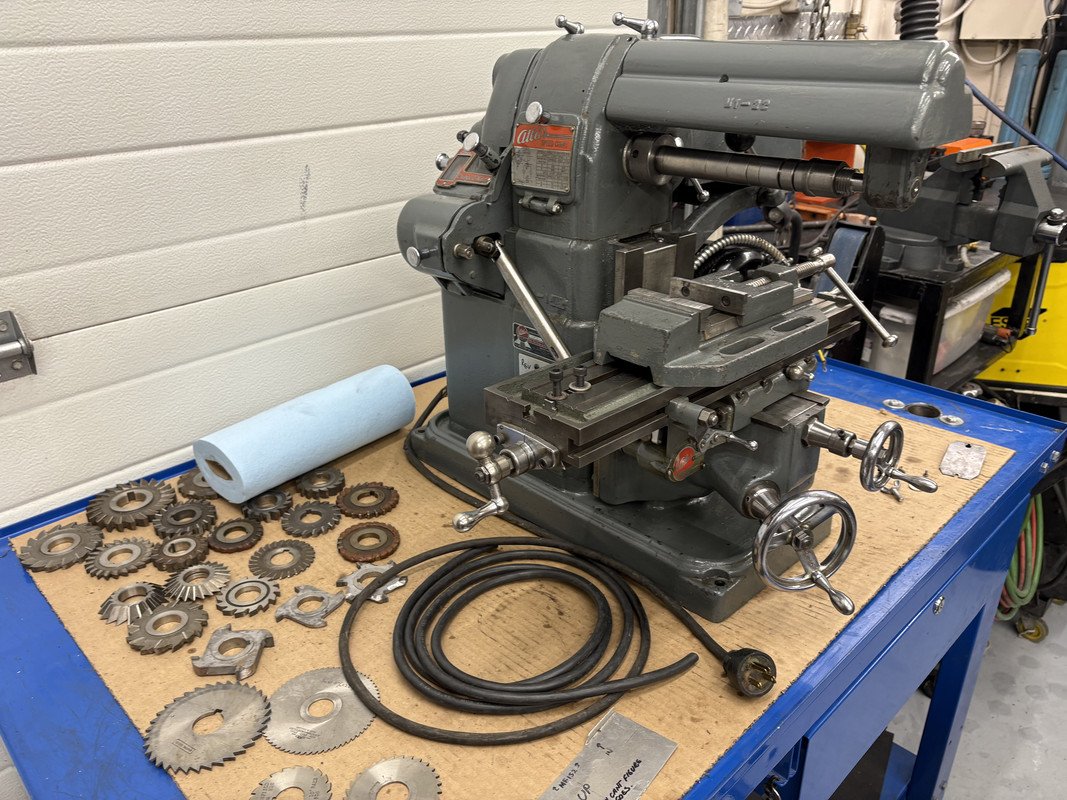
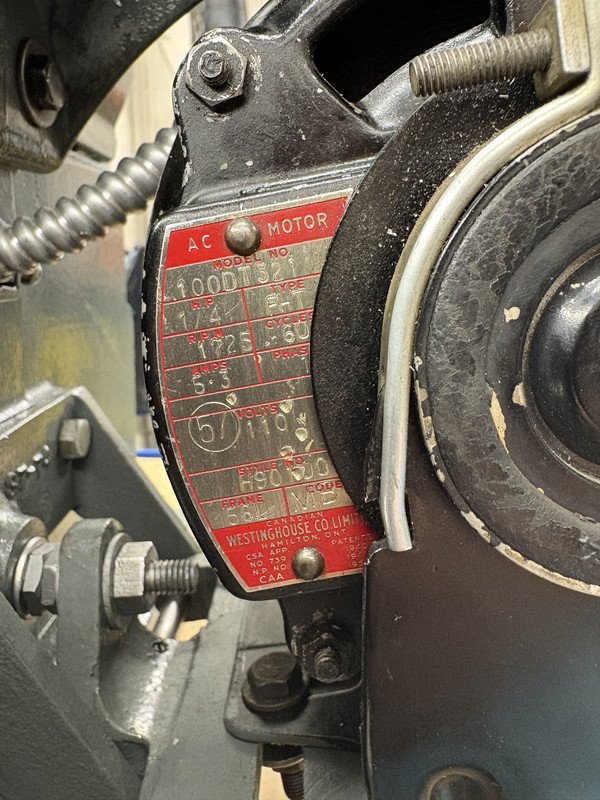
I removed the rear access panel to expose the pair of electromagnetic contactors, there are two of these modules and each has four brass fingers that act like automotive points. I washed everything down with electrical contactors cleaner, used Q tips to wipe everything.
When I plug in the machine and flip the switch back and forth between F and R there are sparks shooting out from the corresponding points contact and a smell of electrical burning.
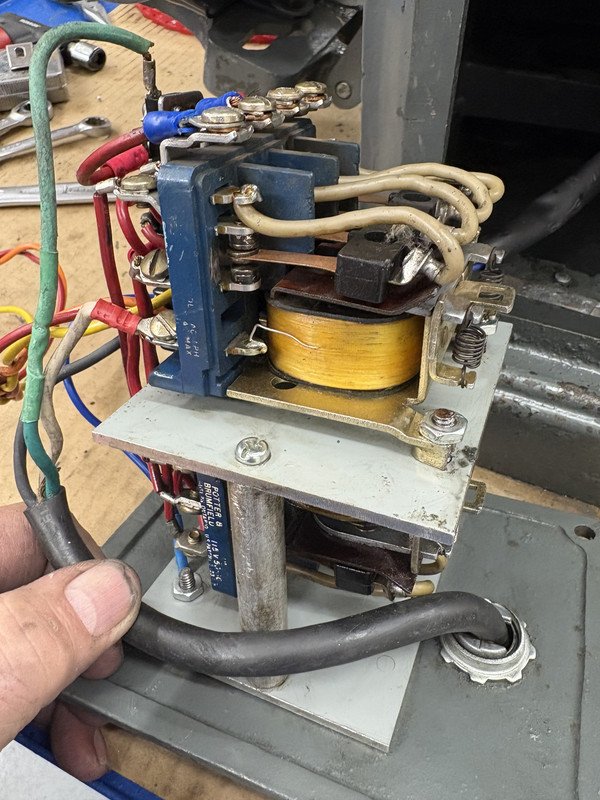
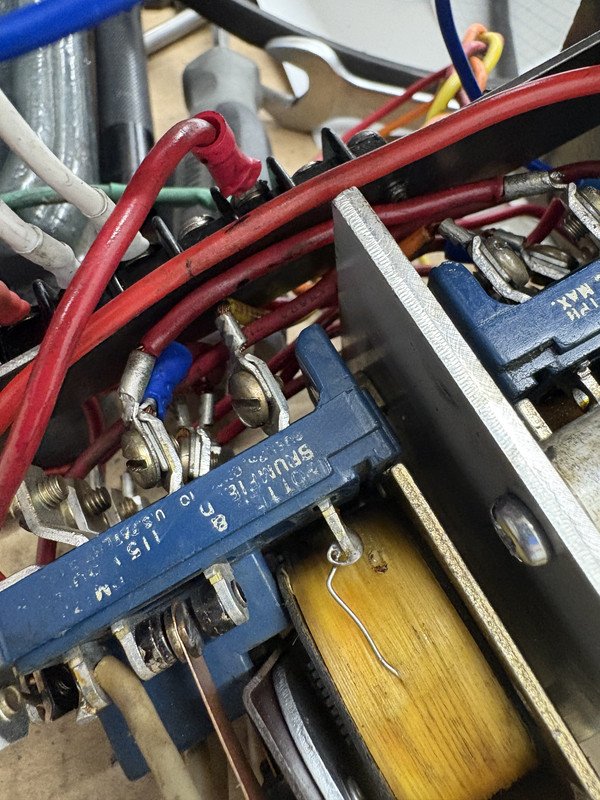
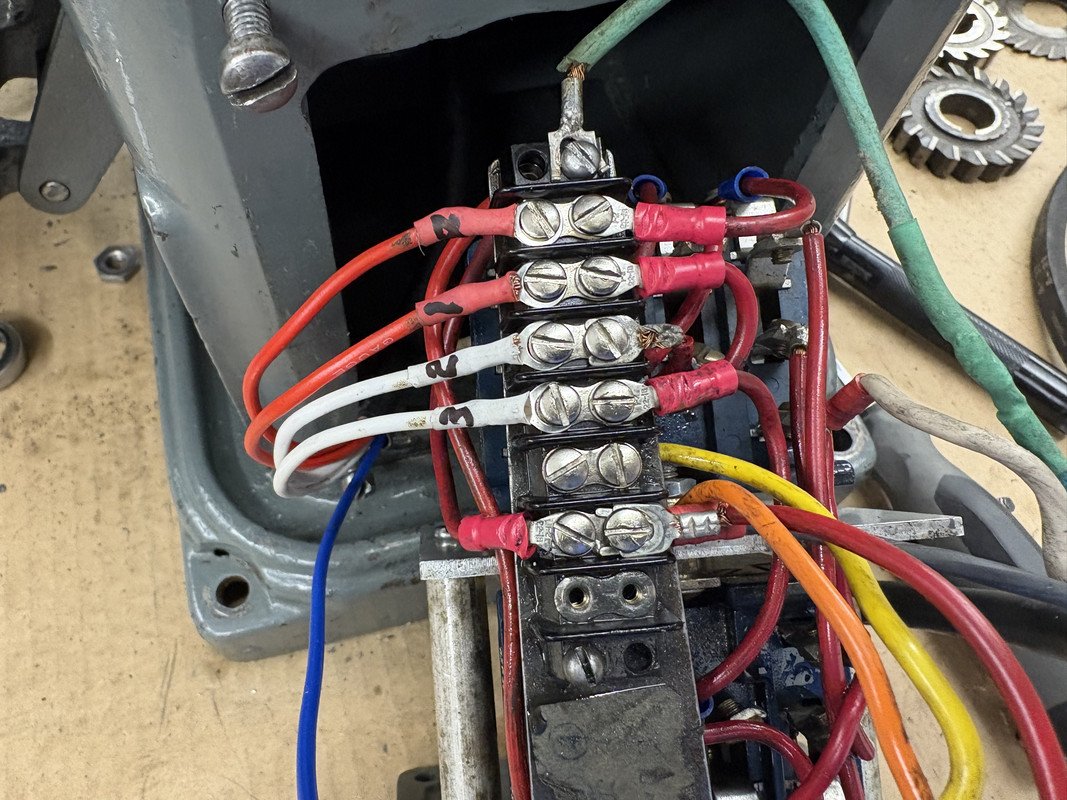
I removed the four wires to the motor and then flipped the switch back and forth, no sparks from the contactor points. Hook the motor back up and the sparks fly again.
