I'm attempting to make a 3/16" keyway broach for use on my lathe.
I'm using a remnant of 4340 I got from @John Conroy (Thanks John!).
I'm to the point of creating the cutting edge and hardening it. At what angle should I grind the edge to? For hardening I was planning on heating the edge to cherry red and quenching in water. Any feel for how long I would need to maintain the critical temperature? I have read 1 hour per inch of thickness. The blade is 3/16" X 1/2". This tool shouldn't see any shock loading. Is annealing necessary?
I guess the other question is, do I harden and grind the edge in or grind the edge and harden it?
Any input is appreciated. I'm exploring new territory here.
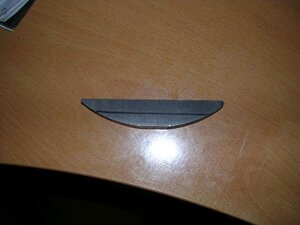
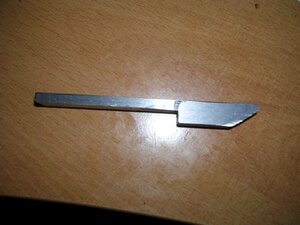
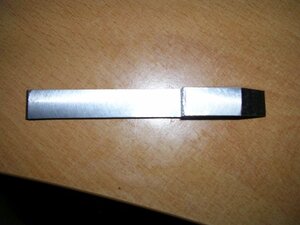
I'm using a remnant of 4340 I got from @John Conroy (Thanks John!).
I'm to the point of creating the cutting edge and hardening it. At what angle should I grind the edge to? For hardening I was planning on heating the edge to cherry red and quenching in water. Any feel for how long I would need to maintain the critical temperature? I have read 1 hour per inch of thickness. The blade is 3/16" X 1/2". This tool shouldn't see any shock loading. Is annealing necessary?
I guess the other question is, do I harden and grind the edge in or grind the edge and harden it?
Any input is appreciated. I'm exploring new territory here.
Last edited: