Tomc938
Ultra Member
I'm almost ready to attach the apron on my 1440, but I noticed some damage. I think the bolt bottomed out and broke a chunk of the casting away. Besides being one of the 5 bolts that hold the apron onto the saddle, the missing piece is also home to a channel that gets oil to the bearing surfaces on the back of the apron. So although from a structural point of view it might be OK, it serves another important function.
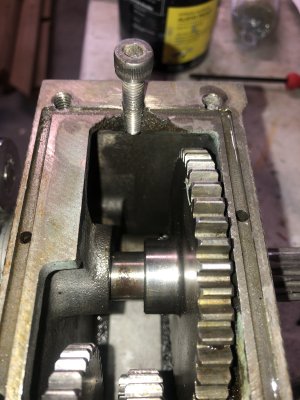
I was thinking of milling out a section back past the threads of the hole so I can redrill and tap the hole. I would use a few small bolts (4?) to hold the repair piece in place. There is lost of spare room to the left of the gear as the picture sits. The red line in the next picture shows where I would mill out. The bolts would come through the housing from the back. (Far side of the piece as it is displayed.
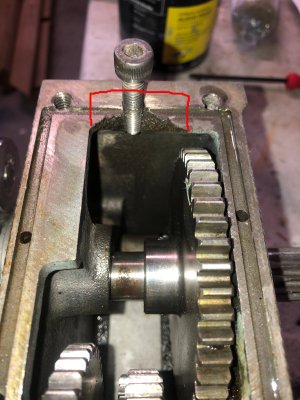
I would use Plastic Steel to make the joint water tight and mill a small channel that matches the channel and allows the oil to flow.
Thoughts? Does this seem like a reasonable way to repair this?
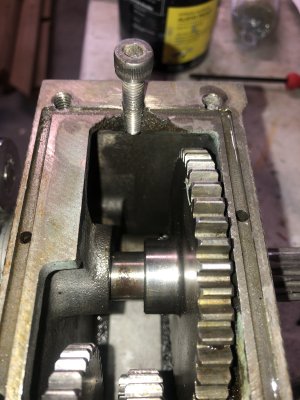
I was thinking of milling out a section back past the threads of the hole so I can redrill and tap the hole. I would use a few small bolts (4?) to hold the repair piece in place. There is lost of spare room to the left of the gear as the picture sits. The red line in the next picture shows where I would mill out. The bolts would come through the housing from the back. (Far side of the piece as it is displayed.
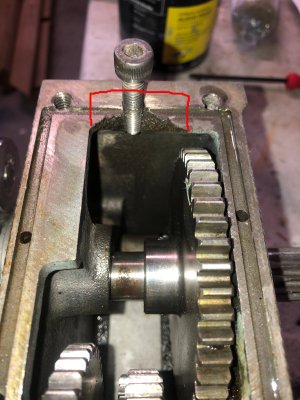
I would use Plastic Steel to make the joint water tight and mill a small channel that matches the channel and allows the oil to flow.
Thoughts? Does this seem like a reasonable way to repair this?