I started building the head alignment guide for my RF mill today.
This is inspired by an excellent idea and execution over on Hobby-Machinist.com
RF-30 Clone Head Alignment Guide
https://r.tapatalk.com/shareLink/to...ent-Guide.84270/&share_type=t&link_source=app
I sourced a piece of 6” diameter 6061 yesterday and today I faced both sides in the 4-jaw.
I hoped to bore it out but got too cold and hungry [emoji39]
Sent from my iPhone using Tapatalk
This is inspired by an excellent idea and execution over on Hobby-Machinist.com
RF-30 Clone Head Alignment Guide
https://r.tapatalk.com/shareLink/to...ent-Guide.84270/&share_type=t&link_source=app
I sourced a piece of 6” diameter 6061 yesterday and today I faced both sides in the 4-jaw.
I hoped to bore it out but got too cold and hungry [emoji39]
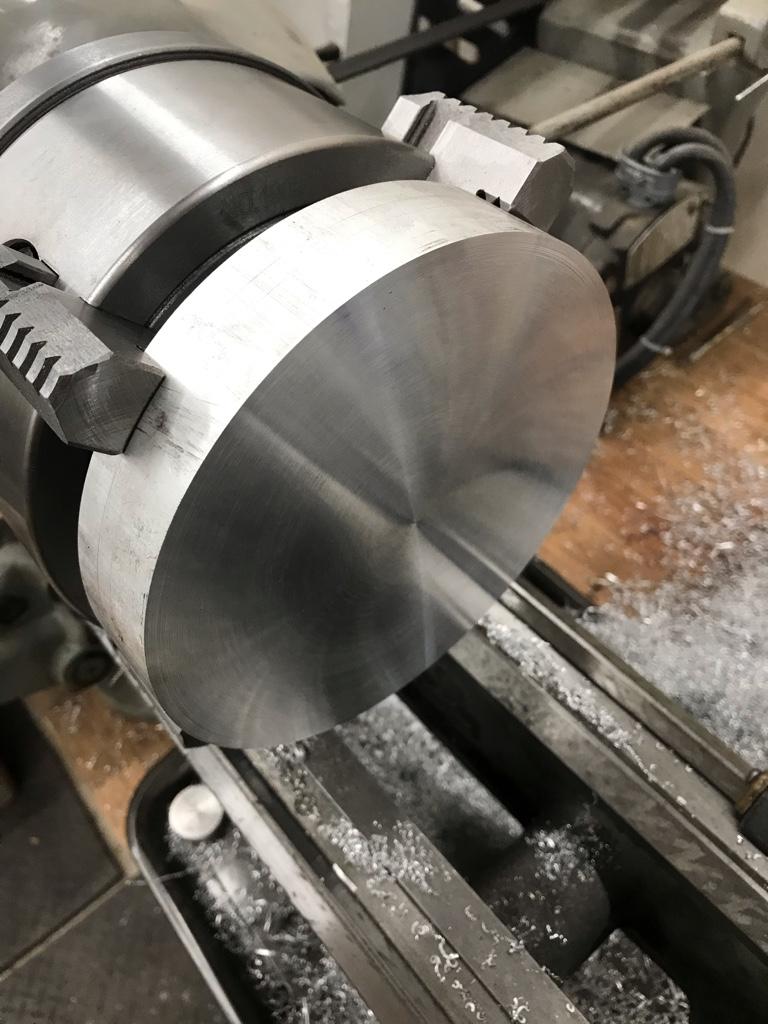
Sent from my iPhone using Tapatalk