slow-poke
Ultra Member
I'm now thinking about how I'm going to add CNC capability to the knee joint of my A1S mill.
I want to use a similar 2.4Nm continuous torque 7.2Nm peak ac servo, except this one has an integrated brake. I have a beefy double nut ballscrew waiting in the corner.
From my measurements and reading about knee conversions it seems I will need a 3:1 torque multiplication to be on the safe side. Aim is to have < 0.001" error, so driving through the bevel gears is not an option. There appears to be plenty of room to mount this servo just inside the front edge of the knee and then drive the new ballscrew via a suitable timing belt as shown in the concept drawing below. The servo moves with the knee and the upper end nub of the ballscrew simply pushes up against the existing bearing (more likely on a spacer that fits in the existing bearing).
Can anyone spot any obvious problems with this concept?
Suggestions for suitable timing belt that will accommodate about 20+ Nm of torque?
I want to use a similar 2.4Nm continuous torque 7.2Nm peak ac servo, except this one has an integrated brake. I have a beefy double nut ballscrew waiting in the corner.
From my measurements and reading about knee conversions it seems I will need a 3:1 torque multiplication to be on the safe side. Aim is to have < 0.001" error, so driving through the bevel gears is not an option. There appears to be plenty of room to mount this servo just inside the front edge of the knee and then drive the new ballscrew via a suitable timing belt as shown in the concept drawing below. The servo moves with the knee and the upper end nub of the ballscrew simply pushes up against the existing bearing (more likely on a spacer that fits in the existing bearing).
Can anyone spot any obvious problems with this concept?
Suggestions for suitable timing belt that will accommodate about 20+ Nm of torque?
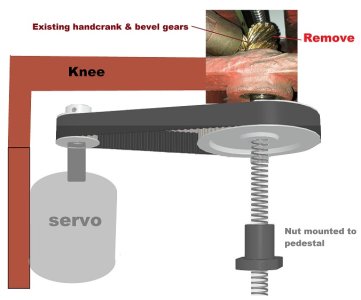
Last edited: