I half considered doing something like this, so I'm curious......
How long have you been using this setup?
Have you tried running the inverters at full load or near full load for an extended time?
How long will the batteries hold up with light load say 400W?
Heavy load?
Do the inverters connect to dedicated wiring or a couple of the original circuits that were originally connected to your breaker box?
Any failures?
Some inverters are pretty iffy, I connected a Canadian Tire brand to an isolated circuit in my garage and it promptly let go with a good puff of electronic smoke.
Thanks
The initial project started in 2012 with AGM batteries, an ELCON charger, xMU control module and a PLC (not in photos) running things.
Underneath there is a large 105V power supply (now in my CNC mill) and beside that the Solar Panel Controller. The smaller red top battery is the genset starting battery.
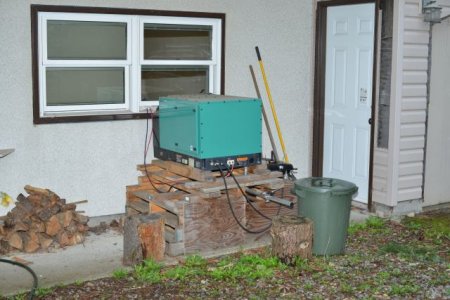
The problem with AGM batteries is that you shouldn't discharge them past 50% SOC and after the initial bulk charge it takes forever to bring them up to 100% SOC so the diesel 30kW (115VAC, not 220VAC with center tap) ONAN generator would often carbon up. The white module TMU (Tray Management Unit) was the main control system and that talked to the PLC or a PC while the 5 CAN bus channels and relay outputs switch inputs would control various things. The gold box series (xIM) for eXtendable Interface Modules were configured as a GIM (Generator Interface module) and BIM (Battery Interface Module).
The GIM would start and stop the generator and read the flashing light fault codes and report them over CAN bus to the PMU which reported them to the rest of the system. The BIM handled all the battery charging and monitoring SOC to know when to start the generator.
We later upgraded from the ELCON 80A 28V chargers to 3 DeltaQ 650W chargers. The ELCON used CAN J1939 while the DeltaQ used CANopen. We weren't allowed to change the main software because that would require full testing and certification so instead I built a small J1939 to CANOpen translator emulating the ELCON chargers. Main software didn't require a change.
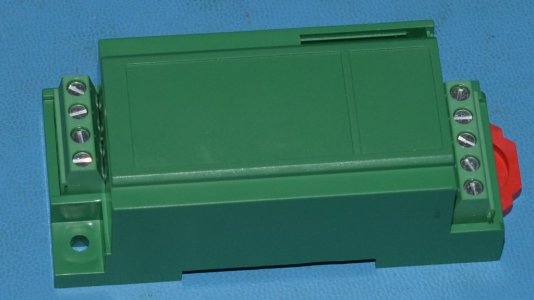
Then we upgraded to Valence brand Lithium and now the Valence BMS handles the batteries but we still used the original software in the TMU which had a back door so it could operate stand alone without a PLC running things.
I ended up with the now used test set batteries since then they later upgraded to 24V units instead of 12V units in series.
Now to answer the questions. I no longer have the generator. The inverters were going to be trashed because they had dropout fault issues when the battery voltage dropped below a certain point. We actually added 24V to 24V DC power supplies to ensure that AGM battery 21V to 28V wouldn't cause the inverters to drop out. Again the lithiums solved those problems but we no longer used those inverters so I have 3.
At 28V a 1000W inverter draws 35A. I've never have run them at that output because the wires to them would probably melt. I just run a few lamps, Router, Shaw cable TV etc.
On a power failure which here never lasts more than a few hours I run extension cords to stuff upstairs. I don't have a transfer switch or dedicated circuits although I'm starting to want that for the Furnace (Nat Gas), Freezer and Fridge. So small breaker box for those three and maybe a lamp or two running continuously off the inverters which run off the DeltaQs which run off AC.
However none of those items actually need a full time AC UPS system. So a transfer switch and switch the inverters from AC line might be the better solution.
Lithium batteries can be taken down to about 5% SOC and they are 120AH batteries so I have 240AH at 24V or about 215AH from full charge. Drawing 400W is 17A which means about 12 hours before a generator would have to be started.
I have no knowledge of what the application load was for these projects since that was beyond my security rating.
The reason I first got this project is because my TMU, for 3 trays with CANJ1939, CANopen for external communications and the relay control was originally an RMU (Rings Management Unit). Two were used in this project; one for starboard and one for the port side of the barge.
Anyway this is a 24V system so I don't think PA or CdnTire even carry those kinds of inverters. One has to go to the Solar Charging suppliers for that sort of thing.