Apparently, the dual counter - rotating propellers on a Volvo Outboard Drive system requires a special socket. The tool costs a King's ransom.
So one of my boys borrowed one and asked me if I can make one for him. For reference, the ID is 2.05", and its about 7 inches long. I don't know if the OD (2.38") is critical but suspect that it is. It might have to fit inside a prop.
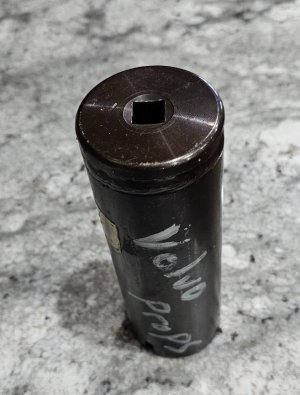
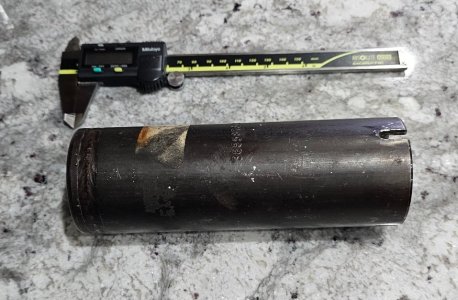
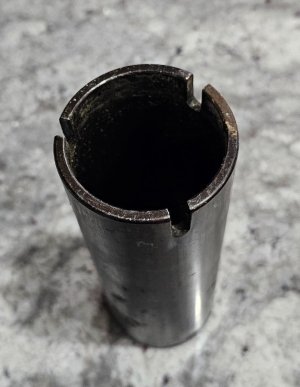
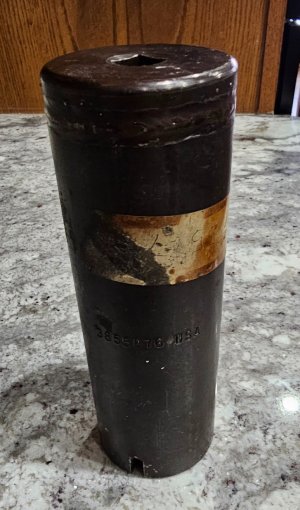
The socket part is easy. A 1/4" endmill will cut the slots. And if I can't find the perfect size thick wall pipe, turning the OD and boring the ID should be a piece of cake. In fact, if steel stock wasn't so expensive I'd just turn and bore the whole thing out of solid steel bar. But thick wall pipe is prolly cheaper.
My question to the gang is how to make the 1/2 (or maybe 3/4) square drive hole. Normally, I'd drill for the ID of the drive, then use a small endmill to rough out the square, and then file to dimension.
But I have a shaper coming some day soon and this seems like a great first project for it. What do the shaper guys on here think? How would you do this using a shaper?
So one of my boys borrowed one and asked me if I can make one for him. For reference, the ID is 2.05", and its about 7 inches long. I don't know if the OD (2.38") is critical but suspect that it is. It might have to fit inside a prop.
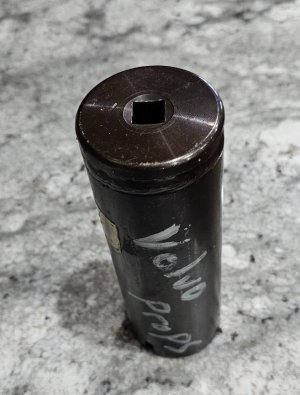
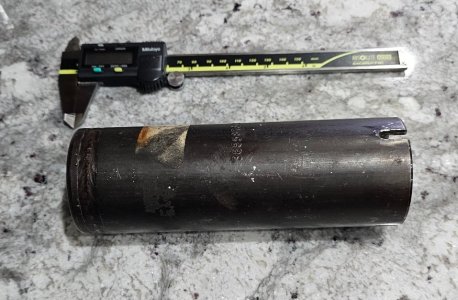
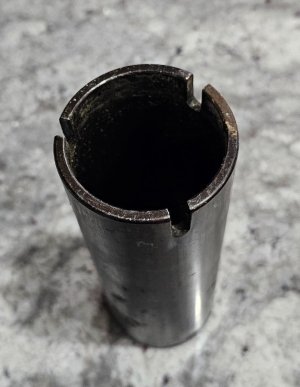
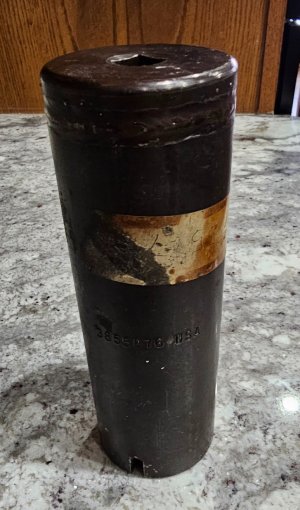
The socket part is easy. A 1/4" endmill will cut the slots. And if I can't find the perfect size thick wall pipe, turning the OD and boring the ID should be a piece of cake. In fact, if steel stock wasn't so expensive I'd just turn and bore the whole thing out of solid steel bar. But thick wall pipe is prolly cheaper.
My question to the gang is how to make the 1/2 (or maybe 3/4) square drive hole. Normally, I'd drill for the ID of the drive, then use a small endmill to rough out the square, and then file to dimension.
But I have a shaper coming some day soon and this seems like a great first project for it. What do the shaper guys on here think? How would you do this using a shaper?