We got a used treadmill for cheap. It had some belt tracking issues and the elevation mechanism would not work. The tracking was solved by adjusting the rollers. The elevation was a different story...
I had just recently completed the rebuild of my 1948 Peerless Shaper (it was free - just had to get it) and it was the perfect little project for it: cut a gear rack. I used my Clarkson T&C grinder to grind a HSS form tool that matched to old broken rack and away we went. I just used cold rolled rectangular stock because I do not have a good way to heat treat steel yet. So I made two racks in one go - just in case. The original seems to be hardened where the gear teeth are. I think maybe too hard and that is why it broke in the first place?
Here is the shaper cutting the racks
And another shot
And the finished product
Here you can see the heat treating of the original part on the left, also the broken teeth. The pinion is driven through a reduction gearing system that is stationary and the rack is what moves the treadmill running surface to an inclined position
Six months later, and very regular use of the treadmill, has not resulted in a failure of the incline mechanism. I guess mild steel was strong enough.
I had just recently completed the rebuild of my 1948 Peerless Shaper (it was free - just had to get it) and it was the perfect little project for it: cut a gear rack. I used my Clarkson T&C grinder to grind a HSS form tool that matched to old broken rack and away we went. I just used cold rolled rectangular stock because I do not have a good way to heat treat steel yet. So I made two racks in one go - just in case. The original seems to be hardened where the gear teeth are. I think maybe too hard and that is why it broke in the first place?
Here is the shaper cutting the racks
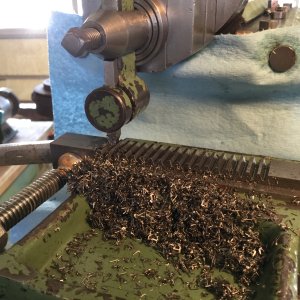
And another shot
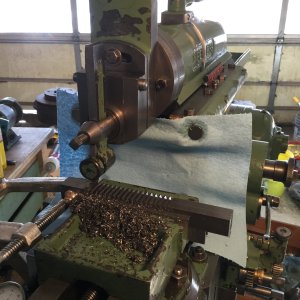
And the finished product
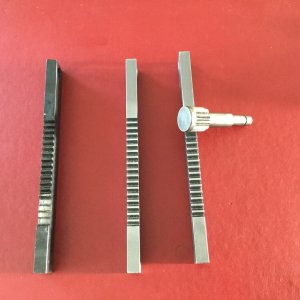
Here you can see the heat treating of the original part on the left, also the broken teeth. The pinion is driven through a reduction gearing system that is stationary and the rack is what moves the treadmill running surface to an inclined position
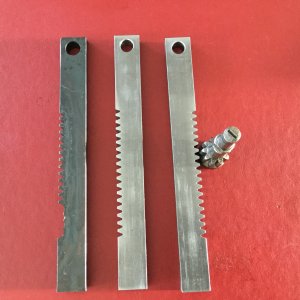
Six months later, and very regular use of the treadmill, has not resulted in a failure of the incline mechanism. I guess mild steel was strong enough.