https://www.canadianmetalworking-di.../MobilePagedReplica.action?pm=2&folio=48#pg48
You might have to register view the article. It's about making moulds for food containers.
I note a couple things - look at how beefy this mold is. I'm guessing each side is 8" thick? Wow.
Second the tolerance is apparently 5 microns or 2 tenths for this kind of work. It is for food containers. Anybody work on this sort of thing? What would the cycle time be for a set of containers when the mould is in use? Maybe they are for cream cheese or dips? How much would a mould like this cost?
Here is a picture from the article - go read it! it's interesting. I hope the publisher is ok with reproducing this along with the plug to go read the article.
You might have to register view the article. It's about making moulds for food containers.
I note a couple things - look at how beefy this mold is. I'm guessing each side is 8" thick? Wow.
Second the tolerance is apparently 5 microns or 2 tenths for this kind of work. It is for food containers. Anybody work on this sort of thing? What would the cycle time be for a set of containers when the mould is in use? Maybe they are for cream cheese or dips? How much would a mould like this cost?
Here is a picture from the article - go read it! it's interesting. I hope the publisher is ok with reproducing this along with the plug to go read the article.
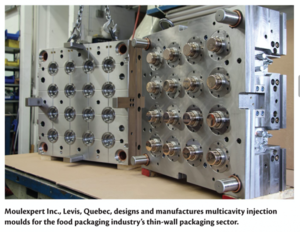