Janger asked for some pics of silver soldering drill extensions. I had a bunch to show, but didn't want to take the other thread so far OT
First example was making a new high precision spindle shaft for a mill - its close to a foot long. There is a way to drill long holes like this by first single point boring the hole say 1-2 the nominal diameter deep. The hole is then started perfectly. Now run a precision ground drill of the nominal size into the hole and cut just enough at the end to form a divot, that because its guided by the bore, will be perfectly concentric to the bore. then alternating between drill, reamer to nominal size, then use a nominal size drill to create a new starting centre at the end of the hole. Things stay true because over this short distance, the reamer is guided by the existing bore. Do this every 1/4" - 1/2 (depending on hole dia) or so and you can drill 20-30x the diameter and the hole comes out within a thou. As good as gun drilling with no special equipment. You need a precise grind on the drills, especially the nominal one used to keep establishing the starting diviot. I use a T&CG to sharpen them or use new high quality drills.
Note the wet rag as a heat sink when brazing the drill. SS is easy, clean, lots or flux and mostly try and get the heat there indirectly. I use air/propane most of the time (yes its more than hot enough) but on large pieces use the higher heat output of O/A - then you must definitely apply heat indirectly (propane air is easier and more forgiving). Not so much here because appearance didn't matter to me, but most of the time when SS'ing I use the technique Kozo Hiraoka covered so well in Live Steam so long ago. Clip little pieces of 1/16 dia SS, place them in the flux with tweezers and warm the two pieces up until it neatly wicks in. Neatest joints possible with no excessive SS blobs
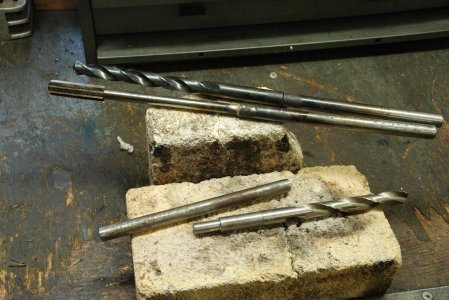
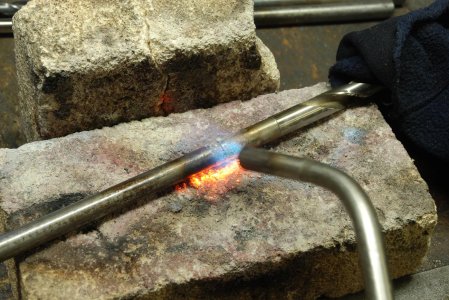
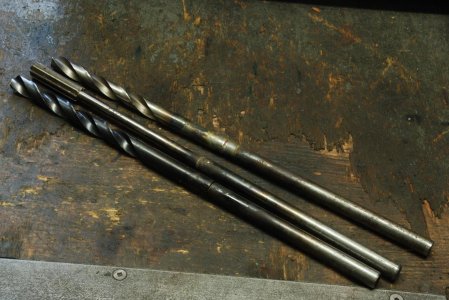
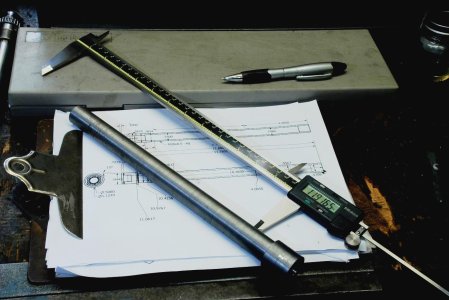

then to the grinder
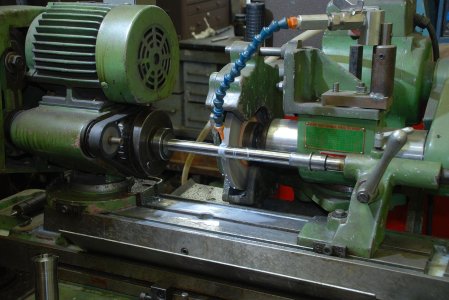
Second example is a 1/8 hole through 4" of cast iron - it ends up being the relief in the corner of a dovetail. Those drills/reamers were soldered with a butt joint and worked fine. In the first photo, the brass shim is there to keep the small diameter extension concentric with the reamer
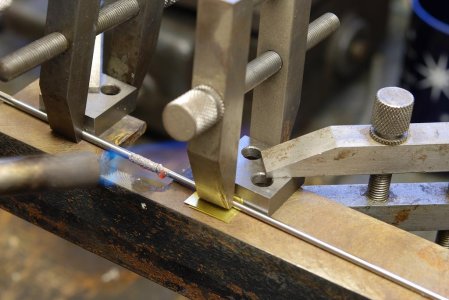
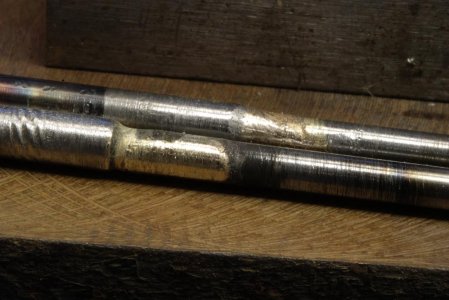
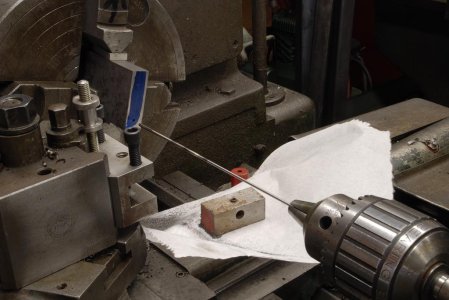
30x the dia and its within 2 thou end to end
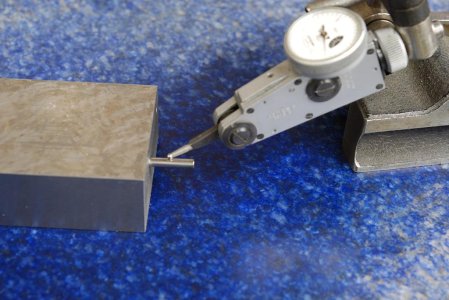
First example was making a new high precision spindle shaft for a mill - its close to a foot long. There is a way to drill long holes like this by first single point boring the hole say 1-2 the nominal diameter deep. The hole is then started perfectly. Now run a precision ground drill of the nominal size into the hole and cut just enough at the end to form a divot, that because its guided by the bore, will be perfectly concentric to the bore. then alternating between drill, reamer to nominal size, then use a nominal size drill to create a new starting centre at the end of the hole. Things stay true because over this short distance, the reamer is guided by the existing bore. Do this every 1/4" - 1/2 (depending on hole dia) or so and you can drill 20-30x the diameter and the hole comes out within a thou. As good as gun drilling with no special equipment. You need a precise grind on the drills, especially the nominal one used to keep establishing the starting diviot. I use a T&CG to sharpen them or use new high quality drills.
