SparWeb
Active Member
Hi
I got this set up on my lathe and just questioning what else I should do to make it work. Photo below.
I'm doing this crazy set-up because I don't have a milling machine.
In the lathe chuck is an end mill that I will use to mill a flat on the bar that's on the cross-slide.
I'm using the boring-bar holder on the QCTP to hold a round bar of the same diameter.
The end is sticking out so that I can mill a flat on it.
Then I will rotate the round bar, tighten again, to mill another flat. I am making 3 flats on this rod.
I am going to mill a fairly long flat at each position, although honestly I only need it to be long enough to grip in the chuck of a power drill.
I have the measurement tools I need to make the flats 60 degrees from each other.
I guess I don't believe this is rigid enough - any suggestions will be welcome!
This is the lat step I need to do for this drill guide project. I made a quick-and-dirty drill guide last year and found it quite useful. However it was terribly jiggly. This is my attempt to make a much more sturdy drill guide.
Given the overhang, I plan to cut rather slowly with the 1/2" end mill, and keep the feed rate and depth of cut shallow, too. Have to bear in mind that (unlike milling) the feed rate is proportional to the chuck speed. I will start at 400 RPM and maybe edge it up to 600 RPM for finishing passes, when the feed rate is as slow as this lathe can go (112 tpi). At that speed I think it will take 30 seconds to complete a single 2-inch pass!
Is there anything I can do to make the setup more rigid? Can you think of a way to use the tailstock for support?
Or is there something better that's totally different?
(Aside from buying a milling machine, of course!)
I got this set up on my lathe and just questioning what else I should do to make it work. Photo below.
I'm doing this crazy set-up because I don't have a milling machine.
In the lathe chuck is an end mill that I will use to mill a flat on the bar that's on the cross-slide.
I'm using the boring-bar holder on the QCTP to hold a round bar of the same diameter.
The end is sticking out so that I can mill a flat on it.
Then I will rotate the round bar, tighten again, to mill another flat. I am making 3 flats on this rod.
I am going to mill a fairly long flat at each position, although honestly I only need it to be long enough to grip in the chuck of a power drill.
I have the measurement tools I need to make the flats 60 degrees from each other.
I guess I don't believe this is rigid enough - any suggestions will be welcome!
This is the lat step I need to do for this drill guide project. I made a quick-and-dirty drill guide last year and found it quite useful. However it was terribly jiggly. This is my attempt to make a much more sturdy drill guide.
Given the overhang, I plan to cut rather slowly with the 1/2" end mill, and keep the feed rate and depth of cut shallow, too. Have to bear in mind that (unlike milling) the feed rate is proportional to the chuck speed. I will start at 400 RPM and maybe edge it up to 600 RPM for finishing passes, when the feed rate is as slow as this lathe can go (112 tpi). At that speed I think it will take 30 seconds to complete a single 2-inch pass!
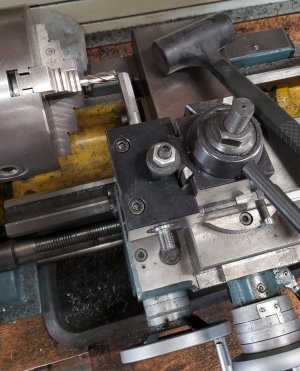
Is there anything I can do to make the setup more rigid? Can you think of a way to use the tailstock for support?
Or is there something better that's totally different?
(Aside from buying a milling machine, of course!)