12- carbon
Andrew
To start, I'm a hobbiest amateur.
I have a component that I have modeled. I'm looking to have this sent off and machined but I'm not sure I understand machining tolerances etc.
There are a few things like the 4 peripheral mount holes, central mount holes, center bore that need to be maintained within a reasonable tolerance.
This is where my understanding of tolerance falls apart.
The largest dimension of this unit is about 97mm
If I get it machined to a tolerance of 1/1000 then the largest dimension of the bolt holes should still working out...
...But This can't be how things work out. This would mean that any part that needs even slightly better tolerance over a certain size would not be possible to manufacture.
...So this is not the correct understanding. There must be a level of tolerance lower than 1/1000 that would get me a component that still fits well within my needs.
Finally to my question:
What level of machining tolerance does one need for a component? More importantly, how is it defined and how does it play out on a component such as this?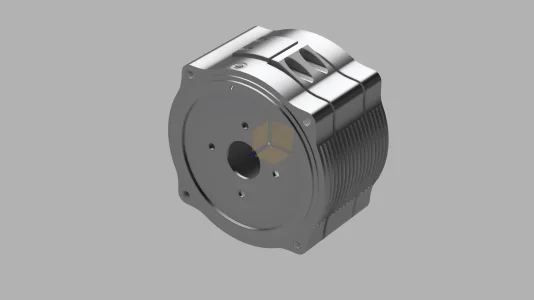
I have a component that I have modeled. I'm looking to have this sent off and machined but I'm not sure I understand machining tolerances etc.
There are a few things like the 4 peripheral mount holes, central mount holes, center bore that need to be maintained within a reasonable tolerance.
This is where my understanding of tolerance falls apart.
The largest dimension of this unit is about 97mm
If I get it machined to a tolerance of 1/1000 then the largest dimension of the bolt holes should still working out...
...But This can't be how things work out. This would mean that any part that needs even slightly better tolerance over a certain size would not be possible to manufacture.
...So this is not the correct understanding. There must be a level of tolerance lower than 1/1000 that would get me a component that still fits well within my needs.
Finally to my question:
What level of machining tolerance does one need for a component? More importantly, how is it defined and how does it play out on a component such as this?
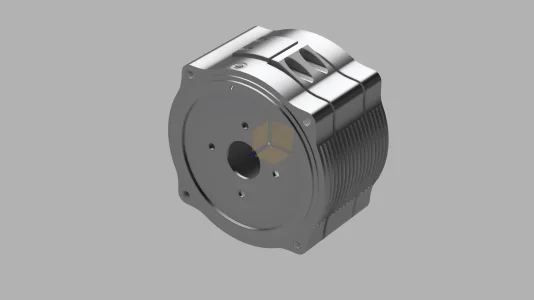