I visited a friend who has a pump and electric motor company. He gave me a new motor to try out, this new motor has a pair of capacitor on the top. He showed me how to wire it up, two white wires from the contactor bus strip to the two white ‘line’ lugs on the motor. The two red wires from the contactor bus strip are joined to the red and black wires inside the motor access opening.
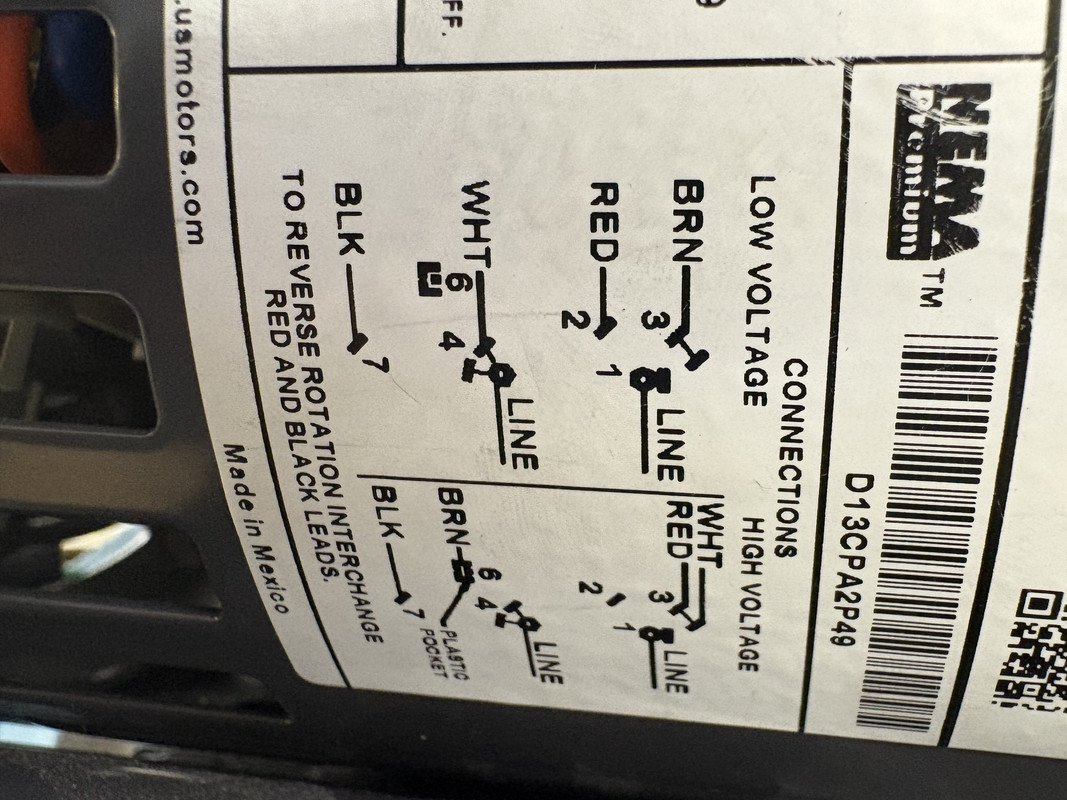
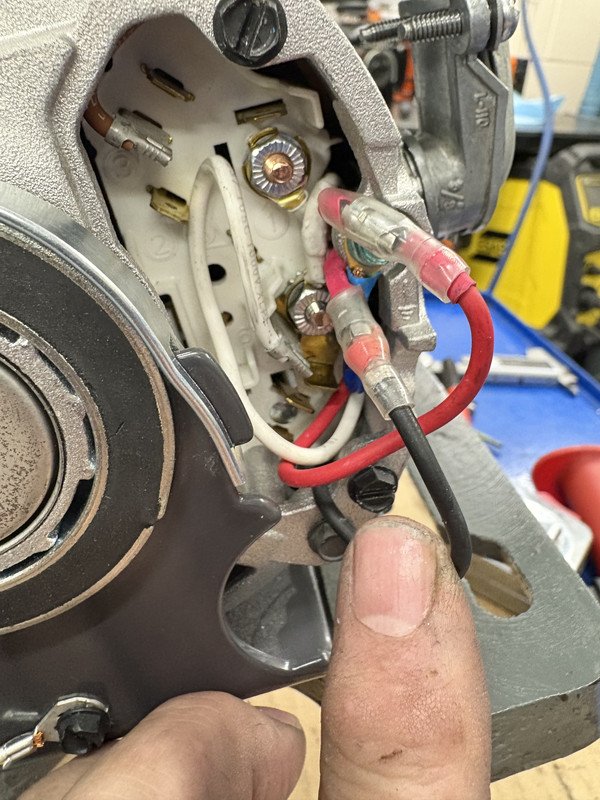
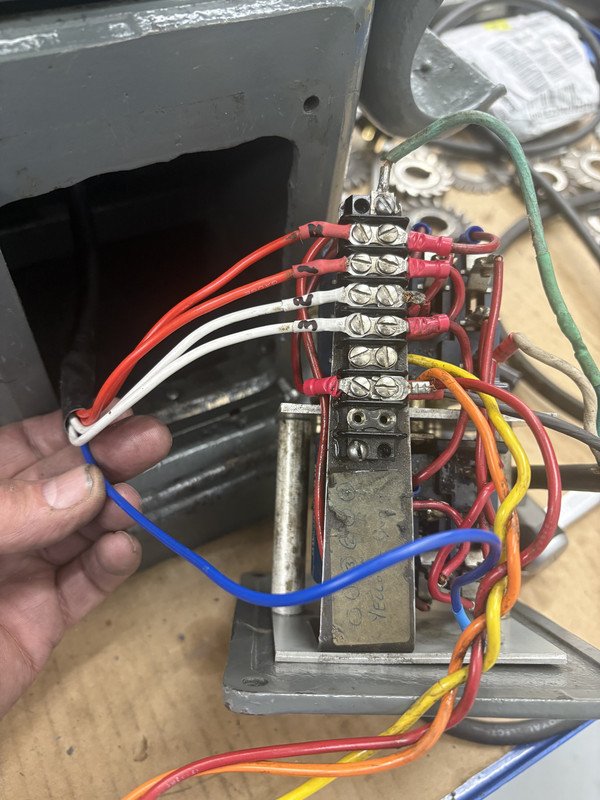
I hooked up all the wires to the contactor bus strip and I get sparks again when I flip the switch to F or R. I had the motor running for about 5 minutes in F and R. The motor case was very hot to the touch and I didn’t even have the drive belt hooked up to the spindle!
Something is very wrong.
While the motor was running it would sometimes seem to switch speeds up and down.
I am wondering if the old magnetic contactors are at fault?
I have a pair of new contactors I had purchased for my single phase 220 volt lathe, can I swap out the old contactors for these new 230v ones?
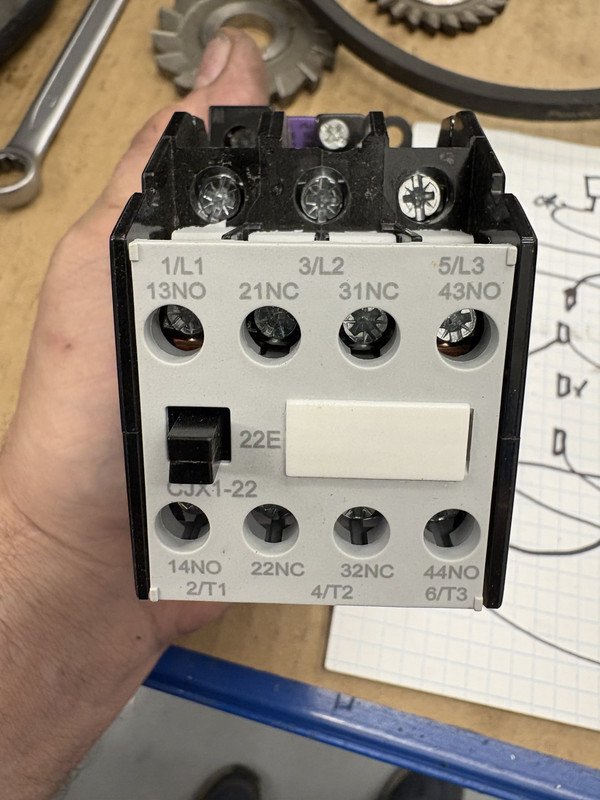
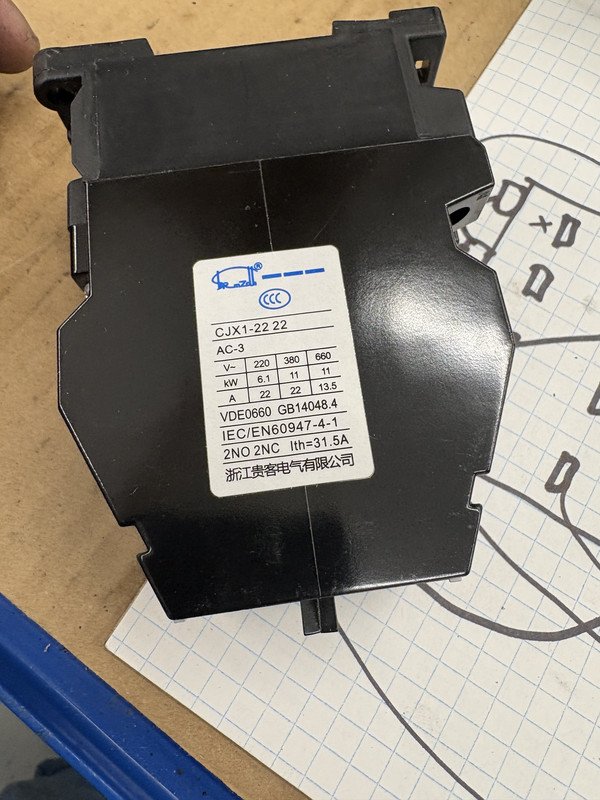
And if so any ideas on how to wire up these new contactors from the 120 volt wall outlet to the motor?
My crude wire diagram of the existing contactors and switch.
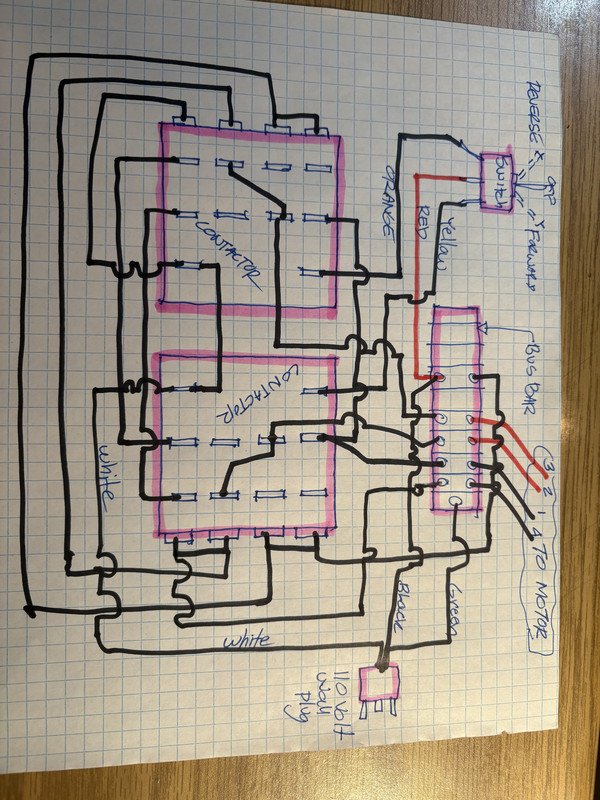
Last edited: