francist
Super User
In reply to another post I included a glimpse of my grinding setup that I built for sharpening milling cutters and there seemed to be a bit of interest to see more about it. So with that in mind, I’ll provide a little more substance here but probably break things into a couple parts lest it get too bulky.
First off, this setup is just what works for me. We all have our own needs and our own styles of working, as well as our own tolerances for what we find acceptable as an end product. I enjoy the chase of coming up with a design, it needs to function smoothly for me without a lot of fussing, and I want it to look good at the same time. Only three criteria — simple
In my shop things tend to evolve and morph as I discover new ideas or skills. The grinding station is no exception and really just started out as a way to sharpen HSS lathe tools. Coming from a woodworking background I like a hollow grind, and that typically requires a solid tool rest for consistency. Most built-in grinder rests are somewhat flexy owing to flimsy material and single-point mounting, at least on smaller grinders anyway. And they usually rely on a thumbscrew or two that is always painfully small and impossible to tighten. I dispatched with both of those concepts and built a rest that stands directly off a solid base platform.
The toolrest table itself is 3-1/2” x 3-1/2” only because I happened to have a small stack of pieces as salvage from a local stove factory. It’s 3/16” thick and has a notch to clear the wheel but only by a sixteenth or so on either side. It’s also easily exchanged for other versions if needed although I have yet to require that.
Angle adjustment is furnished by pitching the leading edge (closest to the wheel) up or down relative to a fixed hinge at the rear. The elevation changes are obtained by using a turnbuckle which raises and lowers cleanly and very controllably, but also holds the position so there’s no need for a locking nut or secondary action. One hand can hold the bit or reference angle, the other adjusts the table with the turnbuckle, and that’s it, grind. Fore and aft movement (towards or away from the wheel) is accomplished with two jig-fixture knobs threaded into the base platform through slots in the base channel.
The remainder of the “standard rest” was in anticipation of having to adjust positioning more than I actually have to. Other than table angle and wheel proximity, the rest stays configured in one position all the time. One thing to understand about this concept is that it does away with what some people regard as “the safety feature” of a single-pivot rest. If they jam a bit between the table and the wheel, they want the table to swing down and away and not continue to jam. Mine will not do that although I have yet to ever get anything jammed in it either. Your call.
The second half of this rig, and the part that drew the attention I think, is what I most recently made for sharpening end mills and horizontal cutters. It also proved to be the opening into a large and cavernous rabbit hole from which I have yet to find my way out....
More in Part II
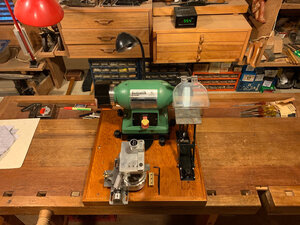
First off, this setup is just what works for me. We all have our own needs and our own styles of working, as well as our own tolerances for what we find acceptable as an end product. I enjoy the chase of coming up with a design, it needs to function smoothly for me without a lot of fussing, and I want it to look good at the same time. Only three criteria — simple
In my shop things tend to evolve and morph as I discover new ideas or skills. The grinding station is no exception and really just started out as a way to sharpen HSS lathe tools. Coming from a woodworking background I like a hollow grind, and that typically requires a solid tool rest for consistency. Most built-in grinder rests are somewhat flexy owing to flimsy material and single-point mounting, at least on smaller grinders anyway. And they usually rely on a thumbscrew or two that is always painfully small and impossible to tighten. I dispatched with both of those concepts and built a rest that stands directly off a solid base platform.
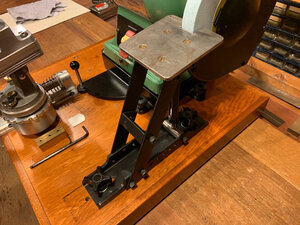
The toolrest table itself is 3-1/2” x 3-1/2” only because I happened to have a small stack of pieces as salvage from a local stove factory. It’s 3/16” thick and has a notch to clear the wheel but only by a sixteenth or so on either side. It’s also easily exchanged for other versions if needed although I have yet to require that.
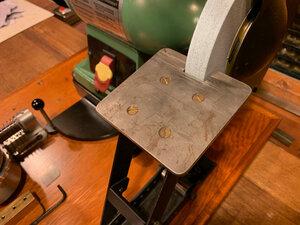
Angle adjustment is furnished by pitching the leading edge (closest to the wheel) up or down relative to a fixed hinge at the rear. The elevation changes are obtained by using a turnbuckle which raises and lowers cleanly and very controllably, but also holds the position so there’s no need for a locking nut or secondary action. One hand can hold the bit or reference angle, the other adjusts the table with the turnbuckle, and that’s it, grind. Fore and aft movement (towards or away from the wheel) is accomplished with two jig-fixture knobs threaded into the base platform through slots in the base channel.
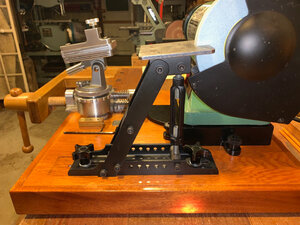
The remainder of the “standard rest” was in anticipation of having to adjust positioning more than I actually have to. Other than table angle and wheel proximity, the rest stays configured in one position all the time. One thing to understand about this concept is that it does away with what some people regard as “the safety feature” of a single-pivot rest. If they jam a bit between the table and the wheel, they want the table to swing down and away and not continue to jam. Mine will not do that although I have yet to ever get anything jammed in it either. Your call.
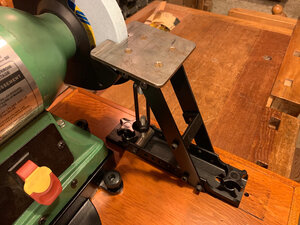
The second half of this rig, and the part that drew the attention I think, is what I most recently made for sharpening end mills and horizontal cutters. It also proved to be the opening into a large and cavernous rabbit hole from which I have yet to find my way out....
More in Part II