Note the wet rag as a heat sink when brazing the drill. SS is easy, clean, lots or flux and mostly try and get the heat there indirectly. I use air/propane most of the time (yes its more than hot enough) but on large pieces use the higher heat output of O/A - then you must definitely apply heat indirectly (propane air is easier and more forgiving). Not so much here because appearance didn't matter to me, but most of the time when SS'ing I use the technique Kozo Hiraoka covered so well in Live Steam so long ago. Clip little pieces of 1/16 dia SS, place them in the flux with tweezers and warm the two pieces up until it neatly wicks in. Neatest joints possible with no excessive SS blobs
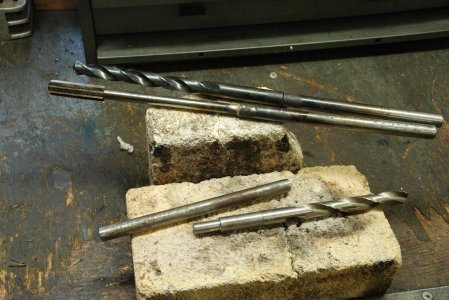
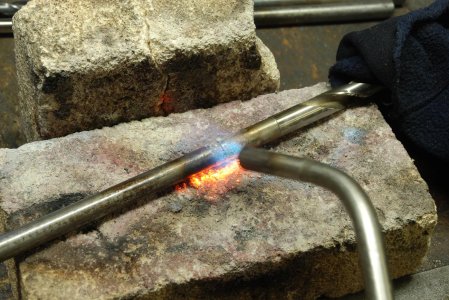
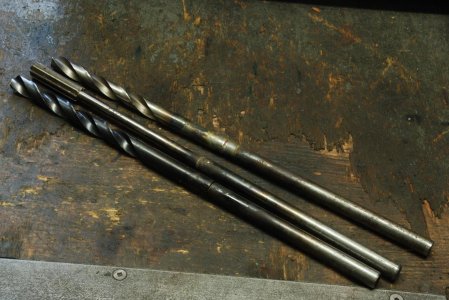
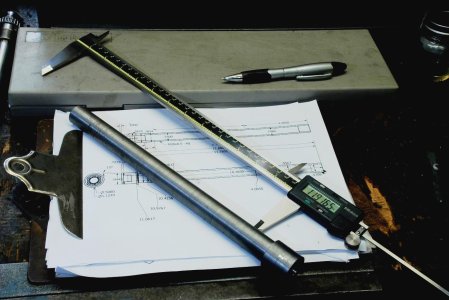

then to the grinder
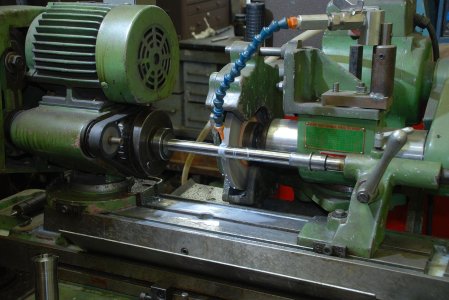
Second example is a 1/8 hole through 4" of cast iron - it ends up being the relief in the corner of a dovetail. Those drills/reamers were soldered with a butt joint and worked fine. In the first photo, the brass shim is there to keep the small diameter extension concentric with the reamer
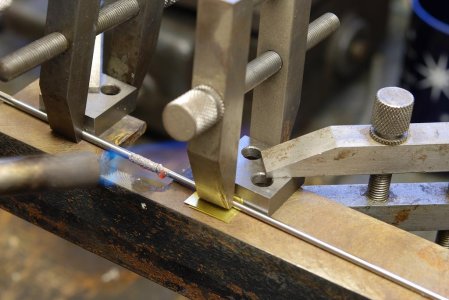
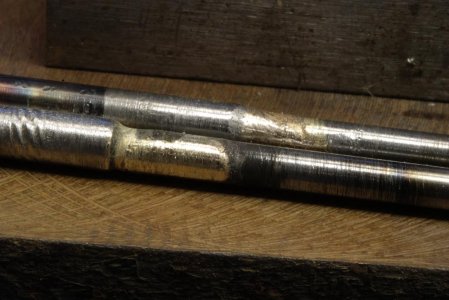
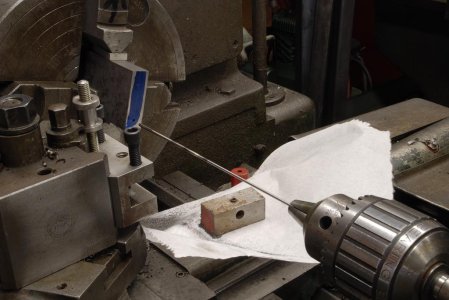
30x the dia and its within 2 thou end to end
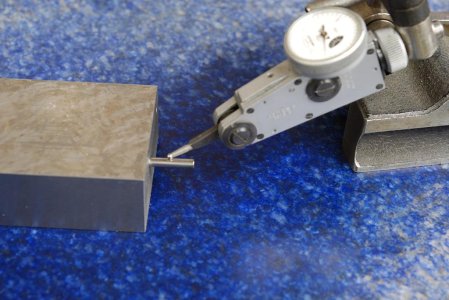
Last edited: