I've been quiet for the last while. Life has a bad habit of getting in the way. With the youngest launched into first year university, the wife recovering from a mental health episode, and my dominant hand recovered enough from spring surgery that I can use it, this middle aged man's thoughts turn to the shop.
A couple weeks ago, I was perusing Kijiji, as I am wont to do. I found an ad, minimal bad pictures, no real details for what looks to be a bench lathe. A couple days of discussion with the clueless owner indicated that it had been his father's who had passed away last year and he was cleaning out the garage. So I take a chance, load the shop crane, block and tackle, ramps and straps on the truck and strike out across the Renous highway. The end result was me picking up a South Bend 9" horizontal drive lathe with a 4 1/2 foot bed and the seriously heavy home made stand. I did pay more for the lathe than I did the fuel in the truck to get there and back, but not by much I don't think. 20 year old Ford 3/4 ton is thirsty!
I did not hear or see the lathe run, one look at the rotted power cord and there was NO way I wanted anything to do with powering it up. The whole thing is absolutely caked in some kind of black crap that turns you the same colour if you get too close to it. Loading this was an adventure. Anyway, got it home a couple weeks ago and it's where it landed.
So here's what I observed.
- There is wear on the ways but I've seen a lot worse.
- The quick change gearbox shifts with difficulty through all the settings but they all appear to work.
- The original clamp for the tail stock is gone and someone kludged together one that works by welding a bolt to a piece of plate.
- The back gear shaft was taken off at one point and put back together wrong, i.e. the cams are out of phase so it's stuck
- Looks like someone HAMMERED on the shaft to get it to go together (square peg/round hole comes to mind)
- Still with the back gear, someone tried to drive a tapered pin through from the small side.
- The piece de resistance here, since the back gears are cocked off crooked, someone managed to smash at least six teeth from the small end gear and possibly at the same time broke one of the bull gear teeth.
The plan is to clean the crap off it in pieces until I can get the machine reassembled in my basement. Metalworking in an unheated garage is no fun from about December to April.
So tonight was step one. No real before photos since I was covered in diesel trying to scrub the crap off the counter shaft assembly. Here are some after pics.
Doesn't look so bad here.
I really am glad I didn't meet the previous operator.
I forgot to clean the shaft collar so that gives you some idea of how much crap is caked on.
That doesn't look right.
Nor does this on he other side...
I understand re-sleaving it, but for the material cost and effort, make it go all the way through!
Can't say anything about this, my skill is probably worse. I'll go at this with a file.
Well, that's not right.....
Know why they resleaved it. That's +0.025" tolerance!
Other side looks closer to 7/8"
Got to take up the slack somehow.
That's not 7/8ths!
Doesn't matter how big your bench is.....
When the time comes, I don't think I'm going to bother farting around with this fire starter/electrocution device.
110/220. That wasn't yesterday.
Yeah, no.
Yetch!
And finally, this really rots my socks. How much does a piece of key stock cost?
So this ought to be an interesting project. First off I think I'll bore those clapped out journals out and make some proper oil bronze inserts. I know there's supposed to be a wick there but a nice close fitting oil bronze bushing with a nice smooth shaft will go a long way to improving things. And I plan on drilling out the oil hole into the bushing.
God alone knows what other interesting things I'll find as I tear into it. Best case I have a usable lathe at the end of the day and I learn a lot. Worst case, I clean up and sell usable bits and pieces to recoup cost, scrap the rest and I've still learned a lot. I'll be working on this as time, ambition and other projects and chores allow so updates will be catch as catch can.
Please feel free to join in with a heartfelt round of "What in the hell were they THINKING?" I'm sure that among other things will be said quite often.
A couple weeks ago, I was perusing Kijiji, as I am wont to do. I found an ad, minimal bad pictures, no real details for what looks to be a bench lathe. A couple days of discussion with the clueless owner indicated that it had been his father's who had passed away last year and he was cleaning out the garage. So I take a chance, load the shop crane, block and tackle, ramps and straps on the truck and strike out across the Renous highway. The end result was me picking up a South Bend 9" horizontal drive lathe with a 4 1/2 foot bed and the seriously heavy home made stand. I did pay more for the lathe than I did the fuel in the truck to get there and back, but not by much I don't think. 20 year old Ford 3/4 ton is thirsty!
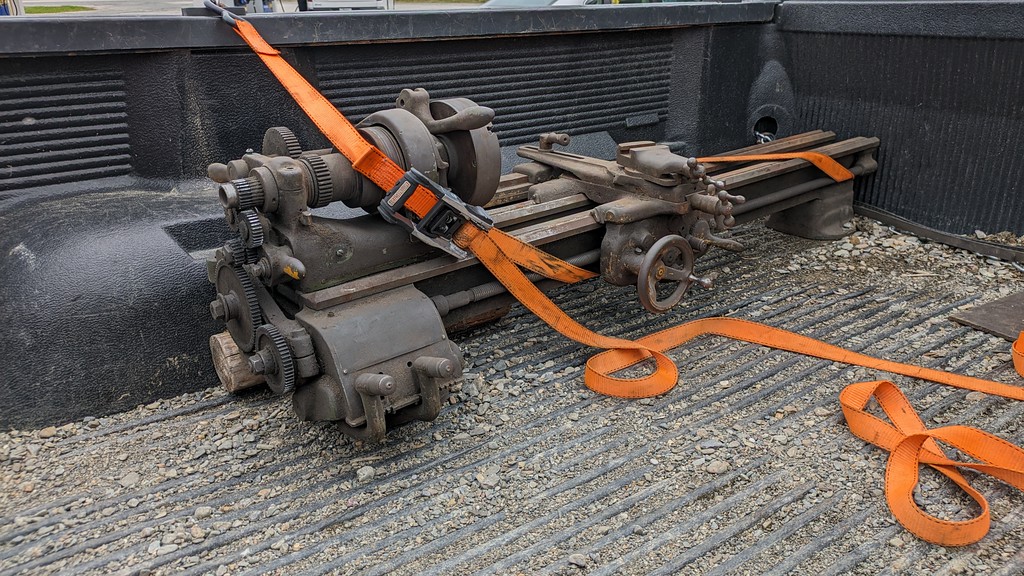
I did not hear or see the lathe run, one look at the rotted power cord and there was NO way I wanted anything to do with powering it up. The whole thing is absolutely caked in some kind of black crap that turns you the same colour if you get too close to it. Loading this was an adventure. Anyway, got it home a couple weeks ago and it's where it landed.
So here's what I observed.
- There is wear on the ways but I've seen a lot worse.
- The quick change gearbox shifts with difficulty through all the settings but they all appear to work.
- The original clamp for the tail stock is gone and someone kludged together one that works by welding a bolt to a piece of plate.
- The back gear shaft was taken off at one point and put back together wrong, i.e. the cams are out of phase so it's stuck
- Looks like someone HAMMERED on the shaft to get it to go together (square peg/round hole comes to mind)
- Still with the back gear, someone tried to drive a tapered pin through from the small side.
- The piece de resistance here, since the back gears are cocked off crooked, someone managed to smash at least six teeth from the small end gear and possibly at the same time broke one of the bull gear teeth.
The plan is to clean the crap off it in pieces until I can get the machine reassembled in my basement. Metalworking in an unheated garage is no fun from about December to April.
So tonight was step one. No real before photos since I was covered in diesel trying to scrub the crap off the counter shaft assembly. Here are some after pics.
Doesn't look so bad here.
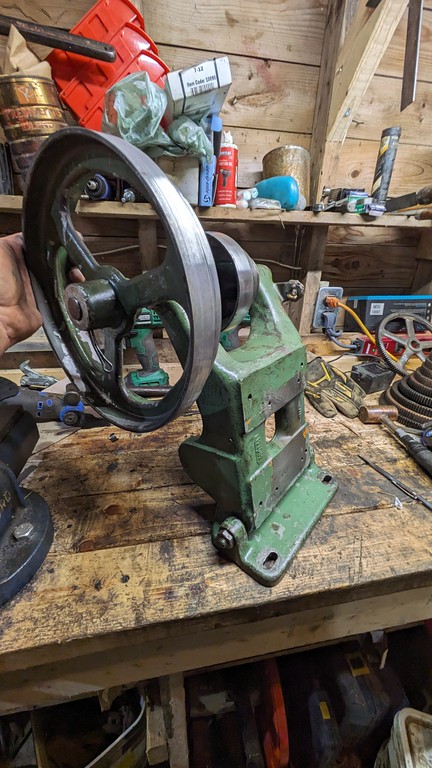
I really am glad I didn't meet the previous operator.
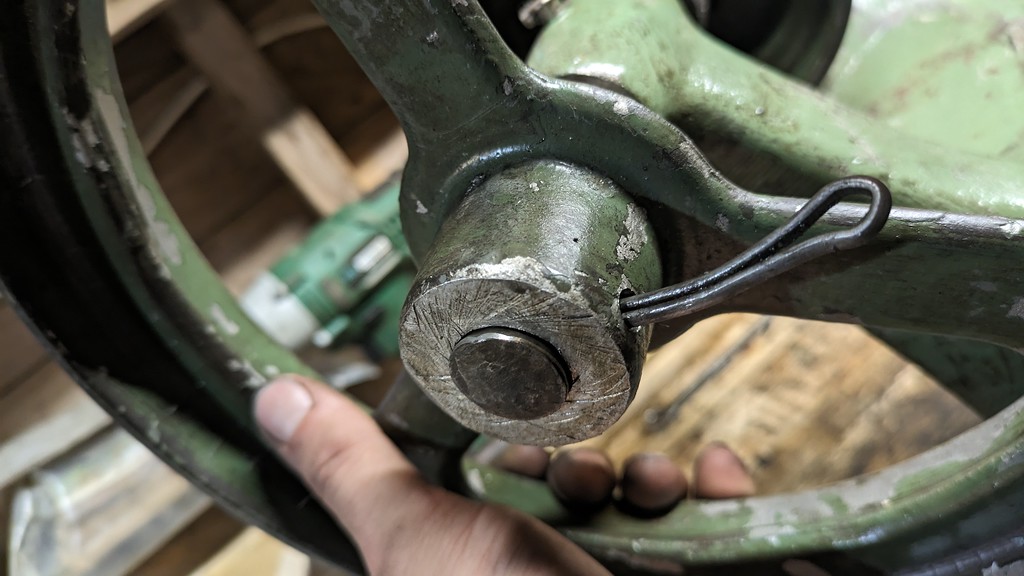
I forgot to clean the shaft collar so that gives you some idea of how much crap is caked on.
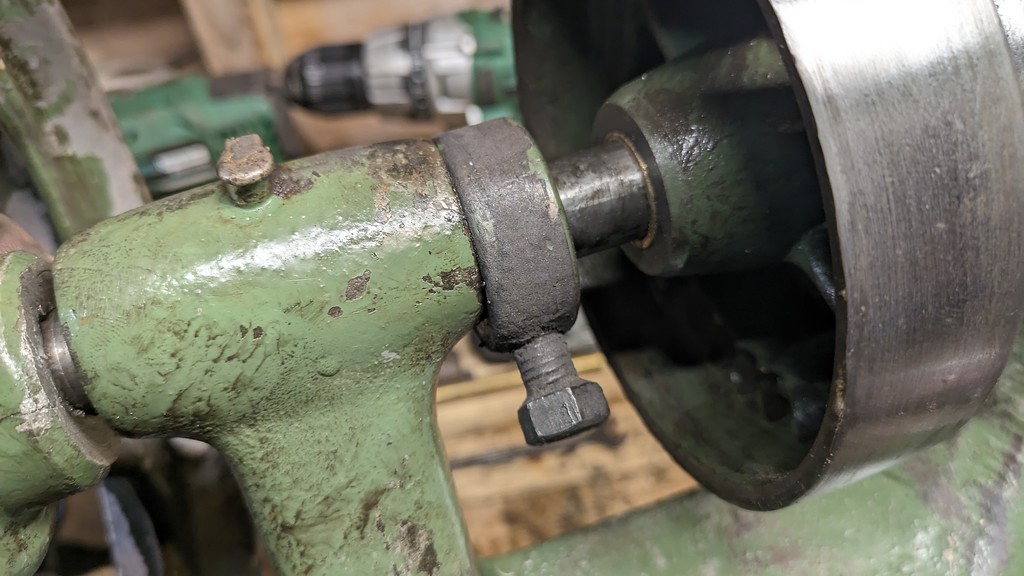
That doesn't look right.
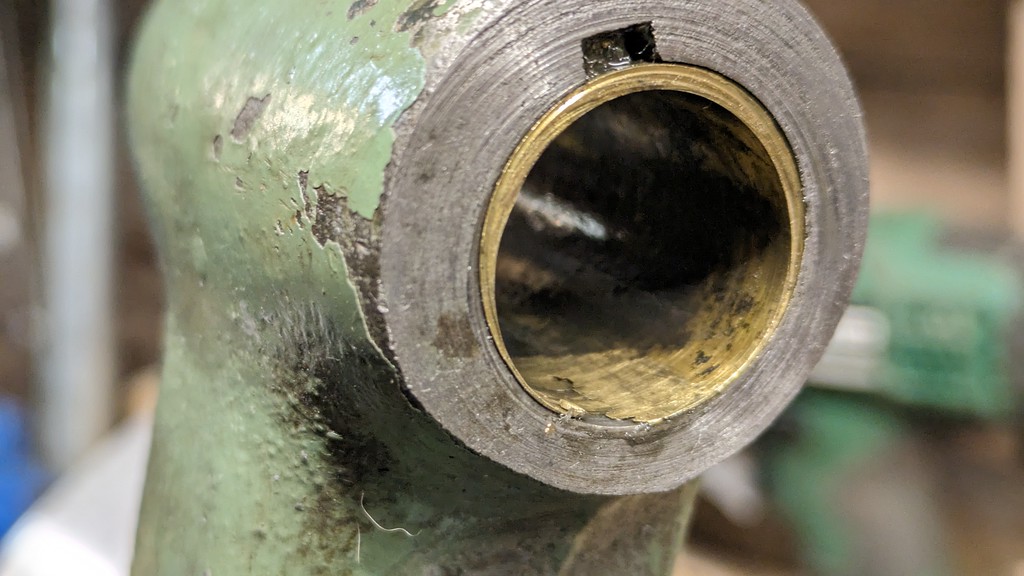
Nor does this on he other side...
