"Once more unto the breach, dear friends, once more"
Time for an update. It takes such a large block of time (close to 20 hours straight) to do a casting that I can usually only one attempt in in a weekend. Something goes wrong, and wait until next week.
I also bought some silicone bronze ingots, trying to eliminate possibles sources of the issue, i.e. using mystery metal.
Still lots of flaws
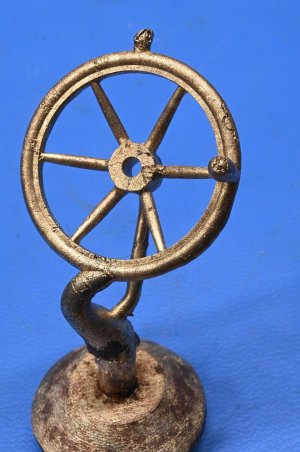
\
The one at the right, is the above cleaned up an few hours in the polisher. Better, but far too many flaws for this dog to drop the bone!
🙂
This has been brutally frustrating. I've a spent a small fortune on different castable resins and so far all are s**t. I think the issue is whatever the resin does on burnout is damaging the mold, but to be sure, i.e. isolate that, I decided to do a casting with a wax pattern instead of a resin pattern.
I fortunately have a vulcanizer and wax injector (when I bought the oven and vacuum caster it was a complete kit from a guy leaving the business) so it shouldn't be too big a deal, right?
The first thing is to make a mold to create the wax pattern, using the 3D resin printed part. As the part is somewhat fragile I elected to make the mold with RTV Silicone (that btw stands for room temp vulcanizing, no heat vulcanizing needed). That means pouring a liquid from using a press vulcanizer, far easier on the pattern.
First though, I need a casting box for the the silicone. 3D printer to the rescue
It did take me two tries, the first had too many air bubbles. The manufacture claims no vacuuming is necessary, but I found this highly optimistic. You might be able to dissipate them by vibration, hold something against the box, but have a vacuum made that easy
There are some tricks to cutting the mold in two. You need a set up like shown below, so you can pull the rubber apart to keep cutting inward. You also put in some curves so there is lots to register on.
This is just cutting a bit of excess material off, but shows the idea of its use
Ready to try. The wax is at 180-190F and under about 5psi of pressure (hand pump, black knob on the top right of the injector)
Injecting with the rubber in the 3D printed box shown below proved to be incorrect. Best to clamp between two steel plates - lets the vents work.
and try, and try and try
Everyone had some error on it. Incomplete, hollow sections, etc.
What went wrong? First issue I had was air entrapment. I learned how to cut vents in a mold.
The thing that kept nagging was how soft the mold was. It seems like I couldn't take advantage of the wax pressure without having to squeeze the mold together so tightly that it was badly distorted. Commercial RTV sold by jewellry supply places is listed at shore 36. The The RTV Silicone I bought, claimed on the amazon site it was Shore 30 (A scale). I figured it would work. This stuff is not cheap and clearly says its 30A
https://www.amazon.ca/gp/product/B09CYYB311/ref=ppx_yo_dt_b_search_asin_title?ie=UTF8&psc=1
I did have a few jewellers molds which seemed far stiffer than my RTV mold. But I says to meself, maybe the rubber is old and stiff?
Finally I couldn't take it any more and ordered A scale durometer. The $@#% $##$@%$^#@ #@)(^# stuff from Amazon is 7!! Despite being advertised at 30. The jewelers molds I had measure exactly 36.
The time wasted by that misrepresentation is really frustrating. Of to BC tomorrow for the weekend...when back I'll order some proper RTV from Gesswein and try again. If I get a good casting, I can carry on with this model.....we'll see if I have enough left in the tank to keep going back to the resin makers. It would be so nice to go from print to investment mold...but man, it is challenging!
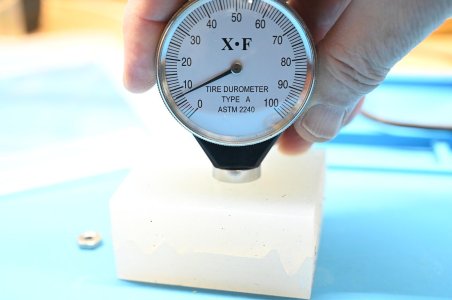