slow-poke
Ultra Member
Well I made a little discovery on the A1S mill just now, hope others can comment on what I discovered.
This relates to this thread, but I don't want to sidetrack that thread so I'm starting a new one.
canadianhobbymetalworkers.com
I'm attempting to take fairly accurate measurements of the X axis saddle particularly around the leadscrew nut because a 20mm balllscrew upgrade is going to be very tight.
I'm not sure if what I found is just the way these are manufactured or if this is particularly sloppy. I would expect the bronze nut to be placed more or less perfectly centered. Clearly the mounting hole for the nut is offset by about 5mm to the right. Further the threaded hole in the bronze nut is further offset to the right by about another 3mm!
My first thought was that they goofed when they drilled the hole in the saddle and offset the hole in the nut to compensate, except the offset in the nut is in the wrong direction, second thought was they goofed again and put the nut on backwards, so I flipped it around to see if it partially corrected the offset, no almost the same, under closer examination the hole through the nut is quite angled to compensate for the offset.
So my best guess is they just bolt the nut on there any which way and then drill and tap it in place probably with some sort of jig fixed on the end cap.
Seems sloppy?
Comments please.
This relates to this thread, but I don't want to sidetrack that thread so I'm starting a new one.
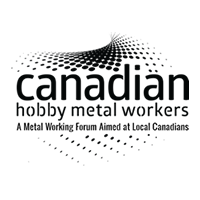
Ballscrew mounting block - expertise please
This question is related to this thread... https://canadianhobbymetalworkers.com/threads/8x30-a1s-mill-ball-screw-upgrade.9143/#post-131249 I'm starting a new thread specific to the mounting block for the X axis for clarity. This appears to be a typical engineering tradeoff scenario. First a...
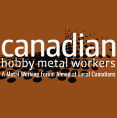
I'm attempting to take fairly accurate measurements of the X axis saddle particularly around the leadscrew nut because a 20mm balllscrew upgrade is going to be very tight.
I'm not sure if what I found is just the way these are manufactured or if this is particularly sloppy. I would expect the bronze nut to be placed more or less perfectly centered. Clearly the mounting hole for the nut is offset by about 5mm to the right. Further the threaded hole in the bronze nut is further offset to the right by about another 3mm!
My first thought was that they goofed when they drilled the hole in the saddle and offset the hole in the nut to compensate, except the offset in the nut is in the wrong direction, second thought was they goofed again and put the nut on backwards, so I flipped it around to see if it partially corrected the offset, no almost the same, under closer examination the hole through the nut is quite angled to compensate for the offset.
So my best guess is they just bolt the nut on there any which way and then drill and tap it in place probably with some sort of jig fixed on the end cap.
Seems sloppy?
Comments please.