I have no experience cutting gears but I do want to try and cut a new gear in aluminum.
I recently picked up an Atlas MFB in very good shape and I have a couple sets of gear cutters, one set is an M1 metric module and the other a DP 16.
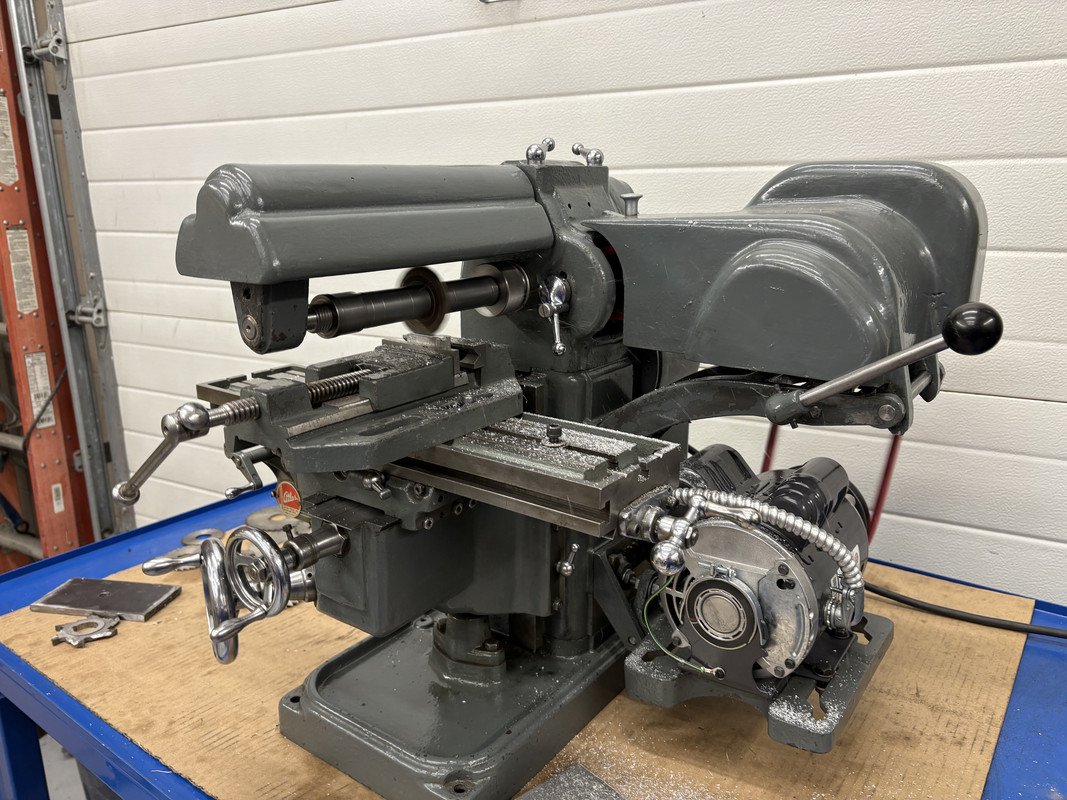
The gear I want to replicate is stamped M1.5 and Z25, o assume this to mean it is a metric gear of 1.5 module and 25 teeth.
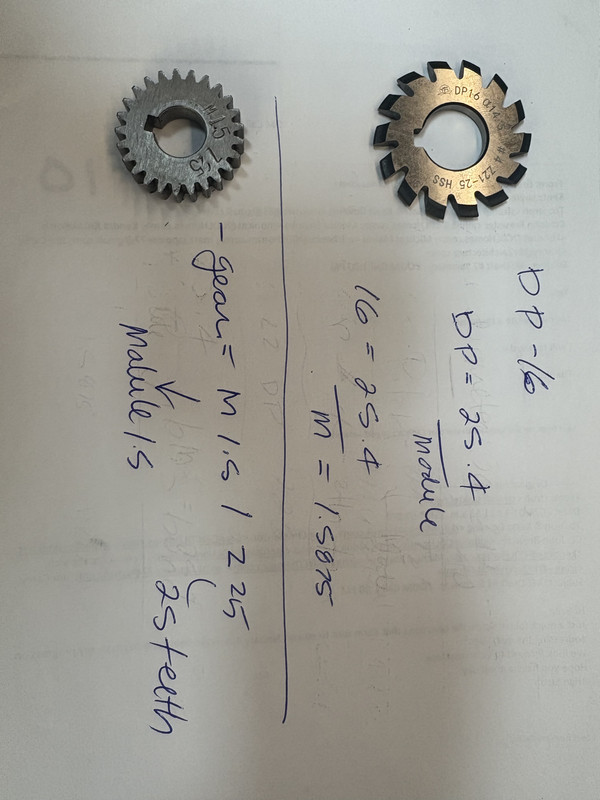
Consulting YouTube university I found a video explaining g how to convert metric module to diametric pitch.
If I divide 25.4 by the diametric pitch of 16 I get a module of 1.587, I assume the closest DP to a module of 1.587 is a diametric pitch of 16?
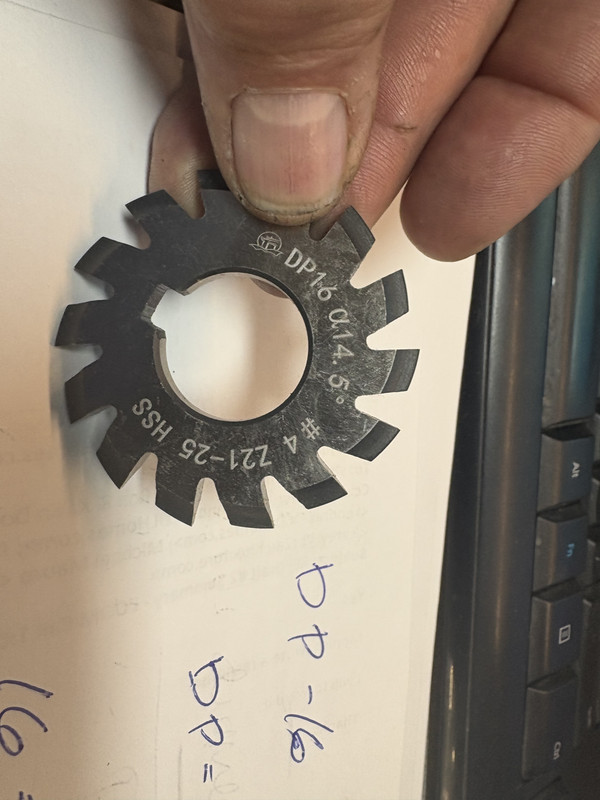
The DP 16 cutter for the 25 tooth gear is the one pictured above,
What are the numerals after DP16?? It looks like 14.5 degrees, do I need to be concerned about these markings?
YouTube says if I know the number of teeth, the diameter of the gear blank and the DP every thing I need can be figured out from there, I assume the critical info I don’t have is the depth of cut??
I have a Vevor dividing head to index the gear blank on
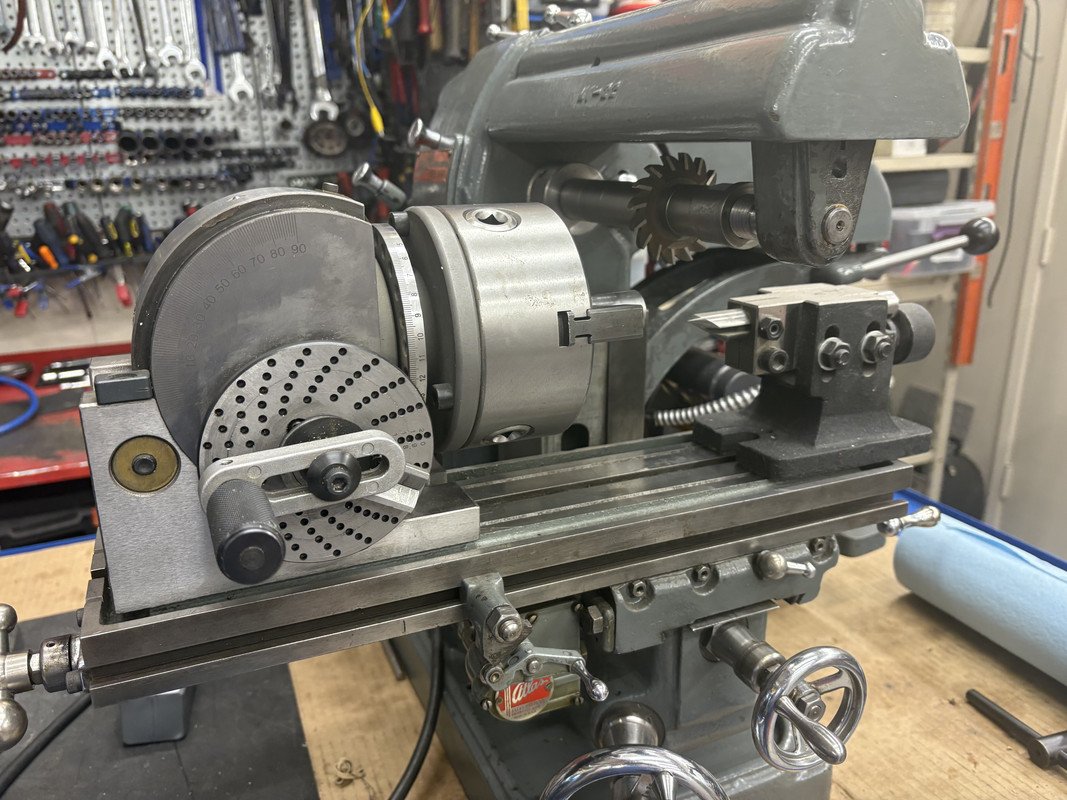
Looks like I need to make up a heavy steel plate to secure to the table to mount the dividing head and tail stock with an arbour mounted between centers, gear blank secured on arbour with sufficient clearance for the table to travel and clear the dividing head, sort of fashioned on the index accessory that Atlas sold as an option.
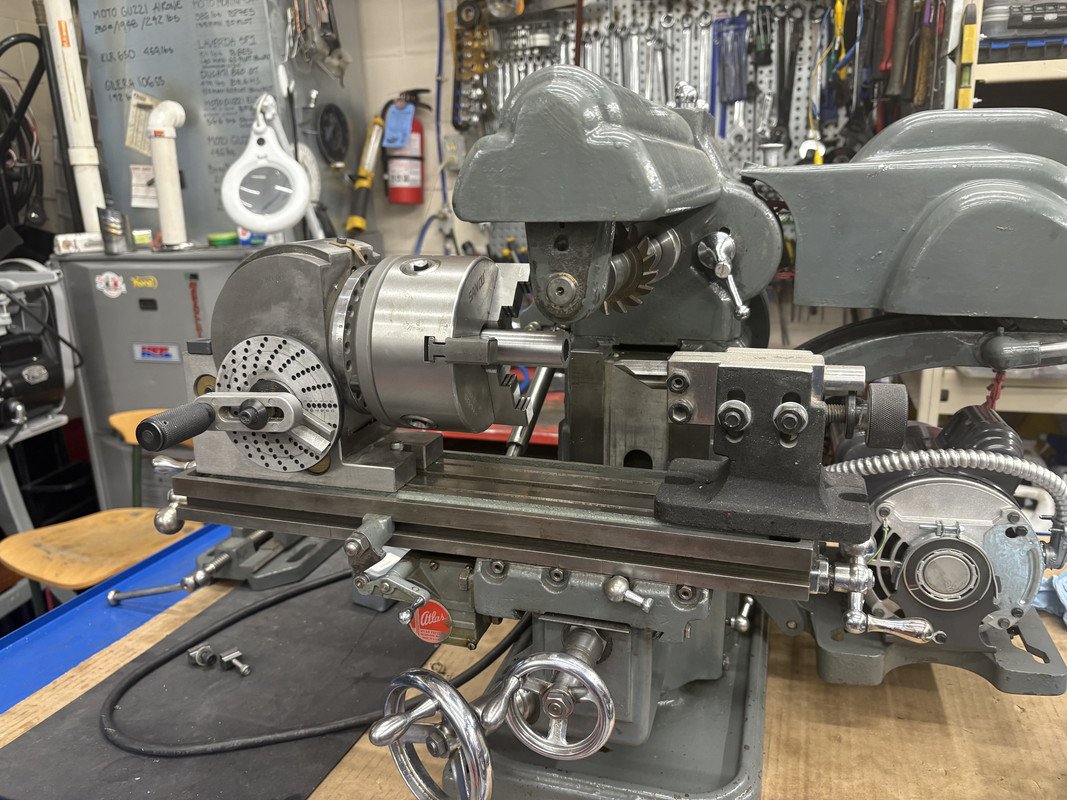
Any guidance into this new to me adventure is very much appreciated.
