terry_g
Ultra Member
I replaced a fuel pump/filter module a couple days ago on an International Maxxforce 10 engine.
For some reason it was only making 30 Psi and it should be 100 Psi. I replaced the electric pump first with no change
so I then replaced the complete unit.
Yesterday I went and rescued it from the scrap metal bin. I put in the band saw and cut the pump housing off and
cleaned it up a bit in the mill. I plan on using it to fill a container for filling fuel filters on diesel engines.
I still need to make lines for it and a pair of leads with a momentary switch to power it.
The before and after pics.
This is what it looked like before the bandsaw.
The 1/8"NPT outlet is visible in the picture.
It uses a plastic quick connect fuel fitting on the inlet.
I am going to make a metal one for it.
For some reason it was only making 30 Psi and it should be 100 Psi. I replaced the electric pump first with no change
so I then replaced the complete unit.
Yesterday I went and rescued it from the scrap metal bin. I put in the band saw and cut the pump housing off and
cleaned it up a bit in the mill. I plan on using it to fill a container for filling fuel filters on diesel engines.
I still need to make lines for it and a pair of leads with a momentary switch to power it.
The before and after pics.
This is what it looked like before the bandsaw.
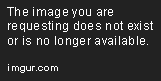
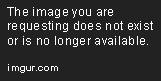
The 1/8"NPT outlet is visible in the picture.
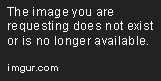
It uses a plastic quick connect fuel fitting on the inlet.
I am going to make a metal one for it.
