Is it possible to turn rubber on a lathe with standard tools? I need to make some custom rubber grommets for a couple of holes I drilled through my truck wheel wells just behind the rocker panel. I had forgotten that the panels (AL in my F250 SuperDuty) would be double panels, so the grommets I used to use for previous trucks that were steel won't fit as the holes are too thick after step drilling. Realistically, I've de-burred them so well with a Dremel you can run your finger across them, so I could always use stainless cable wrap. But I want to do it right.
I've heard of products like Versimold https://www.amazon.ca/dp/B00NQ11AQI/ref=cm_sw_em_r_mt_dp_HIyZFb44J1YQS for grommet making, but also of people turning rubber with standard tools, sometimes with the aid of circuit chiller. Lots of YouTube vids for both. Another method apparently is to make a holder for your Dremel and turn them this way.
The rubber would have to be soft enough to get squeezed into the hole like a grommet, but hard enough to turn. If worse comes to worse I can always make it from acetal, then glue it into place (hey, that's not a bad idea
).
Has anyone tried this?
I've heard of products like Versimold https://www.amazon.ca/dp/B00NQ11AQI/ref=cm_sw_em_r_mt_dp_HIyZFb44J1YQS for grommet making, but also of people turning rubber with standard tools, sometimes with the aid of circuit chiller. Lots of YouTube vids for both. Another method apparently is to make a holder for your Dremel and turn them this way.
The rubber would have to be soft enough to get squeezed into the hole like a grommet, but hard enough to turn. If worse comes to worse I can always make it from acetal, then glue it into place (hey, that's not a bad idea
Has anyone tried this?
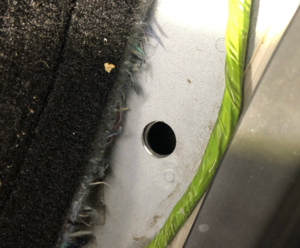