Thanks
Jim
I recently picked up an Atlas MFB in very good shape and I have a couple sets of gear cutters, one set is an M1 metric module and the other a DP 16.
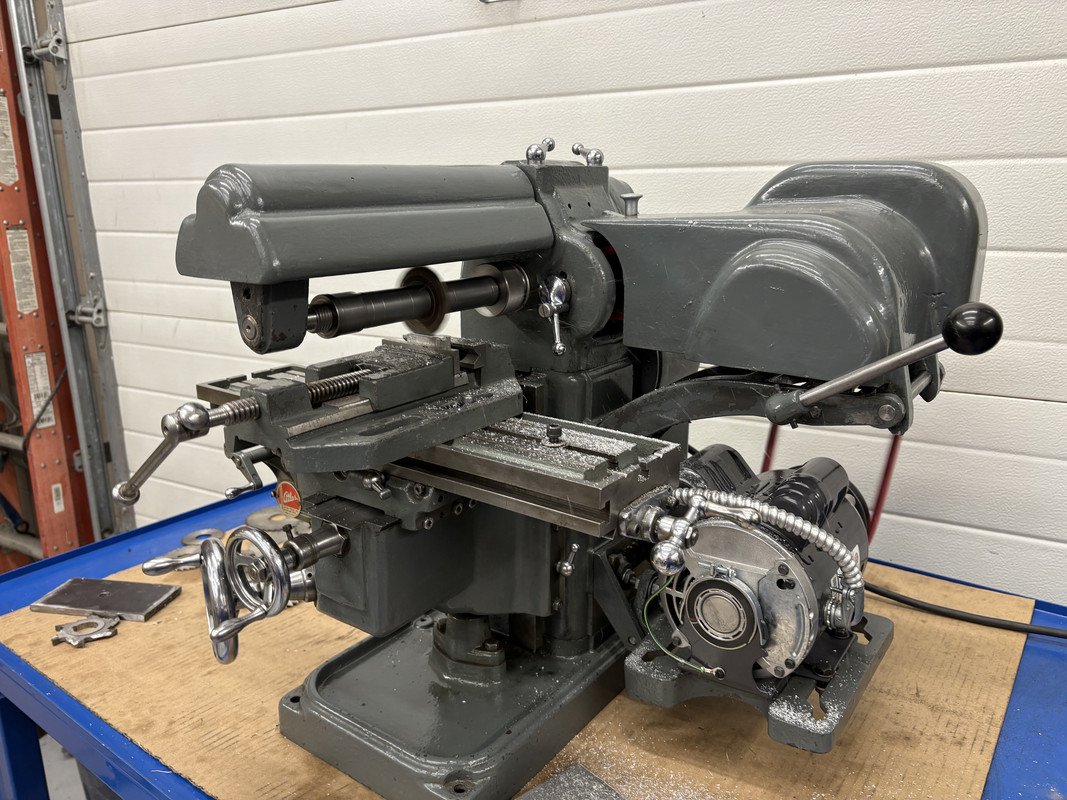
The gear I want to replicate is stamped M1.5 and Z25, o assume this to mean it is a metric gear of 1.5 module and 25 teeth.
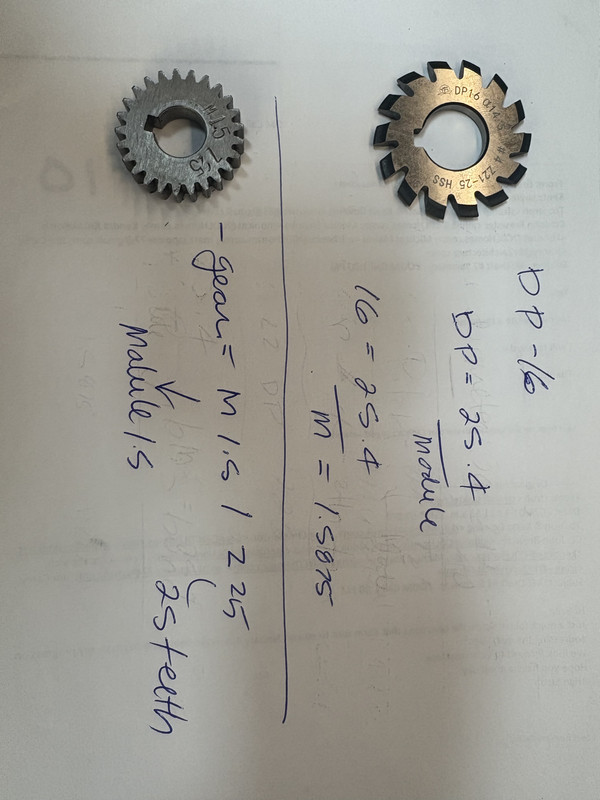
Consulting YouTube university I found a video explaining g how to convert metric module to diametric pitch.
If I divide 25.4 by the diametric pitch of 16 I get a module of 1.587, I assume the closest DP to a module of 1.587 is a diametric pitch of 16?
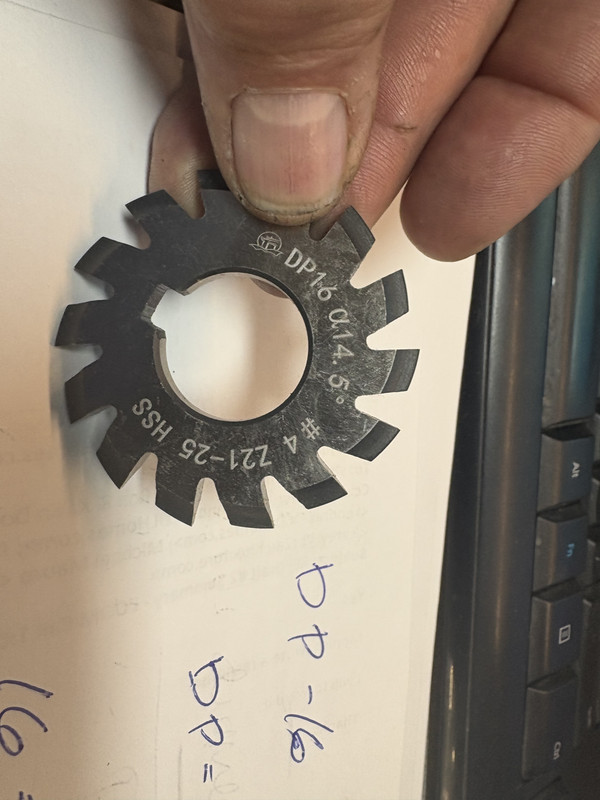
The DP 16 cutter for the 25 tooth gear is the one pictured above,
What are the numerals after DP16?? It looks like 14.5 degrees, do I need to be concerned about these markings?
YouTube says if I know the number of teeth, the diameter of the gear blank and the DP every thing I need can be figured out from there, I assume the critical info I don’t have is the depth of cut??
I have a Vevor dividing head to index the gear blank on
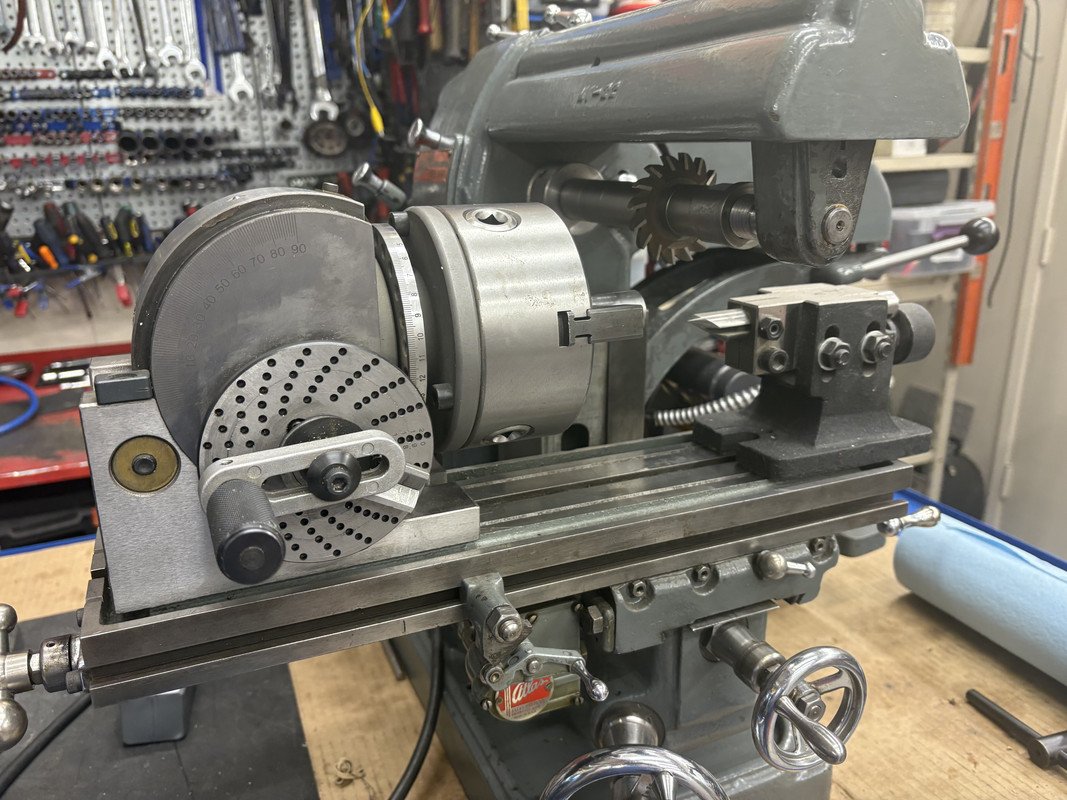
Looks like I need to make up a heavy steel plate to secure to the table to mount the dividing head and tail stock with an arbour mounted between centers, gear blank secured on arbour with sufficient clearance for the table to travel and clear the dividing head, sort of fashioned on the index accessory that Atlas sold as an option.
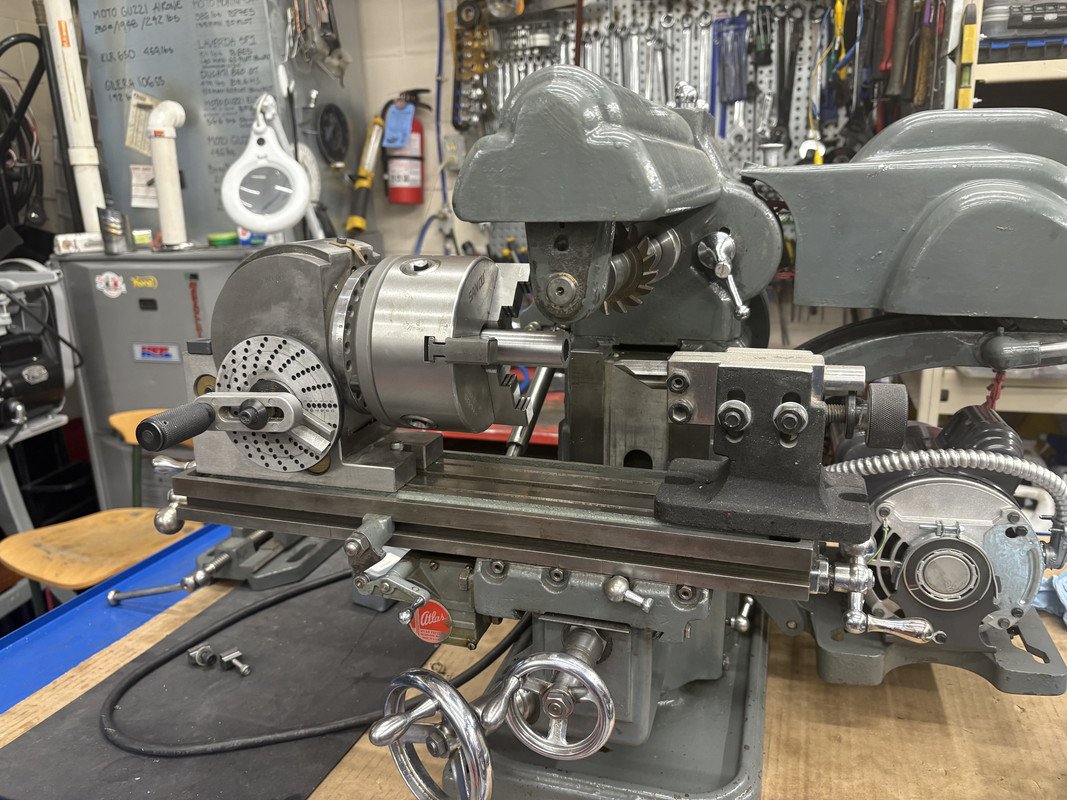
Any guidance into this new to me adventure is very much appreciated.
Thanks
Jim