Well I think I am done. Maybe a sticker or two will be needed to be printed up a the sign shop, but otherwise done.
One of the things I do for my shop machines is make covers for them as they may sit idle for many months due to other projects being address. Sanding, ripping wood and grinding body metal all put a lot of dust in the air in the shop and machines have oil on them and the dust just sticks.
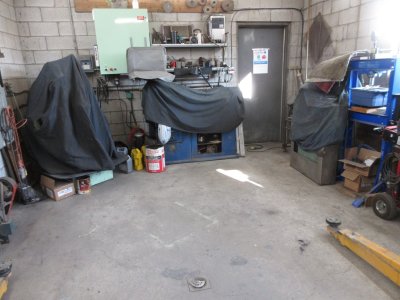
So in keeping with fashion I took a ride to Fabric Land St. Catharines and purchased some denim material to make a cover. Took some measurements, cut the sections and loaded the bobbin and thread into the sewing machine in my basement.
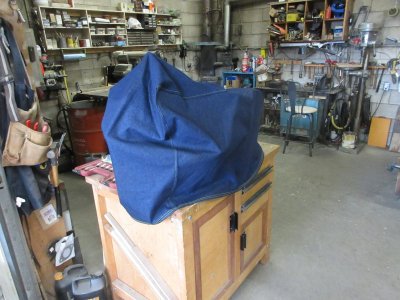
While in St. Catharines I also stopped in at Princess Auto and purchased some wrenches to be dedicated to this machine. Then to keep all of the paper work and manuals I made a sheet metal box so that they would be handy to the machine.
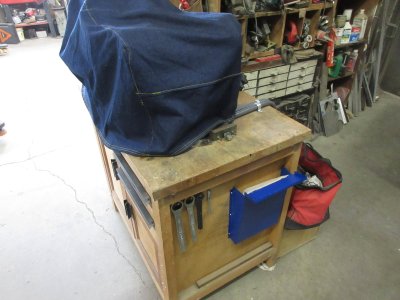
So what is all this worth. There is a saying that an item is worth what a willing seller and a willing buyer agree upon for a said price. I have been watching an ebay item a 7' Ammco that has been for sale for months, price now dropped to $2250 USD, still no takers.
https://www.ebay.com/itm/2567750728...qTKWCujHZZnIoA+hQvyhZlXfaA==|tkp:BFBM_PnpycVl
I think a realistic price for my machine is about $1500 CND and possibly $300CND for the Hard Maple stand/bench, possibly. Looking into what I have into the machine. I purchased the machine, incomplete for $200, Electrical $200, Nuts, bolts, hand wheels $200, Paint $120, Blast sand $70, Tool holder $35, Tools $65, Cover Fabric $40 and a whole bunch of time. I have in direct costs $865. Restorations, seldom benefit the person doing the work, yet there is passion in restoring something to live on for many more years and to be appreciated by many. I do enjoy the challenge.
So I will share a few links of other things that I have sunk a lot of money and time into that some day a long time from now may be worth something to someone else. ( Just not me )
My 1953 John Deere Model 40 Short Track Crawler. One of 2262 made. $15K invested ( 2001 )
My Son's 1985 1/2 Mazda RX7 Sports Car, $30K invested. (2012)
My nephew's 1982 Fiat X1/9 Turbo Engine Swap. He paid for the parts and material $10K and I did all of the labour. (2024)
500 Abarth 1.4 Turbo swap. | XWeb Forums
It has been the tools that I have acquired over the years that have allowed me to make any and all of this to happen.
I say, live, dream, work and watch it happen.
All the best.
TonyK.
Grimsby Ontario Canada.
One of the things I do for my shop machines is make covers for them as they may sit idle for many months due to other projects being address. Sanding, ripping wood and grinding body metal all put a lot of dust in the air in the shop and machines have oil on them and the dust just sticks.
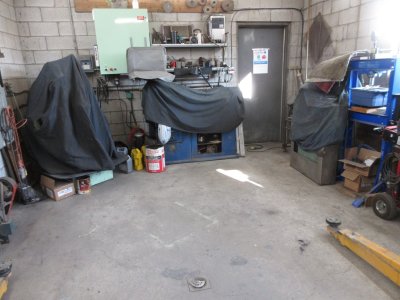
So in keeping with fashion I took a ride to Fabric Land St. Catharines and purchased some denim material to make a cover. Took some measurements, cut the sections and loaded the bobbin and thread into the sewing machine in my basement.
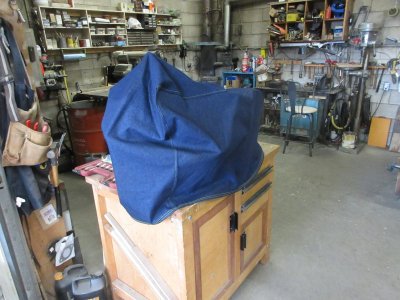
While in St. Catharines I also stopped in at Princess Auto and purchased some wrenches to be dedicated to this machine. Then to keep all of the paper work and manuals I made a sheet metal box so that they would be handy to the machine.
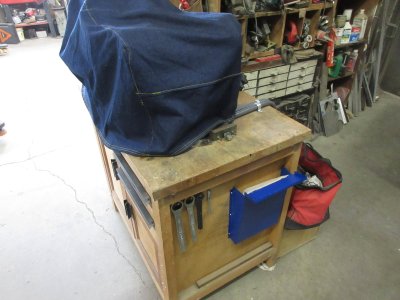
So what is all this worth. There is a saying that an item is worth what a willing seller and a willing buyer agree upon for a said price. I have been watching an ebay item a 7' Ammco that has been for sale for months, price now dropped to $2250 USD, still no takers.
https://www.ebay.com/itm/2567750728...qTKWCujHZZnIoA+hQvyhZlXfaA==|tkp:BFBM_PnpycVl
I think a realistic price for my machine is about $1500 CND and possibly $300CND for the Hard Maple stand/bench, possibly. Looking into what I have into the machine. I purchased the machine, incomplete for $200, Electrical $200, Nuts, bolts, hand wheels $200, Paint $120, Blast sand $70, Tool holder $35, Tools $65, Cover Fabric $40 and a whole bunch of time. I have in direct costs $865. Restorations, seldom benefit the person doing the work, yet there is passion in restoring something to live on for many more years and to be appreciated by many. I do enjoy the challenge.
So I will share a few links of other things that I have sunk a lot of money and time into that some day a long time from now may be worth something to someone else. ( Just not me )
My 1953 John Deere Model 40 Short Track Crawler. One of 2262 made. $15K invested ( 2001 )
My Son's 1985 1/2 Mazda RX7 Sports Car, $30K invested. (2012)
My nephew's 1982 Fiat X1/9 Turbo Engine Swap. He paid for the parts and material $10K and I did all of the labour. (2024)
500 Abarth 1.4 Turbo swap. | XWeb Forums
It has been the tools that I have acquired over the years that have allowed me to make any and all of this to happen.
I say, live, dream, work and watch it happen.
All the best.
TonyK.
Grimsby Ontario Canada.