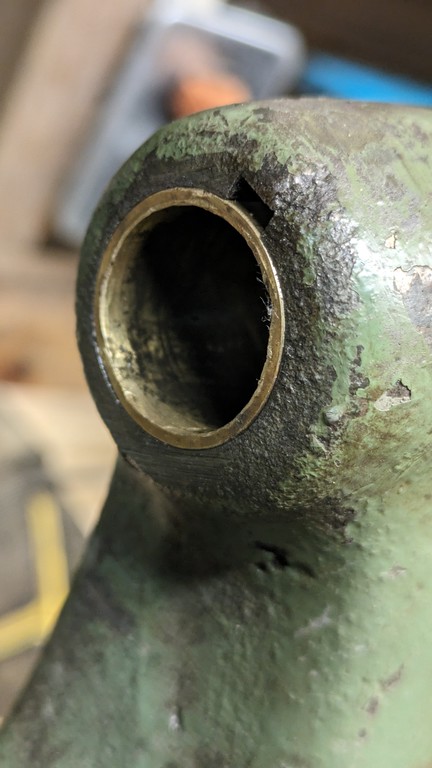
I understand re-sleaving it, but for the material cost and effort, make it go all the way through!

Can't say anything about this, my skill is probably worse. I'll go at this with a file.
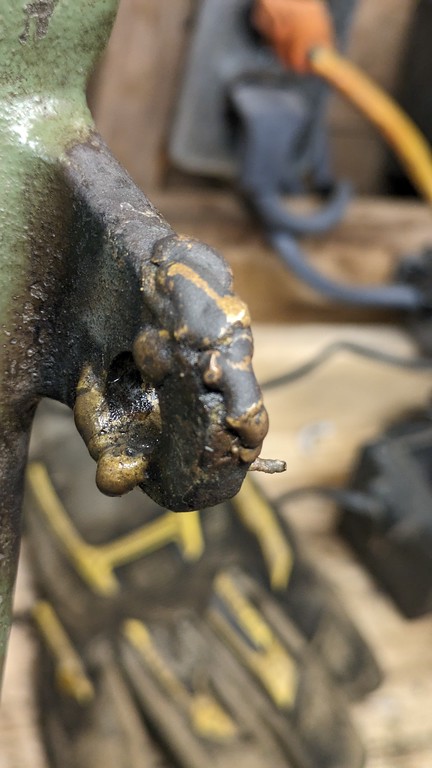
Well, that's not right.....
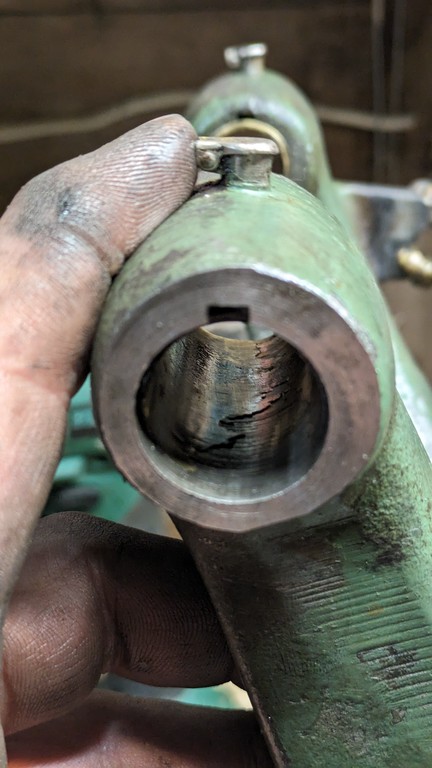
Know why they resleaved it. That's +0.025" tolerance!
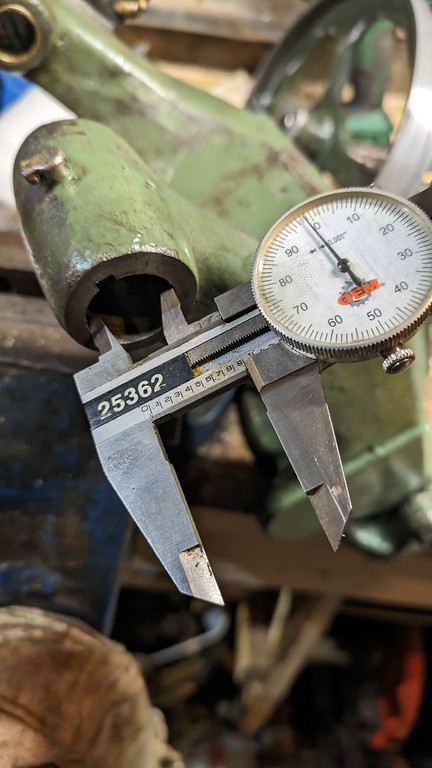
Other side looks closer to 7/8"
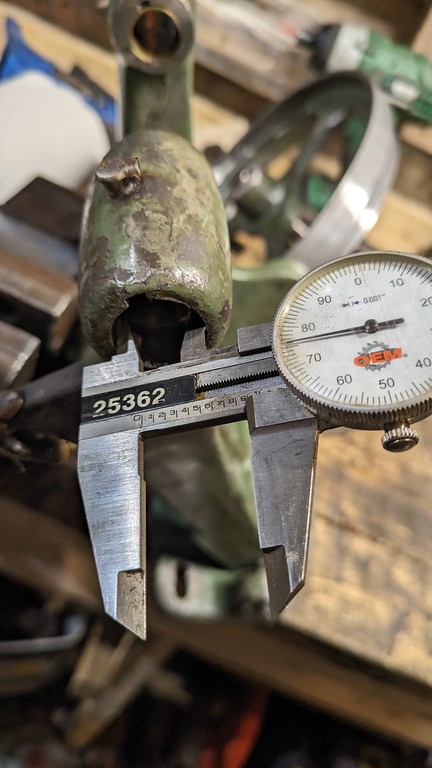
Got to take up the slack somehow.
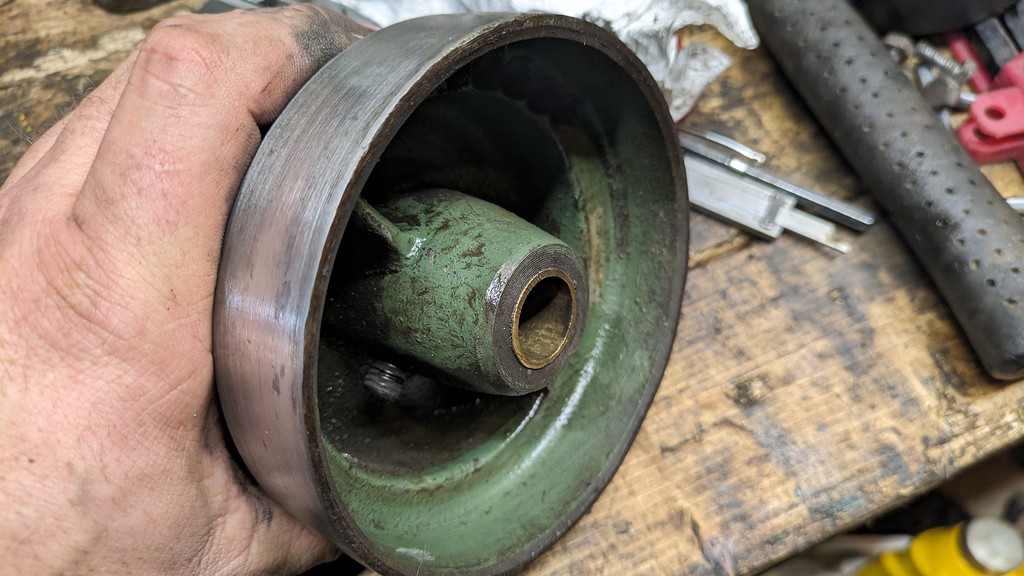
That's not 7/8ths!
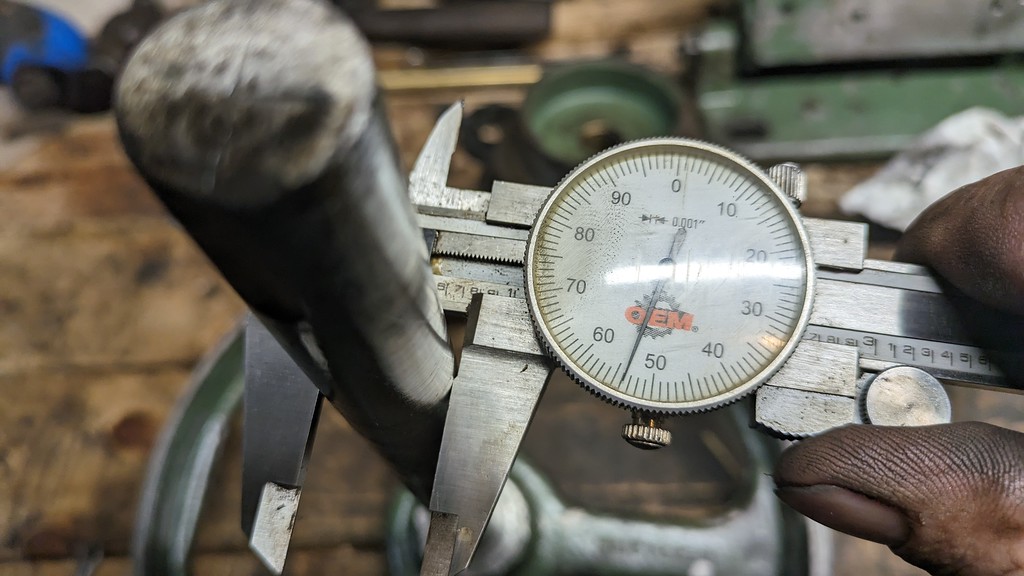
Doesn't matter how big your bench is.....
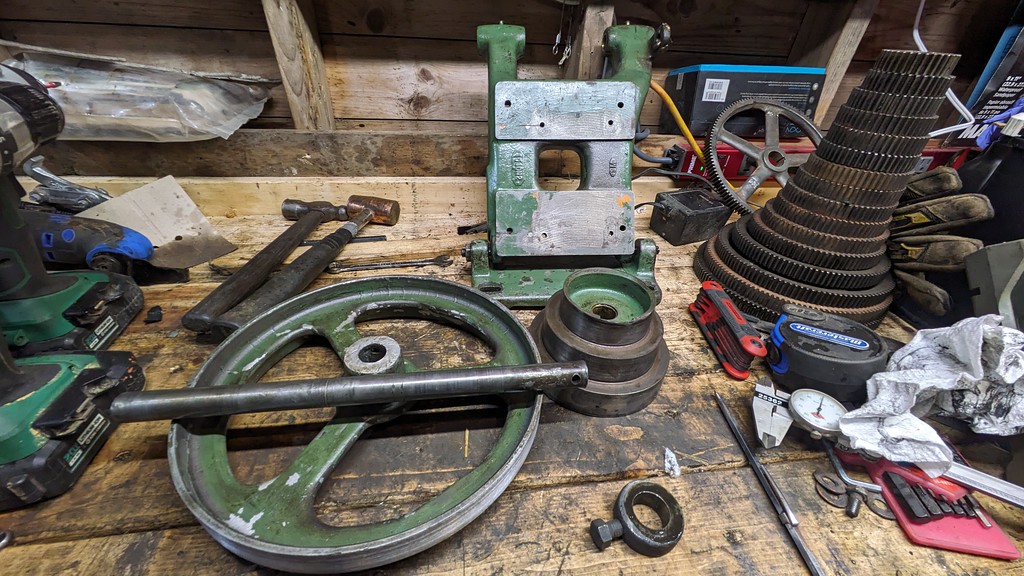
When the time comes, I don't think I'm going to bother farting around with this fire starter/electrocution device.
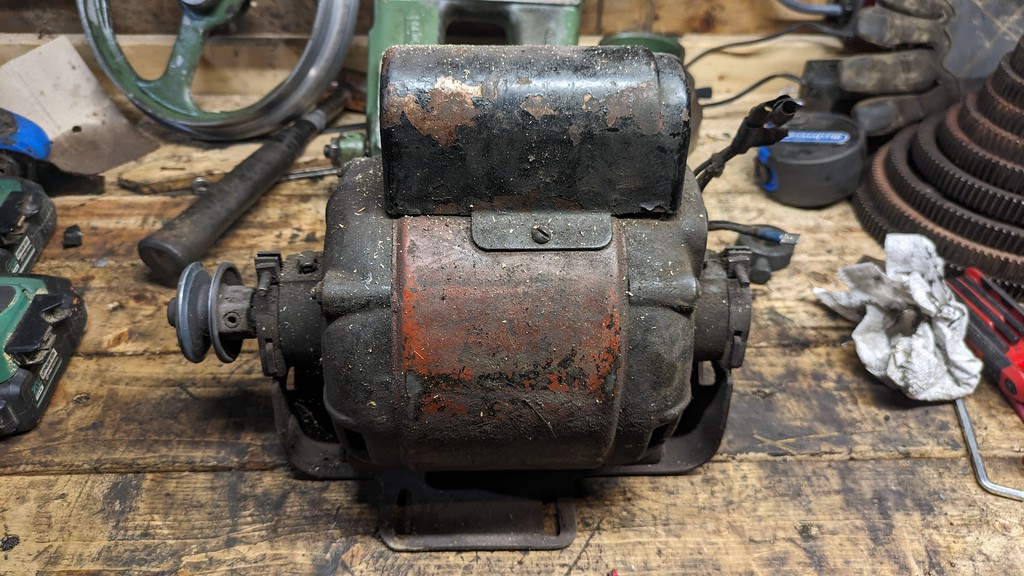
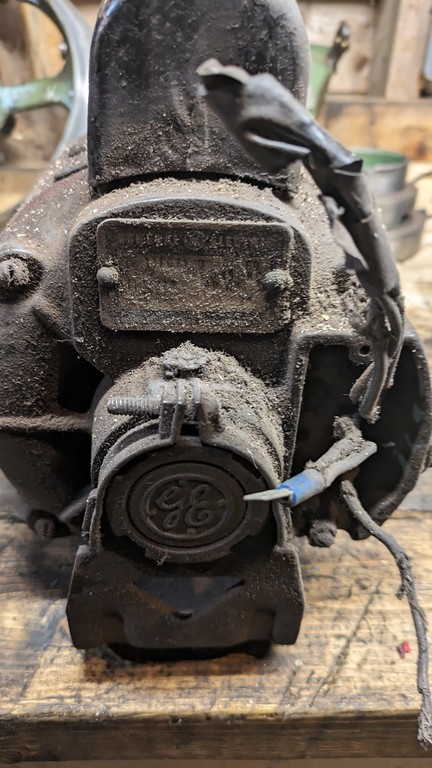
110/220. That wasn't yesterday.
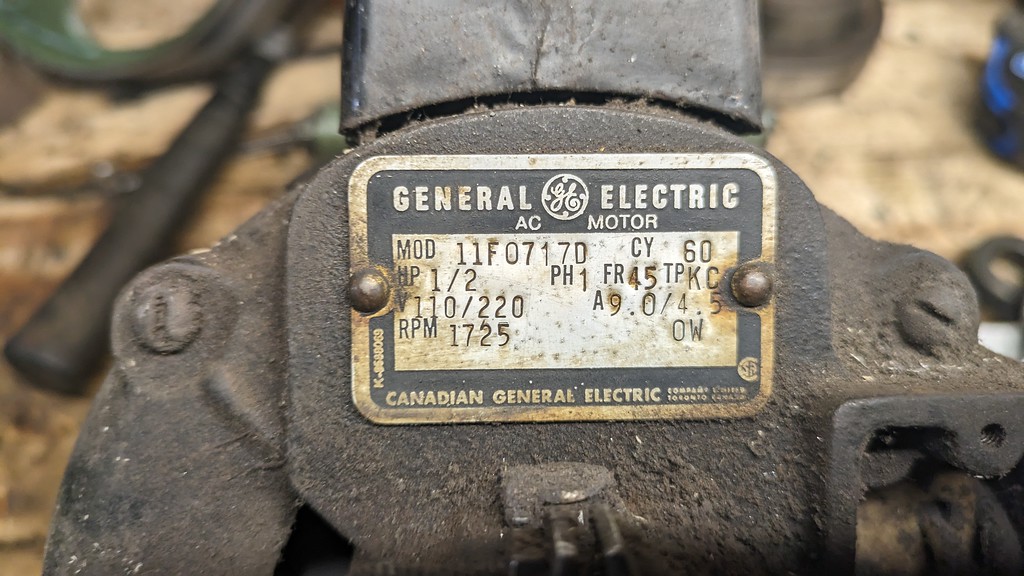
Yeah, no.
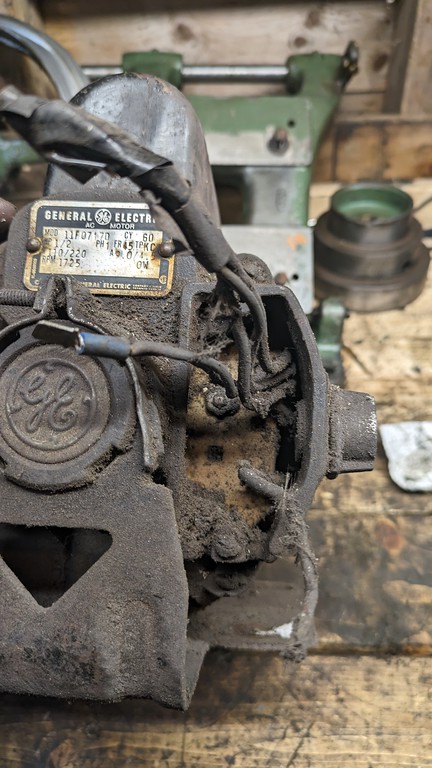
Yetch!
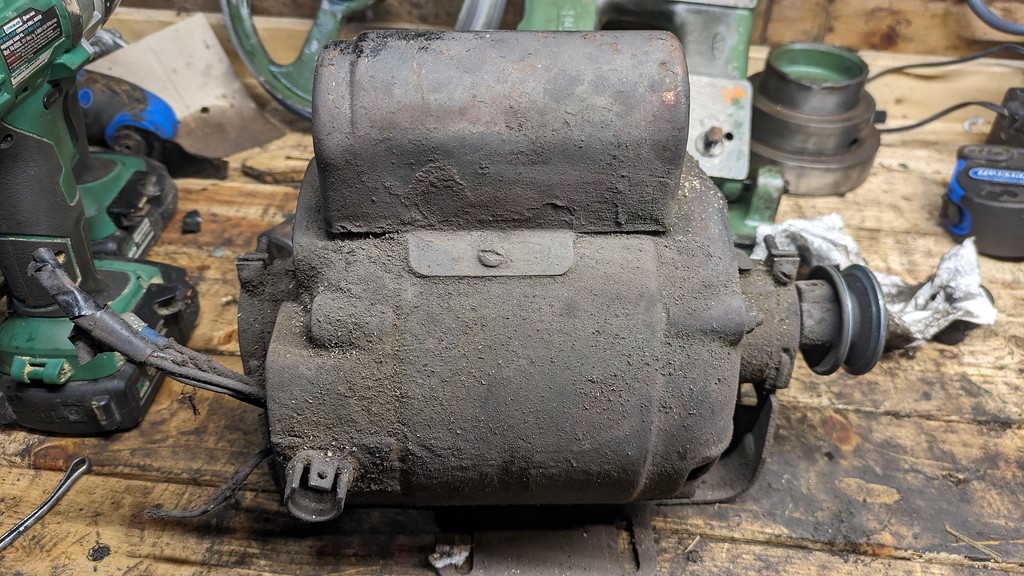
And finally, this really rots my socks. How much does a piece of key stock cost?
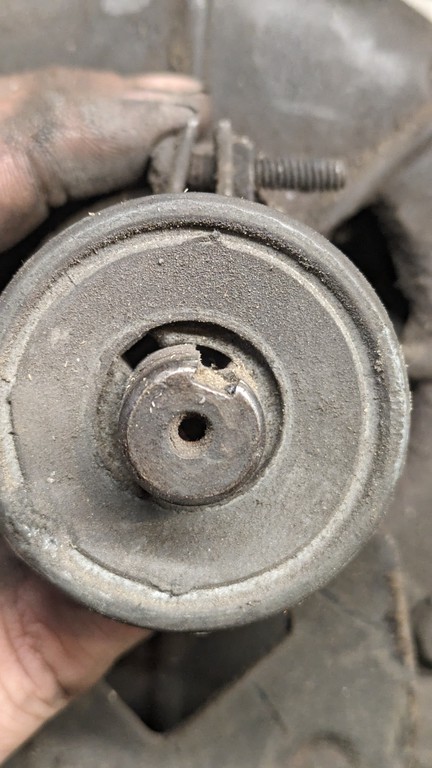
So this ought to be an interesting project. First off I think I'll bore those clapped out journals out and make some proper oil bronze inserts. I know there's supposed to be a wick there but a nice close fitting oil bronze bushing with a nice smooth shaft will go a long way to improving things. And I plan on drilling out the oil hole into the bushing.
God alone knows what other interesting things I'll find as I tear into it. Best case I have a usable lathe at the end of the day and I learn a lot. Worst case, I clean up and sell usable bits and pieces to recoup cost, scrap the rest and I've still learned a lot. I'll be working on this as time, ambition and other projects and chores allow so updates will be catch as catch can.
Please feel free to join in with a heartfelt round of "What in the hell were they THINKING?" I'm sure that among other things will be said quite often.