Brent H
Ultra Member
So, before I left for work last month - maybe about a week to go, my Bridgeport mill started to be quite difficult to raise or lower the spindle at about the top 1 to 1-1/2" of travel. It was stiff enough that the power feed no longer would work at the top. Everything was smooth as silk in the bottom 4 inches of travel. As I would work the handle it appeared to get a bit easier but was always sticking in that last bit of travel. I though maybe it was due to the spring return on the feed handle as I had taken that off and adjusted the spring tension. I opened up that part of the mill and there was a piece of felt material in the works - Eureka!! I exclaimed and pulled out this piece of crap, put it all back together and .......nope....crap!.....And away I went to work.....
Over the month I have been reading all kinds of things- piece of debris in the spindle area, lack of use (ya right - LOL) and a few other things that all talked about pulling things apart. I contacted the guy at H&W Machinery and asked if you can separate the top assembly (head and motor works) from the feed assembly without taking everything apart - he said yes!
So I took it apart as you can see and I found NOTHING........I took a few other things apart as well and it all came back negative.....I still had the tough last inch no matter what was removed. The spindle is amazingly chrome polished the steel sleeve at the top was all good, no debris, the felt strainer thing on top was good.........I left the shop, popped the top off a bottle of whiskey and that was that.......
Reading more on line and one guy says it could be the set screw at the back of the spindle that locks the bearing retaining nut in place. If it is too tight it will distort the spindle sleeve and cause binding.....WHAT?! no way......Ok says I - let us see. Well the set screw was not very tight
but I loosened it more anyways.....holy smokes........like butter....no more binding in the last inch or so and the feed works great 
Couple hours putting things all back together, re-tramming the vise and such and the mill is back in business. The "fit" on the spindle must be nothing short of exact as the screw is not very tight- I guess enough to keep things from coming apart but WOW.........
So ..... If you have a mill like mine and it is sticky in the last bit of feed - check out that F'n set screw.....I didn't adjust it or anything so I must have worked its self tighter? Anyway I also learned you can pull the mill power unit off pretty easy - I screwed some 2 x 8 blocks together for the head to sit on and cranked it over 90 to rest on the wood - I also supported the motor and took some weight off with the chain falls I use to lift the rotary table. 3 nuts off and the two parts will separate. I used the x axis feed to crank the head off and on - worked slick
Now on to other projects.........
Over the month I have been reading all kinds of things- piece of debris in the spindle area, lack of use (ya right - LOL) and a few other things that all talked about pulling things apart. I contacted the guy at H&W Machinery and asked if you can separate the top assembly (head and motor works) from the feed assembly without taking everything apart - he said yes!
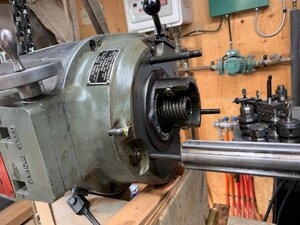
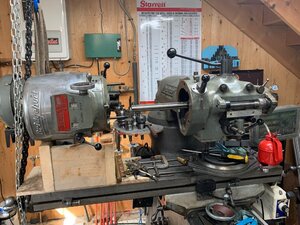

So I took it apart as you can see and I found NOTHING........I took a few other things apart as well and it all came back negative.....I still had the tough last inch no matter what was removed. The spindle is amazingly chrome polished the steel sleeve at the top was all good, no debris, the felt strainer thing on top was good.........I left the shop, popped the top off a bottle of whiskey and that was that.......
Reading more on line and one guy says it could be the set screw at the back of the spindle that locks the bearing retaining nut in place. If it is too tight it will distort the spindle sleeve and cause binding.....WHAT?! no way......Ok says I - let us see. Well the set screw was not very tight
Couple hours putting things all back together, re-tramming the vise and such and the mill is back in business. The "fit" on the spindle must be nothing short of exact as the screw is not very tight- I guess enough to keep things from coming apart but WOW.........
So ..... If you have a mill like mine and it is sticky in the last bit of feed - check out that F'n set screw.....I didn't adjust it or anything so I must have worked its self tighter? Anyway I also learned you can pull the mill power unit off pretty easy - I screwed some 2 x 8 blocks together for the head to sit on and cranked it over 90 to rest on the wood - I also supported the motor and took some weight off with the chain falls I use to lift the rotary table. 3 nuts off and the two parts will separate. I used the x axis feed to crank the head off and on - worked slick
Now on to other projects.........